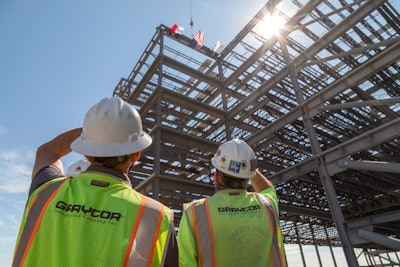
Social distancing added an enormous logistical challenge to picking and packing inside of warehouses, at least when planning the movements of human workers. Adding further to the challenge was the fact that online orders skyrocketed, and consumers may not be returning to stores any time soon. Survey results released by First Insight in January 2021 found that “60% of respondents stated that spikes in COVID-19 are deterring them from shopping in-store.”
Even before the pandemic, automation and robotics were being widely deployed in distribution centers to increase productivity. Combined, pandemic-related shopping behaviors and economic incentives for investing in robotics are likely to mean an ongoing high adoption rate of automation. This will, in turn, cause changes in how warehouses and cold storage facilities are designed, constructed and operated.
Because of the level of detail involved in the installation of an automated storage and retrieval system (AS/RS), not to mention the complexity of AS/RS functions during the facility’s operational stage, accommodation for these systems must be made upstream, even during planning, site selection and capital appropriations processes. Companies that are forward-thinking with a thorough pre-construction process and the ability to act quickly are the most likely to be successful in the switch to automated distribution. The key is to assemble a team of owners, designers, engineers and contractors during the earliest project planning phases, as well as to use a project delivery method (such as design-build) that supports this teamwork.
Facility layout
An AS/RS enables picking and packing single items (as opposed to traditional bulk cases). The biggest difference between an automated warehouse and a traditional one is the need for height. Most AS/RS are vertically arranged and have many interaction points, so exact ceiling heights and system layouts dictate facility design. Automated systems also have higher electrical power requirements than traditional warehouses. Support spaces for the computerized control systems—including a server room—may also be necessary.
Rack-supported buildings
The use of AS/RS is not just causing alterations to traditional structural designs; it’s also causing the entire warehouse building type to be re-thought. For example, rack-supported structures are not buildings in the traditional sense, because they are not for human occupation. The independent storage rack system of the AS/RS forms the structural system of these facilities; walls and roofs are put in place after rack construction.
Rack-supported buildings offer time savings during construction because material lead times are often shorter and construction tasks occur faster. With no internal columns creating “wasted space,” rack-supported facilities have lower costs per square foot. They also save time during the facility’s operations phase because automated equipment moves product very efficiency. In addition to these benefits, rack-supported structures are stronger than conventional steel frames.
It is important to note that various federal, state, and local regulations govern these specialized structures. Like any building, rack-supported facilities must withstand seismic or weather-related forces (although, with their multiple structural members, rack-supported centers have an advantage over traditional warehouses in resisting such forces).
Rack-supported systems—and any other entirely automated facility where human occupation is unnecessary—are eligible for unique low-oxygen fire safety solutions. This is a significant benefit, because with their low level of humidity, cold storage facilities are especially vulnerable to fire. Low-oxygen fire suppression systems, sometimes called hypoxic systems, can actually prevent the occurrence of fire in unoccupied buildings by reducing the conditions necessary for combustion. The systems typically are cheaper than traditional ones, as well.
There are specialized requirements for refrigeration systems in rack-supported distribution centers. Because the finished facility is not navigable by people and equipment, refrigeration components must be installed as the building is erected. Refrigeration systems should also be engineered to ensure against temperature stratification, in which the higher levels of the facility are a different temperature than the lower ones (caused by outdoor air temperatures and distance from the installed cooling source).
Designing the automated system
In any automated facility, AS/RS system requirements will dictate design decisions from the project’s outset. Components of an AS/RS include machinery, racks, conveyors and/or tracks, and controls. Questions to ask when selecting and arranging the system include:
- What is the load type (e.g., pallets, trays, totes, cases, cartons)? Load type and weight per unit are major determinants of the appropriate type of AS/RS, although storage density and the desired speed of access are also important factors.
- Does a given distributor deal with multiple picking units? If so, it makes sense to automate storage and retrieval of the packaging where it will maximize labor savings. Rack-supported structures may prove ideal for food manufacturers that specialize in a single product with uniform packaging dimensions.
- What volume of product will be moved and how many different SKU numbers will the facility hold? Historical data can be useful in determining when the greatest product demand will occur. AS/RS should be designed and sized to handle peak volumes in a way that is balanced against everyday demands.
- Which products move fastest and which move slowest? This information will inform the slotting plan, i.e., the arrangement of inventory that maximizes efficiency in picking.
Once answers to the above questions have been obtained, teams must choose between the basic AS/RS types on the market. For large loads, unit load systems are a good choice because they can handle full pallets and cases. Typically, these systems are configured in vertically oriented, narrow-aisle racks and served by special electrified cranes that are outfitted with guide rails, control systems, elevators, lifting devices and handling devices. Aisles can be either fixed, in which a crane services a single aisle or moveable, in which a crane can service multiple aisles. Deep lane storage systems do not have aisles, so they are very space efficient. However, they are the least flexible layout and therefore require some of the most intensive up-front planning. High-density systems use three-axis autonomous mobile robots (AMR) capable of navigating along a floor through the high-density rack system, then travelling vertically up a storage rack to retrieve a tote or case.
For smaller units, mini-load systems are an option. They handle totes, cartons or other small units and are best for facilities that handle multiple SKUs. Carousel-based systems, which move bins continuously along a track and can be either horizontal or vertical, are another option. A vertical lift module is an enclosed system that has an inserter/extractor in the center and a column of trays on either side. Finally, there are some systems that use automated guided vehicles to pick and shuttle units.
Given the constraints of AS/RS system components, warehouse “furnishings” are far from an afterthought. During capital planning for an automated facility, system selection and the attendant design decisions must be made during the project’s planning phase. Pre-construction activities should therefore involve addressing a complete checklist of the various considerations. To ensure a knowledgeable approach, engineering and construction experts should be brought in early. Doing so reduces risk and leads to better project outcomes.