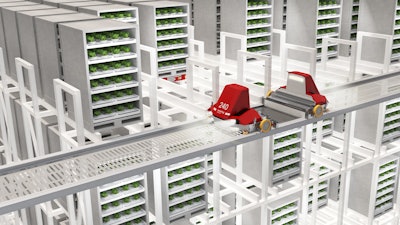
Vertical farming, the practice of growing crops like leafy greens in vertically stacked trays or shelving within warehouses and other buildings, is not a new concept.
But, while today’s applications look much different since its first inception, the initial idea of growing crops in indoor facilities to bring healthy, fresh food closer to densely populated urban environments remains unchanged.
The vertical farming industry is currently estimated to be a $3 billion industry. However, most operations are not profitable or scalable beyond the niche applications they currently occupy. There are a number of challenges and obstacles that need to be overcome, including high upfront, operational and labor costs, as well as the inability to easily scale to meet demand.
In many ways, warehouse automation can help vertical farming grow beyond its current applications.
Conquering the last mile of food production
While there are challenges still to be overcome with the science behind the planting, most vertical farming companies continue to refine and enhance their proprietary growing methods. Again, where most companies struggle is with profitability and scalability. One of the seemingly most effective ways to solve these twin challenges is by taking a logistics-market approach to vertical farming.
Think of it in terms of a distribution issue. Numerous companies are diligently working to conquer the last mile of their supply chain to bring products closer to consumers. This is exactly the goal of vertical farming -- bringing food production closer to consumers where there is a need. And, as the Coronavirus disease (COVID-19) pandemic has shown us, the food supply chain is more fragile than many may have realized. A robust vertical farming program would strengthen that supply chain and provide another tool in the fight against supply chain disruptions and shortages.
In the traditional supply chain, automation is playing a significant role in providing the flexibility and scalability needed to keep products moving. This includes in micro-fulfillment centers that are bringing fulfillment closer to consumers.
Strategically integrating warehouse automation technology into vertical farming operations will help them overcome barriers to growth by reducing costs and increasing scalability. It will broaden the applicability of growing crops, allowing these operations to be installed and maintained in a wide range of pre-existing and purpose-built space in urban areas.
Borrowing from high-density pallet warehousing
A variety of automation technologies and configurations can be used in vertical farming based on a number of factors, including the growing process, crop type and space availability of the operation. The important thing is that the vertical farming company work closely with the automation provider to determine the best automation strategy. For instance, one approach could use an automated shuttle system traditionally used for high-density pallet warehousing.
In this type of customized vertical farming installation, automated shuttles would move around discrete plant shelving units inside an enclosed room or facility. Each shelving unit could hold multiple plant trays, depending on plant growth height needs. Shelving units would move around the enclosed space based on the needs of the plants for water, nutrients, light, planting, germination, maintenance, harvesting and monitoring. Regular day/night cycles could be accomplished by moving the shelves between dark and light spaces, instead of switching lights on and off.
The modular design of this type of system enables it to be implemented into any shape or size building. It is adaptable to almost any space both horizontally and vertically across one or multiple floors. This includes in existing abandoned warehouses in urban centers, unused floor space in office buildings or new purpose-built facilities.
One or more fixed activity stations devoted to planting, maintenance, inspection and harvesting can be added to the configuration. These activity stations could be located behind roll-up doors to maintain the clean room environment and reduce contamination potential. Behind the roll-up doors the tasks of planting, inspecting and harvesting the plants could be conducted by robots, humans or a combination of both.
As plants grow, their needs for space, lighting, temperature and nutrients change. An automated solution with discrete mobile plant shelves that can automatically move between various zones enables the changes plants need over their lifetime. The system could also start with very dense planting for germination and then thin the plantings over time by moving densely planted shelves to an activity station, taking the plants out and then moving them to new trays and shelf units in a thinner planting density. This allows for the optimal usage of planting space for light and nutrient delivery over time.
Depending on the modularity and flexibility of the automation technology being used, there are a number of different configurations that can be customized to meet the needs of individual operations.
Supply chain automation technology can provide vertical farming operations a scalable, adaptable, cost-effective solution for low-footprint vertically stacked installations that can enhance planting, monitoring, maintenance and harvesting – as well as the complex scheduling and logistics of such an operation.
Taking such a logistics-market approach to vertical farming can eliminate barriers to growth, help strengthen the food supply chain, transform abandoned urban buildings into productive growing facilities and contribute to reductions in pollution. It can also help lower the cost and environmental impact of growing organic, fresh produce to help eliminate food deserts in underserviced communities.