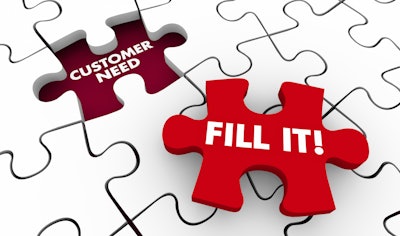
Warehouse managers often think that throwing equipment into the warehouse to automate a process will take care of all their problems of late fulfillment times, out-of-stocks and labor shortages. But, operations are getting more complex, and labor is becoming more and more of a challenge to find. Throw the continuing pandemic into the mix, and you have a recipe for disaster.
Consumers are ordering more and more products online in response to the pandemic, and studies show this will not let up. So, companies receive customer orders and have transportation lined up to deliver on them. Still, they struggle to execute all the activities required to get the appropriate inventory into the correct trailers. This is causing transportation delays, which trickle downstream to affect nearly every part of the overall supply chain.
Supply chains are really messy right now.
A man, a dog and a long way to go
If you were to speak with any director or VP of logistics at a large shipper, they would wax poetically about their vision for dark warehousing down the road. In the future, automated machines run all warehouse operations, and the only bodies in that warehouse are a man and a dog. The dog exists to make sure the man doesn't touch anything and the man exists to feed the dog. In 50 years, it might be possible.
The truth is that most automated systems exist in a process silo, ignoring many of the surrounding warehouse micro-flows. For example, a consumer goods shipper may use automated forklifts to retrieve a pallet, but the pallet might sit in the staging area for 12 hours before it's loaded onto a trailer. Valuable staging space is wasted, and other orders may not get out on time, in full. The actions of the automated forklift need to be intelligently orchestrated to ensure it is performing the most positive action at the right time.
What warehouse managers need to know
To meet fulfillment times and customer service levels, warehouse managers need to know:
- When will I run out of inventory?
- When will I run out of dock space?
- How can I match capacity to demand?
- Will I make my on-time, in-full fulfillment numbers?
- How do I synchronously plan tasks inside capacity limits?
- How can I reduce the number of touches?
For example, you know you have 150 inbound receipts and outbound deliveries scheduled for the next 24 hours. You are aware of when the trucks are supposed to arrive and where the inventory is inside of the building. To meet this schedule, you need to load each truck by a specific time, but to load the truck, you need to have everything picked by a particular time, and you need to make sure the inventory is available and the correct number of people are scheduled for picking and loading. These are all constrained sequences that need to be respected
Instead of throwing money at conveyors, automated storage/retrieval systems (AS/RS) and other systems, shippers must understand the steps necessary to optimize processes best. It takes a holistic look at the supply chain to orchestrate all this work. To do this effectively, companies are turning to warehouse management system (WMS) accelerators. These tools look across all of the siloed operations at a distribution center (DC) or campus of DCs to optimize labor, inventory levels, touches and equipment to drive efficiencies.
WMS accelerators operate one level above robotic systems today, leveraging data from warehouse management, yard management, order management, visibility and production systems to provide a single, unified view of operations. They then take all of that data gathered and use it to "predict" what will happen via digital twin technology. This technology brings in the current state from all systems and all known shipment and order information and plays the future-forward based on known constraints like labor, inventory and human or robotic task times.
From there, WMS accelerators create a prescriptive plan to ensure that demand is met while respecting all constraints inside of the building like labor availability, inventory availability, task sequences and more. This process enables a site to direct work effectively across human and robotic systems, leveraging each while simultaneously considering all micro-flows that need to be completed to deliver customer orders effectively.
As you begin to create a strategy around automation and labor augmentation, learn from the best shippers globally by thinking of total site activity optimization and reviewing the need for a WMS accelerator moving forward.