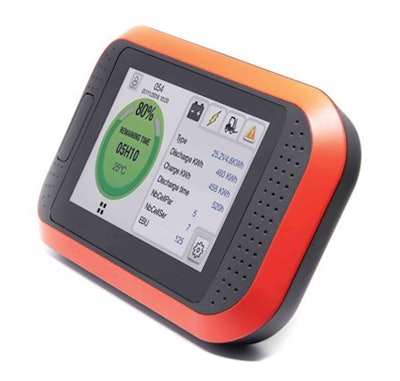
Mirroring the increasing implementation of lift truck telematics, the adoption of lift truck battery fleet management and monitoring solutions has been increasing over the last few years. In much the same way that a telematic system can uncover a range of data about day-to-day lift truck operations, these solutions can open a window into the battery fleet that will reveal many previously hidden opportunities for improvement. And, much like lift truck telematics, they offer capabilities that range from basic monitoring and troubleshooting to highly sophisticated fleet asset assessments, with potential cost savings at every level.
The basics: monitoring and troubleshooting
All battery monitoring begins with some form of on-board device that captures and monitors basic battery health and performance. Such metrics include amp hours (AH) charged/discharged, voltage levels, temperature levels and electrolyte (or “water”) levels of batteries where applicable. If missed or ignored, any or all of these issues can limit battery runtime and life, lead to premature battery failures and drive lift truck downtime.
Of course, simply capturing such data is useless unless it can be turned into actionable intelligence. Accordingly, the on-board units must save and share battery operating data with cloud-based software, which in turn allows it to be viewed on on-site or remote computer workstations, mobile devices, and increasingly, lift truck dashboard displays.
Opening this real-time window into battery health allows operations managers and lift truck operators to see developing problems and take action before they lead to battery failures and lost productivity. It’s a crucial step toward controlling unplanned downtime and reducing operating costs, but it’s just the start of what effective battery monitoring can do.
Optimized maintenance, charging and changing
The next step after identifying battery performance issues is correcting the maintenance practices causing the problems in the first place. Watering, charging and equalization conducted improperly or at improper intervals are common culprits. Do any of these tasks poorly or too infrequently, and you damage the battery and decrease its runtime and life. Do them too often, and you’re wasting labor. Both scenarios can increase operating costs and reduce lift truck uptime and productivity.
Modern battery management can help operations avoid all of it, both by setting the proper intervals for watering, charging and equalization, and by monitoring if, when and how operators deviate from these practices. Such approaches can help operations managers promote best battery maintenance and charging practices and identify when, where and how to better train their employees. (Always be sure to follow the manufacturer’s guidelines for battery care and handling and direct any questions to your battery professional).
Battery monitoring solutions can also give operators even less to think about by automating battery charging and selection entirely. By monitoring chargers and tracking when batteries are connected, how long they charge and how long they cool, such practices can prioritize battery selection and tell operators, which battery to choose. Automating the process can help facilities stop over- and under-utilizing certain batteries, thereby extending their runtimes and lifecycles while ending the costly practice of changing batteries too often.
Fleet right-sizing and future-proofing
Beyond tracking performance and optimizing maintenance, advanced battery monitoring can also help companies assess their battery asset spend and answer questions such as, “Do I need more batteries, or fewer? Am I spending too much money on my lift truck power, or too little?” By quantifying battery room power usage and weighing it against actual hourly lift truck power requirements, a battery management system can help a facility right-size its battery and charger fleet to help cut capital and maintenance costs.
Along with qualifying and quantifying battery and charger budgets based on these shorter-term needs, battery monitoring can also help a facility assess longer-term power needs and evaluate potential technology upgrades to meet them. “Does it make sense for us to start fast-charging? Which would save us more money – replacing our flooded lead acid battery fleet with Thin Plate Pure Lead (TPPL) or lithium-ion (Li-ion) technology? Which would deliver a faster return on investment?” Effective battery monitoring and maintenance can help answer all of these questions and more.
Battery knowledge is power
Whatever the size and scope of your warehouse operation, today’s battery management, monitoring and solutions can lay the groundwork for greater lift truck and battery fleet efficiency. And, depending on how basic or how sophisticated you want your solution to be, there are options out there to suit every situation. To find one that works for you, look to your battery distributor for help getting started – the battery knowledge you’ll gain will provide you with the power to boost uptime productivity, which may lead to increased profitability.