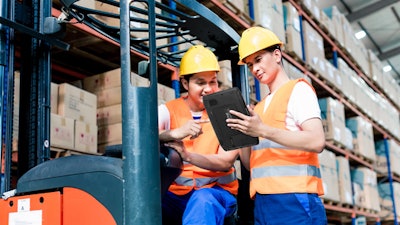
Whenever you walk into a distribution center nowadays, there's a high probability that the team is behind schedule, product is being cut from customer orders and there's not enough labor on the floor to make ends meet. Unfortunately, it's likely to get worse. According to research by ARC Advisory Group, the number of applicants applying for warehouse jobs is shrinking year over year, with over 490,000 open jobs available as of July. Those factors paired with internal pressures to reduce costs and drive efficiency has created an untenable current ecosystem in dire need of innovation. According to a Blue Yonder report, 53% of manufacturers and 58% of logistics services providers saw “pressure to reduce supply chain costs” as a major investment driver in supply chain technologies.
As you begin to re-evaluate your distribution center strategy in the hopes of keeping up with demand, it’s only logical that you investigate moving toward a “lights out warehouse" or an environment so automated that people are not necessary to operate the facility. Unfortunately, jumping straight to a dark warehouse isn't feasible from a CapEx or OpEx perspective for most businesses. It’s also challenging because the end-to-end technology required to support dark warehouses doesn’t exist yet.
Eventually, most organizations decide it is in their best interest to retrofit a legacy warehouse. There are many easy-to-exploit opportunities worth investigating around automating processes and introducing new software to drive efficiency. Unfortunately, when you decide to go down the path of retrofitting an existing warehouse, you can't just throw automation at it.
Click here to hear more about automation in the warehouse:
The balancing act between automation hardware and software
You’ve decided to invest in new technology to make life easier in the warehouse and need to explore what hardware and software exist to help. First, let’s review automation hardware because automation technology has the highest return when viewed as a way to supplement human labor. Unlike a human labor force, automated systems are stellar from a productivity predictability perspective. In contrast, you may never know which labor associates will show up on a given day. Some examples of automated systems worth reviewing are:
- Automated storage and retrieval systems (AS/RS)
- Layer pick systems
- Automated guided vehicles (AGVs) and forklifts
- Goods-to-picker systems
- Robotic arms
- Conveyance systems
Each of these systems can significantly supplement what are traditionally manual processes done today. Unfortunately, these automated systems are also very costly. For example, larger automated systems like adding an AS/RS to a complex distribution center can cost over $3 million. This investment significantly reduces the manual labor and equipment required for inventory putaway and retrieval, but takes a long time to pay back. It also still needs to integrate with all of the other workflows inside of the distribution center. Those workflows could involve case pick, layer pick, replenishment, kitting, repack, each pick, loading, receiving, cross-docking and more.
When looking at areas for warehouse improvement, all of the workflows mentioned above need to be considered to understand not just where innovation can net the highest return, but also where it has the highest return on investment (after all, reducing costs is a big part of running a supply chain). Because return on investment (ROI) is so important to supply chain organizations, it's more common for retrofitting to happen in an area that requires much less capital expenditure – software.
Most distribution centers already have a warehouse management system (WMS) in place but struggle to see the value in upgrading. Of course, they may be promised the sun and the moon from WMS vendors on what capabilities will be exposed via an upgrade. Still, history has shown that those capabilities rarely manifest themselves precisely as hoped. Instead of just upgrading a WMS to spur innovation, most groups are now starting to explore innovative new software like slotting optimization tools or WMS accelerators.
Wait… what is a WMS accelerator?
Let’s revisit why we’re exploring software innovation:
● There are more demands on the business than ever.
● Reducing costs is still mission-critical to the greater organization.
● Labor is very challenging to find and retain.
● Automation technology is expensive.
So, how can you innovate while simultaneously addressing all of these problems? Explore the use of a WMS accelerator, which uses advanced analytics to optimize all of the activities in and around a distribution center to increase capacity per headcount, reduce inventory touches and maximize customer satisfaction.
For example, say it is 11 a.m., and a site is trying to plan for the next shift. There is much information that needs to be balanced:
- An inbound expected at 10 a.m. still has not checked in at the gate.
- Production will be producing approximately 500 cases of Item ABCD at 2 p.m.
- There are 22 scheduled outbounds at 3 p.m. (18 drops, four live).
- Six are short inventory currently --two need inventory from the 10 a.m. truck that has not arrived.
- Two shipments could be fulfilled directly from the production line.
- One shipment has yet to be assigned a trailer, but there is a drop trailer available.
- Three shipments require a case pick that has not yet started.
- There are 13 scheduled inbounds at 12:30 p.m.
- Seven of them have inventory that could be used for the outbound at 3 p.m.
- There are only eight forklift drivers, six reach truck drivers and 2 yard jockeys on shift.
- There are only 12 dock doors available and nine staging areas.
A WMS accelerator can understand all of these operational constraints and play forward warehouse operations to identify the bottlenecks. Beyond that, it can tie all of the different tasks required to execute this work together and create optimal schedules for everybody involved in the whole operation.
A WMS accelerator would integrate with the WMS to rearrange the picking schedule and change dock times (while still meeting the carrier pickup time based on if a load is live vs. drop) to ensure all shipments are made without any controllable inventory cuts. This “playbook” can integrate all of the way down to dynamically controlling the work queue, increasing labor capacity by over 10% simply by reducing unnecessary escalations and optimizing task times. This also minimizes detention and demurrage times, increases fill rates and saves site planners many headaches. It does all of that without the need for a WMS upgrade or exploration of massive capital-intensive expenditures.
Best of all, when capital expenditures are finally made, a WMS accelerator’s planning capabilities can treat each automated system as a different “actor” in the warehouse and ensure it is always tasked with the right work to orchestrate a complete and successful operation.
In short, if you are exploring different innovative solutions for retrofitting a distribution center, explore WMS accelerators in tandem with more traditional capital-intensive programs.