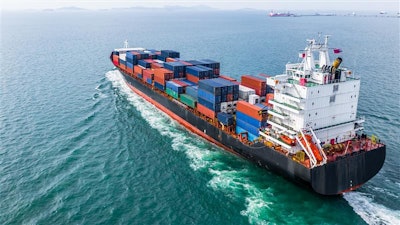
Global supply chains are headline news. Shortages and disruptions over the past few years have caused companies in all industries to reconsider where they are sourcing and processing products and the potential for reshoring their supply chains.
The pandemic exposed risks in supply chains not visible in the past and led to supply chain disruptions, labor shortages, a shortage of ingredients, plus the inflation of prices.
Before the pandemic, global food supply chains suffered from the tariffs on aluminum and steel used for canning food products and on imports from China. Now the war on Ukraine has caused global shortages of agricultural products.
All of these symptoms point to a lack of supply chain strategic planning. For so many years, we were lulled into believing all was well because global supply chains were running smoothly. U.S. companies sourced, produced and shipped products globally. Supply chain risk and mitigation were just an afterthought and bringing production back to the United States was cost-prohibitive. Supply chain professionals focused on execution -- moving products to their destination in the most cost-effective and efficient way. Only a handful of companies considered the possibility of reshoring operations.
Fundamental lack of supply chain planning
This lack of strategic planning and consideration of global risk was and still is evident across industries. Electronics are still mostly made and shipped from China. Automotive parts are produced in China, Mexico, and Brazil. Pharmaceuticals and related chemicals are produced in China and India. Apparel and footwear are produced in China, Vietnam, Turkey, and Bangladesh. Food is grown and packaged around the world. Globalization has flourished over the last 25 years.
Now is the time to rethink and reconstruct global supply chain strategies.
Sustainability
Concern over global warming has also caused a rethinking of strategies based on droughts, floods, snowfall and wildfires. Companies now consider alternate regions for farming, processing food and other products, and are working to produce biodegradable packaging, reduce chemicals in processing and recycle waste products.
Logistics and transportation are now additional concerns based on fluctuations in pricing, container availability and port congestion during the pandemic. Producing products closer to markets where those products are being sold reduces the carbon footprint. The Reshoring Institute calls this “Local for Local,” producing in the market you are serving.
Consideration for growing, processing and packaging in local markets is now the strategic direction of supply chain leaders. Products that are the growth or production of America may be labeled “Made in the USA” or “Product of USA,” and these labels have intrinsic value. A study conducted by the Reshoring Institute showed that Americans are willing to pay up to 20% more for products made in the United States. The study concludes that there is more perceived value to products made or grown domestically and therefore these products can command a higher price.
Sustainability and reduction of a company’s carbon footprint are likely to be on every company’s strategic agenda for the foreseeable future.
All parts included
It’s not just the shortages of raw materials or ingredients that have wreaked havoc on supply chains, it is also the shortages of packaging materials. Take canned food for example. Shortages of aluminum for canned fruit have resulted in empty shelves and a limited selection of some brands.
Shortages of available and inexpensive aluminum are caused by the 232 import penalty tariffs placed on aluminum and steel, and the 301 penalty tariffs on almost everything coming from China. These tariffs make aluminum imports considerably more expensive – up to 15% more for most imports, plus an additional 25% for imports from China. The intent of these tariffs was to make U.S.-made aluminum and steel products more cost-competitive, but with limited aluminum and steel production capability in the United States, the result is rising prices and shortages.
Geopolitics and war
The geopolitics of Asia and the war on Ukraine have also made matters worse.
The escalation of the trade war with China introduced additional tensions between the two nations and a vulnerability across Asia. With China threatening to invade Taiwan (when, not if) the U.S.- China relationship is on shaky ground. Companies in America and Western Europe are actively seeking sources outside of China.
The war on Ukraine has also taken a toll on food production. Ukraine is one of the world's major grain producers. The country mainly grows and exports wheat, corn and barley. According to the European Commission, Ukraine accounts for 10% of the world's wheat market, 15% of the corn market, 13% of the barley market and 50% of the world's sunflower oil market. The loss of food production in Ukraine has contributed to global shortages and has driven up the prices.
Production close to home
The pandemic exposed the many reasons for producing products close to the markets in which they are being sold.
Most companies experienced shortages - off-and-on-again factory production, particularly for products coming from China during the various COVID-19 shutdowns and lockdowns. Inconsistent and unreliable suppliers caused shortages and chaos in many industries.
Mitigating the risk of long global supply chains and addressing the need for more sustainable products means that producing closer to home should be considered a viable alternative. But it’s not that easy to change global production and processing. It takes long-term strategic planning to answer the question, “where in the world should we manufacture and process goods”?
With more than 84% of U.S. companies indicating that they are now reshoring or considering it, we will soon begin to see the regrowth of industry in America.