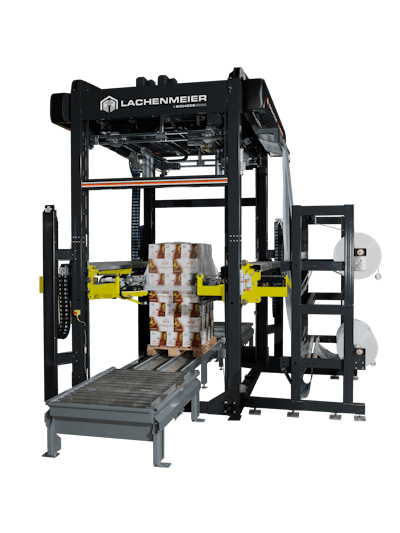
From consumer packaged goods (CPG) to frozen foods, effectively packaging pallets for transit demands solutions as unique as your product. Shrink hooding, conventional stretch wrapping and stretch hooding are the three most common wrapping solutions, each with their relative strengths and ideal applications within the transit packaging pipeline. Comparing these directly can lead to a highly detailed and granular discussion, so in the interest of providing succinct analysis let’s focus the lens in on one topic: Stretch hood wrapping technology. What are its benefits, which companies are more likely to achieve the fastest gains, and what are its latest advancements?
Many companies and organizations are moving to hooding technology. Traditionally popular in Europe, hooders are gaining a significant foothold in North America. A range of national and regional players in CPG, food and beverage and more are upgrading and automating their end-of-line pallet packaging with hooding technology. This is alongside continued adoption in corrugated, building materials and chemical industries.
What is driving this change? First, hooding technology provides an unmatched ability to protect palletized products from the elements and potential tampering, while also stabilizing loads for transport. The most advanced stretch hooders offer 5-sided protection and a throughput capacity of up to 200 pallets per hour. Second, significant cost savings can be achieved through reduced consumable use, lowered energy consumption and simplified material handling. Third is adaptability. Stretch hooders have the ability to be fitted with several film rolls, allowing them to wrap multiple load sizes and types with greater variations more quickly. The most advanced stretch hooders can host a variety of film patterns, including fully closed hoods, film sleeves, short hoods and film reinforcement capabilities.
The recent generation in stretch hooder technology features the replacement of traditional hydraulics with electrically operated stretch frames and machine frame movements. The electric frame allows for reduced safety area fencing, providing the flexibility of a smaller footprint to maximize valuable production floor space and the ability to be placed closer to a facility’s perimeter. The most advanced of this new generation also feature a steel-reinforced timing belt movement, providing greater reliability and lower maintenance costs, and greater compatibility with requirements in CPG and food and beverage operations. This also reduces dependence on lubrication, which is required for typical chain drive lift systems. Going to a belt-driven frame makes hooding solutions more compatible with clean operations that don’t allow exposed, lubricated components.
Bridging the gap between the newest electric units and the older technologies can be a challenge, but it highlights the importance of consumable and equipment interaction and performance. While easy to treat as a second thought, selecting the right film consumable for your operation requires due diligence at least equal to that of new equipment purchases. Multiple film options, including transparent, colored, perforated and printed, are available.
When going about the film selection process, there are several considerations to keep in mind. Along with the requirement for the film to provide the needed load containment, other factors include: Is brandability an issue? Is transparency important to optimize barcode-readability? Will your pallets be stored outside and demand films that protect from moisture?
On a global scale, stretch hooding technologies and investment have risen to greater levels of interest and attention. They offer great protection in transit packaging applications, are adaptable and productive at end-of-line and the newest generation provides lower physical footprints and maintenance savings. They don’t tell the whole story of an organization’s automation journey, but they do provide a valuable chapter in the quest for increased efficiencies, product protection and throughput. The integration of technologies, software systems and production lines is a necessity.