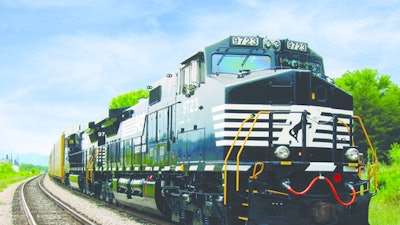
In the past 20 years, global rail freight activity has seen a dramatic increase. This mega-trend is set to continue over the next 20 years as cities grow, populations expand, and geopolitics become more complex. Driven by new emerging power structures and resource pressure, accountability and agility are prioritized as the landscape shifts.
Environmental, social and governance (ESG) considerations have been fully embraced, with high expectations around emissions, provenance and safety. Data capabilities have also become more sophisticated and relevant. This offers the rail freight industry the ability to drive growth through improved asset disposition and utilization and creates new revenue streams based on the data collected through digitalization.
The rail freight industry was valued at $247 billion in 2020 and grew to reach $271 billion in 2021. As population centers demand robust transportation services, rail cargo offers an optimal solution. Rail cargo is five times less polluting than road transport, safely keeps hazardous goods away from the public and is predictable and energy efficient.
However, for rail freight to be maximized, railroaders and rail supply chain leaders must put data to work for better real-time visibility. Of the 5 million railcars in operation globally – of which roughly 1.7 million serve the United States – only about 8% are currently digitalized. This represents a massive opportunity to create value adding data-driven services that all participants need.
Stakeholders in rail freight are demanding greater visibility and accountability. Cargo owners and shippers want to know, without a doubt, that their goods will arrive on-time and in-full (OTIF). Rail fleet owners, repair workshops and transport hubs need accurate information to manage operations, improve service availability, maximize fleet utilization, optimize maintenance and extend product life cycles. The knock-on-effect is that cargo customers, shippers, manufacturers and retailers all get more reliable, cost effective and high-quality transportation. And better data is the ultimate solution to improve processes, capabilities and overall visibility.
The missing link
Forward-looking rail freight operators are joining the data revolution.
They are choosing to invest in sophisticated Internet of Things (IoT) sensor gateways, connectivity and powerful data analytics to leverage new value from digital asset fleets and infrastructure. Entire fleets of railcars are being equipped with zero-maintenance hardware devices to send essential data in real-time to an intelligent, secure cloud. Each IoT device makes it possible to monitor a specific railcar or cargo’s conditions, utilization, handling and maintenance. The device generates data on the asset’s location, load status, placement conditions, security and wear on moving parts like brakes, bearings or access points.
This data is brought to life using the most advanced algorithms. The combination of hardware devices, and software analytics not only supports necessary real-time decisions, but also reduces energy consumption and supply chain risks while boosting the supply chain’s efficiency. When root causes can be identified, leadership can take action to avoid this situation in the future. This may include ordering more training, closely monitoring third parties and managing billing differently.
IoT devices and Big Data analytics allow operators to fully utilize their fleet and gain new insights to drive a step-change in customer service and profitability. Installing sensors on valuable rolling stock transforms the railcar itself from a hunk of steel into a connected agent that can drive processes aligned with the wider supply chain ecosystem.
IoT keeps rolling stock in service
IoT technology increases railcar observed availability from day one. According to Nexxiot's research, using sensors to track actual railcar mileage can optimize maintenance cycles and deliver annual savings of as much as $430,000 for a fleet of 1,000 railcars. One key metric that determines profitability in rail freight transport is fleet uptime, which is the ability to keep transport assets running. Maintenance managers must make decisions whether to repair or replace essential components. Limited data makes it difficult to optimize parts without risking safety. With highly accurate mileage data for every single asset, plus data gathered from brakes and other critical sub-systems, the decision making becomes easy.
As for brakes themselves, they are by design perpetually in the process of wearing out. The rate of wear depends on many factors – the number of stops and starts, the weight of the asset and cargo, the miles traveled, cumulative elevation, train-handling practices and the components being used. IoT sensors collect and transmit brake data at a resolution where, with the right software tools, industry leaders can apply advanced decision-making to optimize repairs and maximize the value of their assets.
Improved brake maintenance enhances the service life of a railcar and the client experience. It improves safety standards and creates better visibility on portfolio management. This means more capacity, greater flexibility and improved fleet uptime so assets are serving customers rather than sitting in the workshop.
Other supply chain pressures affect availability
It is increasingly difficult to attract “hands-on” railroad workers to walk tracks, perform inspections and identify defects. In remote, dangerous locations and under adverse conditions, digital asset monitoring makes it possible to test brakes automatically from anywhere and deploy human experts once a problem is understood. They are armed with the right equipment, information, and location before they even set off to the site. With the right information in hand, railroaders work more safely and efficiently to get the task done.
The supply chain is under pressure from cargo shippers’ heightened expectations. They expect visibility, API data on availability, arrival times, risks, conditions, and want safeguards on security, quality and sustainability. With real-time health monitoring of brakes and other critical systems, operators have the metrics to assure stakeholders that rail freight is a reliable, preferred option.
While trucks offer predictable and reliable transportation and cover the first and last mile of the journey, rail is the most sustainable mode of land transportation. On average, rail is 11 times more energy-efficient than trucks and twice as efficient as water and pipeline use on a ton-mile basis. But to make efficient cross-modal transport a reality, trucks must be seamlessly aligned with available, well-maintained rail assets. Cross-modal transportation is more sustainable than door-to-door truck transport, plus it cuts transportation costs, boosts public safety and creates more options for cargo owners. IoT sensors and data analytics make efficient, profitable cross-modal freight a reality.