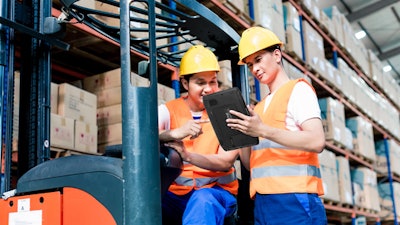
If you look around at everything you own, nearly all of it was put together and shipped thanks to a warehouse worker. They make this possible by lifting and carrying boxes and using heavy equipment, like forklifts and pallet jacks, to move product to and from delivery trucks. In good times, however, when everything is operating business as usual, it can be easy to forget just how vital the job of a warehouse worker is. The pandemic offered a glaring reminder of just how critical warehouse employees are to businesses and consumers alike. When the world shut down, warehouses kept moving full steam ahead to get essential items on shelves.
Making sure essential workers are safe on the job is paramount—not only for the employees themselves, but also for your business and the customers you’re serving.
Let’s dig into some of the ways to effectively prioritize safety in the warehouse.
Safety equipment and gear
The equipment you employ within the four walls, along with wearable safety gear, should be one of the first things you look at when designing a safe warehouse.
· Powered industrial vehicles (PIV) management system. Having a PIV management system in place ensures operator accountability, while providing valuable information to reduce costs and improve operator productivity. PIVs can be equipped with collision alert devices to help identify performance trends and enhance compliance with applicable regulations.
· Waterless forklift batteries. Waterless batteries normally require watering 4-6 times per year, compared to standard forklift batteries that require weekly and bi-weekly watering. Less frequent watering prevents acid leaks and sulfate buildup, which greatly reduce a battery’s useful life. By choosing waterless batteries to power your PIV, you’re reducing the frequency of exposure to employees and the costs of preventative maintenance.
· PIV warning lights/alert systems. As part of the routine, pre-use inspection is important to ensure all warning lights and alert systems on PIV are working properly. These safety features ensure pedestrian safety and operator safety when backing out of trailers, down aisles and around blind spots.
· Flexible warehouse automation. The power of automation is real, but you don’t have to maintain an “all or nothing” mindset to drive incremental improvements. Leveraging the following pieces of automated equipment is a great place to start:
o Conveying systems
o Electronic pallet shrink wrap machines
o Automated storage and retrieval systems (ASRS) that automatically place and retrieve pallets in facility locations with accuracy and speed
o Automated guided forklifts, a.k.a. autonomous transport that execute vertical handling and placement of goods, increasing productivity and standardizing workflows across expansive distribution centers
· Personal protective equipment (PPE). PPE is worn to minimize exposure to a variety of hazards in a warehouse. Some examples of PPE are safety footwear, hand protection, eye protection and fall protection, to name a few.
A safety footwear program provides not only foot protection during material handling, but also reduces the likelihood of slips, trips and falls. A vending machine program makes all types of PPE readily available to employees at all times to ensure they have the proper tools and equipment to perform their job safely.
Ergonomics
Ergonomics is important for every job type, but takes on a heightened level of necessity in the warehouse. Re-designing workstations to account for average worker height ensures that each employee’s job can be completed with greater ease, and ultimately, prevent injuries. Using equipment such as spring pallets and skid lifters prevents workers from having to lean down or bend at the knees. Instituting injury prevention programs offers a combination of theory and practical teaching methods designed to ensure employees learn how to use their bodies safely, both at home and on the job.
Piloting certain programs can be a great way to test the waters and gather valuable data in the process. For example, if reducing sprain and strain injury rates is a goal, you can test out the use of reflex devices, which identify high-risk postures in workers and create long-term behavior change by providing real-time ergonomic feedback. You can also pilot an analytics platform that equips leadership with unique daily insights to help drive safer working environments and limit operational disruptions.
Employee engagement
Training, ongoing coaching and listening to employees is a trifecta that forms a recipe for success when it comes to preventing workplace injuries. Fostering a safety culture in which every employee feels free to raise safety concerns without fear of retribution is key and requires a top-down approach.
There are several ways to accomplish this:
· Create daily opportunities or “safety moments” prior to meetings to discuss safety topics as a team, taking on a lessons-learned approach. This time can also be designated for pre-shift stretching.
· Share weekly safety messages with staff. This facilitates open and honest health and safety discussions and provides the chance to regularly share industry best practices.
· Develop incident sharing communications by collecting personal stories of employee injuries, everything from how their injury affected them, to how they might have been able to prevent it. These stories can be shared on posters hung in the warehouse, posted on the company intranet and/or shared via email.
· Provide a centralized place for compliance safety training tailored for specific roles.
· Empower employees to stop work if they identify an unsafe condition in their work area.
It’s important to be mindful that while some employees may feel comfortable raising safety concerns to the group, some might prefer to do so anonymously. You can place drop boxes in the warehouse, where employees can place feedback cards, which can then be reviewed during safety committee meetings. These are just some examples to demonstrate to employees that you care, and their safety on the job a priority. Ultimately, from senior leadership to front line workers, workplace safety is everyone’s responsibility.
What’s the safety mantra
If you’re striving to achieve a zero-injury workplace, foster a collaborative working environment, including management leadership, employee engagement and effective training. Be relentless in identifying and implementing effective methods to eliminate or control hazards, and remember, choosing to ignore a safety hazard could compromise someone’s life.