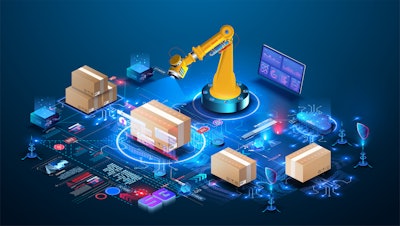
For many companies, warehouse automation is not new.
But for some companies, warehouse automation still remains a foreign way of doing business; one that supersedes the way “they’ve been operating for years.”
It involves wearables, drones, robotics and emerging technologies that are costly to implement, difficult to learn and somewhat cumbersome to existing staff.
And more often than not, automation is only being implemented into certain parts of the supply chain vs. end-to-end.
In Food Logistics’ March/April 2023 issue, editor-in-chief Marina Mayer talks with several industry experts about how warehouse automation keeps cold food chains moving.
Here’s an interview with Kyle Nevenhoven, principal consultant, food and beverage for Dematic, who details the importance of addressing the adoption of automation from a behavioral and cultural standpoint. [CLICK HERE to read the article in full].
Food Logistics: More and more companies in the cold food chain are adopting warehouse automation solutions. Why?
Kyle Nevenhoven: There are a few main reasons why cold food chain companies are adopting warehouse automation. One of the major drivers is labor. As difficult as it is to find labor in general warehousing, it becomes even more challenging in the difficult environment of coolers and freezers. Another driver is the utilization of space and the cost to condition space. Having a very dense storage mechanism, and taller buildings with better cube utilization, can help to reduce the cost of construction as well as the ongoing costs to condition the space. Increased density also reduces carbon footprint per pallet stored. Lastly, food safety regulations can be tracked and maintained in a more controlled fashion when the movement of goods is automated.
Food Logistics: On the flip side, there are several companies just getting started in the automated warehousing game. What advice do you have for those organizations just starting to adapt these solutions? What are the next steps?
Nevenhoven: For many companies, the automation journey can be one of significant change in both operational behaviors and culture. It is important to address both throughout the process of the adoption of automation. From an operational perspective, it is important to do a thorough business analysis to determine where automation may fit into the organization. Sometimes this can be very clear by way of visible operational inefficiencies, staffing challenges, or throughput barriers. At other times, the areas in which to focus automation can be difficult to identify, and in these instances, bringing in a consultant or automation firm to work through the various types of automation, and through the various functional areas of the operation, can help to drive the focus of automation strategies.
From a cultural standpoint, the journey to automation requires careful change management, ensuring that employees, managers, and executives alike understand why automation is being implemented and how it can be a benefit to both the employees and the company.
Lastly, the move to automation frequently requires additional building footprint. While not always conventional wisdom, the most productive path forward is to understand the operational and business requirements, design the automation and then fit the building to the resultant system design.
Food Logistics: Describe new technologies/solutions introduced to market over the past 12 months. Include press releases when/where applicable.
Nevenhoven: Over the last 12 months, many of the new technologies released to the market have been in the autonomous mobile robot (AMR) and robotics realm. These solutions have advanced significantly over the past 12-plus months, becoming solution types that can be implemented rather quickly, at a favorable price point and with very little infrastructure change, mitigating major interruptions to existing operations.
Food Logistics: What are the Top 5 types of automated warehousing solutions (i.e., WES, order fulfillment), and why?
Kyle Nevenhoven:
a. WMS/WES – Software is ultimately the heart of any automation system. Intelligent software, and the successful implementation of software, enables the success of an automation project. Additionally, software provides visibility throughout the supply chain, allowing operators to make proactive decisions, in turn making the best use of both the automated and non-automated resources available.
b. Order fulfillment – Order fulfillment can look very different from one organization to the next. In almost all organizations, it is the biggest single source of labor requirements, and is therefore often one of the main focuses of automation. A solid order fulfillment solution can both reduce labor requirements, as well as improve the environment and experience for the employees. Additionally, it is order fulfilment that generally facilitates the customer experience, and therefore can be one of the main drivers in becoming the producer or distributor of choice.
c. Pallet storage – In cold food chain, pallet storage automation is a significant automation opportunity. When constructing a new facility, automating pallet storage may allow a facility to be built with a much smaller footprint, leading to cost avoidance in land acquisition and the building itself. This cost avoidance coupled with OPEX labor and energy savings can in turn contribute significantly to the ROI of the automation project. For existing buildings, pallet automation may be able to prevent the need for expansion or relocation and can also act as a source of labor reduction.
d. Material movements – In most operations, there are significant material movements that must occur across the facility. The use of automated guided vehicles (AGVs) or autonomous mobile robots (AMRs) can automate these repetitive tasks with little infrastructure change to the facility.
e. Robotics – Robotics are a critical component of many automation systems, as they can automate both repetitive tasks, tasks which could generate injuries through heavy lifting and repetitive motions, and tasks that could otherwise be dangerous or undesirable.
Food Logistics: How does warehouse automation helps those B2B companies looking to branch out to B2C/e-commerce?
Nevenhoven: Many B2B companies currently have limited B2C capabilities, as they have built their existing operations around the order cycles and order profiles common to B2B activities. When investing in automation, a well-designed system ultimately provides quicker and more efficient access to inventory which ultimately can allow for the shorter SLAs that B2C and e-commerce customers seek. Additionally, where many cold food chain companies have traditionally picked at the pallet, layer and case level, automation allows for the introduction of efficient each picking, providing additional value to consumers. A cold chain provider that provides B2C e-commerce services can also serve as an enticement to some producers to bring not only the B2C but also the more traditional B2B business vs. a competitor that does not offer the B2C capability.
Food Logistics: How will disruptions such as inflation and labor shortage, for example, impact the future of warehouse automation?
Nevenhoven: Inflation and labor shortage both have implications on the future of warehouse automation. While inflation can tend to negatively impact the ROI, the magnitude of the challenging, more expensive labor market has increased the interest in and need for automation substantially. Even more importantly, the prevalence of labor scarcity, which presents a business risk in not being able to accommodate the throughput needs of the business, or ultimately prevents the ability of a business to grow, has become a major driver toward automation. Labor challenges, along with inflation, have caused organizations to rethink their return-on-investment expectations. Whereas it was previously common to expect a 3- to 5-year ROI on a major automation investment, it is not uncommon in today’s climate to accept a 7- to 10-year ROI, given the risk to the business of doing nothing, or doing too little to have a long-term impact on business risk mitigation.
Food Logistics: What are some things not addressed above that may be pertinent to our readers?
Nevenhoven: The thoughtful and successful implementation of automation, applied to the right functions within a business, can provide not only a reduction in bottom line costs, but a true top line revenue growth through reduced SLAs, quality improvements, value-added services and an all-around superior customer experience.
[CLICK HERE to read the article in full].