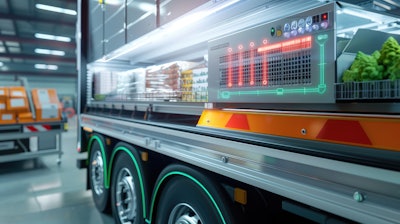
Cargo theft is no longer a background risk—it's a frontline threat. In today’s global food and beverage (F&B) industry, where cold chain shipments are increasingly complex and fragile, theft has emerged as a key vulnerability.
In 2024 alone, total reported cargo theft losses reached nearly $455 million. Food and beverage shipments are among the most frequently targeted, making up 32% of stolen goods. And the trend shows no signs of slowing down—with a projected 35% increase in total incidents by the end of 2025, according to Verisk’s CargoNet.
With a surge on the horizon, there’s a lot on the line. To protect their goods and preserve integrity across the chain, F&B organizations must move from reactive to proactive, with real-time visibility, trusted partnerships, and a smarter, more agile mindset.
Why the F&B cold chain is especially vulnerable to cargo theft
Cargo theft in the F&B sector isn’t just rising—it’s evolving. Sophisticated criminal networks are leveraging technology, insider access, and deep logistics knowledge to exploit vulnerabilities in the cold chain. Food shipments, in particular, offer an appealing combination of high resale value and low traceability—making them an increasingly frequent target.
Unlike standard freight, cold chain shipments must be maintained within precise temperature ranges throughout often lengthy journeys—passing through multiple carriers, cross-border checkpoints, and storage facilities. Each of these “touchpoints” adds complexity and more opportunities for theft, tampering, or spoilage. This intricate network makes food and beverage logistics one of the most fragile segments in global supply chains. In fact, 41% of cargo thefts occurred during transit in 2024.
Several factors have intensified the threat. Criminals target food and beverage cargo not just for its high value and consumer demand, but because it's difficult to trace once stolen. Unlike serialized goods like electronics or pharmaceuticals, food products aren’t frequently barcoded or serialized for shipment. Geopolitical tensions and rising tariffs also play a role, increasing the declared value of goods and making each shipment a more attractive target. At the same time, legacy tracking systems and fragmented logistics networks leave blind spots. Without real-time insight into where goods are and what condition they're in, organizations are left reacting after damage or theft has already occurred.
Temperature monitoring plays a critical role in closing those gaps. While vital for reducing spoilage risk, it also acts as an early warning system for broader security threats. A sudden spike during an unscheduled stop in a known hotspot might signal a breach in progress. Fortunately, solutions exist that not only fill these visibility gaps but also deliver broader operational benefits. For example, temperature monitoring doesn’t just reduce spoilage. It can serve as an early warning system for theft or tampering, like a sudden temperature spike in a truck that’s unexpectedly idle in a known theft hotspot.
But even the best technology can’t function in a silo. Protecting cold chain cargo requires an evolved strategy and a multi-layered approach; one that combines real-time intelligence, network flexibility, and operational agility to create empowered teams. Leading F&B companies are already making this shift. Here’s how they’re strengthening security while building more resilient supply chains.
1. Turn visibility into action
Visibility is no longer a value add; it’s the foundation of cold chain protection. According to recent data, 60% of companies now use IoT-enabled shipment tracking—up from 55% the previous year.
Modern visibility tools use IoT-enabled trackers and environmental sensors to provide shippers with a full view of a shipment’s condition. This technology can monitor temperature, light exposure, and route changes. Shippers will receive instant alerts when something goes wrong—whether it’s an unauthorized door opening, a temperature spike, or an unexpected stop in a high-risk area. The real advantage isn’t just in the data, it’s in the ability to act on it, which enables teams to quickly intervene before cargo is lost or compromised. In high-risk categories such as food and beverage, that kind of responsiveness can be the difference between a minor delay and a multi-million-dollar disruption.
2. Build a more resilient network
Technology is only one layer of protection: the next step is strengthening the ecosystem around your cold chain. That starts with choosing the right partners—logistics security experts, carriers, insurers, even law enforcement—to enhance the ability to respond quickly when incidents occur.
These partnerships also help uncover theft trends, optimize route planning, and strengthen protection in known hotspots. Expand your protective network by diversifying suppliers and logistics providers to avoid single points of failure. Use real-time visibility data to evaluate and select only secure, vetted partners and shipping lanes. At the same time, diversifying carriers and routes reduces reliance on single points of failure—enabling faster, safer rerouting when threats arise. By blending visibility with a more flexible and collaborative network, F&B leaders can move from static supply chains to systems built for responsiveness and control.
3. Empower people on the frontlines
A strong security strategy doesn’t just rely on better locks and tracking systems: it depends on people. In high-risk, fast-moving logistics scenarios, employees are often the first line of defense. A multi-million dollar technology investment is worth nothing if teams aren’t empowered with the right tools, context, and training to identify red flags, interpret real-time data, and escalate issues quickly.
When a Mexican confectionery company, for example, needed to protect temperature-sensitive candy during cross-border transit, it focused on building frontline confidence in using monitoring tools. The team was trained to track environmental conditions and location data in real time, providing situational awareness to respond proactively. That preparation proved critical when one of the trucks was hijacked near Mexico City. Thanks to the team’s real-time visibility into the shipment’s status and location, employees were able to coordinate with local authorities and recover the stolen vehicle and cargo—before damage or spoilage occurred.
In the food and beverage industry, where timing and temperature control are everything, incidents such as this underscore the importance of combining people, process, and platform. No system is immune to disruption, but a well-prepared team—equipped with the right information at the right time—can mean the difference between loss and recovery.
Final thoughts
Cargo theft isn’t a risk that can be eliminated, but it is a risk that can be managed. With the right combination of visibility technology, resilient networks, and trained teams, F&B organizations can protect more than their shipments; they can protect their brand, customer trust, and long-term profitability.
In a cold chain environment that’s only getting more complex, the companies that invest in smarter security today will be the ones still delivering tomorrow.