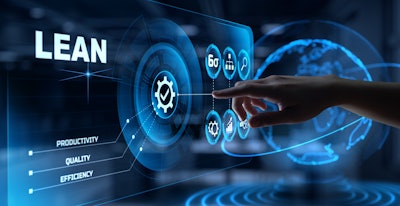
Supply chains have seen unprecedented volatility over the past few years, with the impact of Brexit, COVID-19 and now the war in Ukraine leading to delays and shortages with no easy solutions.
The current state of the supply chain
Goods are piling up in storage and ships are diverting or slowing down in major transit hubs. According to the Kiel Trade Indicator, 11% of goods are waiting on container ships worldwide, with most in China.
These material bottlenecks caused by the pandemic have led to significant production and transportation delays, which has meant businesses can’t refill their inventory stocks.
Increasing prices have also led to manufacturers struggling to commit to delivery prices for their clients, straining the relationship between manufacturer and supplier.
While the past few years have led to issues within the supply chain, it has resulted in the industry evaluating itself and investing in new strategies to make production more efficient. One of the most popular strategies is lean manufacturing.
What is lean manufacturing?
Toyota developed Lean to streamline manufacturing processes, as outlined in The Toyota Production System (TPS). One of the main goals of lean manufacturing is to reduce timescales within the production system and the response times from suppliers and customers.
Essentially, implementing lean strategies can help eliminate waste without impacting productivity.
Five principles make up the concept of lean and include:
- Define value: Find out what the customer is willing to pay for through interviews, surveys, demographic information and web analytics.
- Map the value stream: Use the values defined in step one to identify how to contribute to these values. Anything that doesn’t add value is considered waste and should be removed from the stream.
- Create flow: Once the waste is removed, changes should be made to allow the operation to run smoothly. For example, reconfiguring production steps, training staff to be more adaptive and more.
- Establish pull: Products should be created when needed with the correct quantity to meet demand.
- Pursuit of perfection: Making lean thinking and continuous improvement an everyday part of business culture.
By implementing these principles, manufacturers can be confident in the efficiency of their work processes and help improve what’s currently an unstable supply chain.
The benefits of lean thinking
Response in real-time
Lean manufacturing principles mean pulling products through the supply chain as and when required. To do so, lead times have to be reduced and suppliers and manufacturers must be near the customer.
There are tools commonly used in lean manufacturing, such as Kanban cards. Kanban cards are visual representations of work items that contain information about a task and its status, including its deadline, the person responsible for it and a summary of the assignment.
These cards allow manufacturers to respond to customers' changing needs in real time and improve the overall transparency of the work process.
Warehouses will experience lower excess inventory and fewer unscheduled product changes with more responsive operations.
Reduced waste
The biggest focus of Toyota's lean management principles is reducing waste.
There are seven wastes lean manufacturing operators should keep in mind to assess waste and usage in every warehouse process: transport, inventory, motion, waiting, overproduction, overprocessing and defects.
Eliminating these non-value added wastes will eliminate potential bottlenecks across the business, reduce lead times and create simpler distribution networks.
Improved product quality
Utilizing lean principles allows the quality of products and production to increase, meaning fewer errors for both customers and suppliers.
Reducing the quantities of materials, work in progress and finished stock will reduce overall inventory costs, allowing manufacturers to provide quality products at the lowest possible price for their customers.
By instilling the idea of continuous improvement throughout the company, production value will steadily increase and products will be created with the value customers expect.
Boost employee morale
When lean thinking is implemented successfully, employees will feel a positive impact. Workers know when their work is unnecessary, which will ultimately negatively impact morale.
Implementing lean principles means getting input and participation from employees as they’re well-placed to point out waste and inefficiencies in production.
Including staff in these processes benefits both business owners and empowers employees, gives them importance and makes them feel involved in improvements to the company, all of which will help boost morale and employee satisfaction.
Enhanced customer relationships
The lean approach focuses on customers by aiming to deliver the value they expect. By cutting out wasteful processes, companies can focus on building solid relationships and providing a service that makes every buyer feel special.
Building this foundation means all customer interactions will improve and lead to a steady flow of revenue.
The supply chain has seen unprecedented change over the past few years and the logistics sector has had to evolve to keep up.
From the ability to respond to issues in real time, reduce waste to increase revenue, improve product quality and boost employee morale, warehouse managers are turning to lean manufacturing. Most of all, lean thinking puts the customer first, meaning the value is at the forefront from production to delivery.