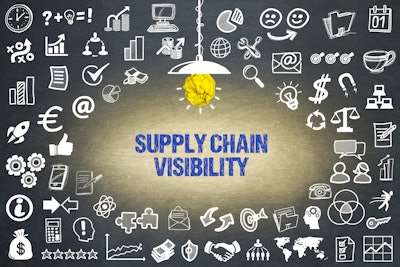
In the face of historic supply chain disruptions, most manufacturers took a “band-aid” approach, planning for longer lead times or hoarding materials rather than addressing the fundamental problem: a lack of visibility into their suppliers’ operations.
As the supply chain crunch begins to slow for the time being, manufacturers may be tempted to stick with the status quo. That would be a mistake. If we’ve learned anything these past 2.5 years, it’s that the global marketplace changes fast and more disruption is likely on the way. Just last quarter, nearly half of manufacturing executives survey said that supply shortages were their leading operational challenge.
The good news is that digital tools can help – and now, this moment of “relative quiet,” is the ideal time to adopt them. Here’s what executives should know.
Why visibility is key
For manufacturers, a lack of insight into suppliers’ operations can lead to setbacks, including poor asset utilization, quality issues and revenue loss.
Take a contract manufacturer for example. With demand growing, a particular contract manufacturer suddenly found it couldn’t get the supplies needed to package the product. When the packages finally arrived, small variances in the materials, for which their machines weren’t optimized, caused the packaging to tip over. This caused significant downtime, extensive waste, scheduling problems and substantial hits to the company’s revenue.
What they didn’t know was that their customer, who was responsible for buying and sending the materials, had started using a different vendor. If they had – and if there was more visibility into that new vendor’s timing and specs – they would have adjusted their production schedule, optimized equipment settings, and even charge back their customer for any loss in value.
Unfortunately, this is a fairly common occurrence: in a 2020 Gartner survey of supply chain leaders, roughly 80% said they had insufficient visibility into their supply chains. In a West Monroe Q2 customer and industrial products executive poll, nearly three-fourths of executives said their technology processes, which can help improve visibility, required the most attention to improve their operations.
Using technology to improve visibility
Technology can help, but where should manufacturers start? Here’s the data needed to improve visibility, what technologies they need to capture and share this data, and some key best practices for working with their suppliers.
What kind of data is needed
Ideally, a manufacturer should have insight into key elements along their supply chain, from product development through sourcing, assembly, distribution and logistics, to the point of consumption. Consider your ability to track your order from the warehouse, so the company knows precisely how much of each product coming off the line costs.
Starting this journey involves collecting information from suppliers about:
· Raw materials, including quality and technical specifications, certificates of analysis, ultimate source, n-tier supplier mapping, etc.
· Transportation logistics, basically who’s shipping the materials? What are their schedules? Are there backups? Can you track shipments?
· Lead times, i.e., gaining a better understanding of when materials may arrive based on the above logistics, what other businesses your vendor is supplying and how much of that supply is already accounted for from other customers at a given time.
The technologies that can help
Technology can unlock supply chain visibility for manufacturers, largely by breaking down silos internally and among their suppliers to centralize critical data. At a high-level, key technology elements include:
· A shared data platform (e.g., a unified namespace) that enables anyone along the supply chain to publish and share their data to others – from machine data on a factory floor to transportation schedules to technical specifications. This allows manufacturers to get ahead of potential specification or supply disruptions. For example, if an organization knows a component will run out of supply in four weeks, they can work with the supplier to find an appropriate substitute. Market interest in control tower technology continues to grow to accomplish consolidated supply chain network visibility.
· Extending enterprise resource planning systems (ERPs) to connect with the supply base and logistics partners. This presents purchase orders for acceptance and editing through a shared browser, thereby improving inbound visibility of raw materials or finished goods.
· A supplier portal, where suppliers can make necessary updates and collaborate with the manufacturer’s data team to extract needed data from their systems.
· Artificial intelligence/machine learning systems, which, once the above is in place, can use that data for predictive analysis to improve planning forecasts and run simulations for specific disruptions.
Best practices
Manufacturers can’t force their suppliers, many of whom might still run off spreadsheets, to engage in this process. That’s why communication and incentives, such as longer contracts for vendors that participate in a supplier portal are key to getting buy-in. In initial conversations, be sure to understand what their current digital maturity level is and what business models and technologies are already in use.
Remember, there’s no one path forward. Think about what you can do internally as you get started with your suppliers – for example, do you need to adopt a transportation management system? Understand that it’s a give-and-take relationship: identify at the outset what data you need and what data you’ll be willing to share.
Don’t forget about demand
COVID-19 did more than shake up supply chains. It wreaked havoc with manufacturers’ abilities to assess demand as ongoing disruptions make it more complicated to use data collected over the past few years for planning efforts.
This underscores how critical it is for manufacturers to gain better visibility into their suppliers and highlights the need for effective supply chain simulation tools and supplier mapping to help assess the array of what-ifs they may face.
While supply chain strains may appear to be leveling out at this moment, future disruptions loom. Now is the time for manufacturers to adopt the technologies they need to gain more visibility into their suppliers and improve their resiliency before the next wave of upheaval.