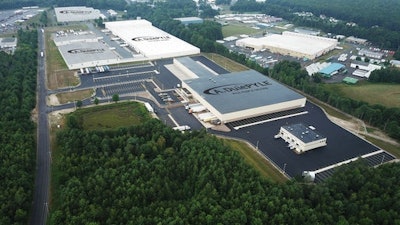
A logistics company’s most valuable assets are the people on the ground who make the shipping process run flawlessly. To improve its people’s well-being and protect the overall efficiency of transportation and distribution networks, warehouse and workplace safety should always be a top priority.
Logistics companies in the food and beverage space can apply simple strategies to protect their warehouses, increase safety measures for employees and keep food and beverage items properly stowed. It is always a sound investment to spend on safety on the front end to insulate warehouses from risks associated with worker’s compensation, customer claims, product contamination and much more.
Know how to store food and beverage products
Keeping all food and beverage products well organized is the first step to ensuring a secure warehouse, as having a lean environment for all items will minimize clutter and help to certify that everything has a place where it belongs. Not only will maintaining a tidy warehouse keep all items organized, but it will also help illuminate any hazards that develop during the workday. When everything is well organized, it is easier to pinpoint areas of concern throughout or following a shift, as items out of place will likely stick out like a sore thumb. Providing safe walk or travel lanes can also assist in promoting safety with more efficient travel layouts.
To perfect organization skills, it is critical to know the details of all food and beverage products and how to store them properly. Storing products can present several challenges. Making sure everything is labelled correctly and using signage to note areas of concern are important steps to take when storing products. An essential part of storing food and beverage is taking into account temperature and climate control. Warehouses with temperature-controlled space use cooling and heating units to keep temperatures within a set range which helps to preserve the product. When storing food and beverage products, warehouse workers must understand how to properly store products to prevent dangers such as spoiling and cross-contamination.
Good Distribution Practices (GDP) are being adopted across a growing number of industries in addition to FDA regulations and requirements. For example, the Global Food Safety Initiative (GFSI) is an industry-driven standard specific to food handling and adds a layer of accountability to third parties distributing food products. No matter how many specific classifications your products require, it is always critical to have sustainable process documentation.
Protect your house
Regardless of the size of the building or the operations within, there are many moving parts in any warehouse or distribution environment. In a perfect world, the building, racking and other contents would never come in contact with equipment in motion. However, that isn’t always the case.
Electric forklifts are one of the most popular pieces of equipment in food and beverage material handling, with other useful equipment including reach trucks and pallet jacks. Unfortunately, while switching to electric forklifts can help boost environmental sustainability, forklifts remain one of the most hazardous pieces of warehouse equipment, and 90% of forklifts are involved in some form of an accident throughout their lifetime.
Forklifts and other warehouse vehicles are essential tools but can cause serious safety hazards, as forklifts typically weigh even more than cars. With that said, logistics companies must consider their building’s structure and implement practices to protect it. Luckily, there are many inexpensive tools to do this.
Column protectors, including brightly colored wraps, panels and guards are an inexpensive tool that can provide some insurance in an accident. Column protectors significantly reduce the chance of damage from a collision to forklifts, vehicles or people. Reducing damage means reducing repair expenses after a crash. Additionally, column protectors are typically available in bright colors, increasing visibility to forklift operators and warning those approaching to keep a safe distance.
Bollards, which are sturdy, short posts, are pieces of equipment that can act as a visual guide, as bollards can help guide traffic and mark boundaries. In addition, bollards can be used as protection from crashes, designation areas and mark direction for heavy machinery. While there are many types of bollards, safety and security are most ideal for warehouses. Safety and security bollards direct truckers on where to load and where to stop. Additionally, most are highly reflective, making it easier to spot in headlights and mirrors.
Guardrails are one of the most cost-effective safety measures that can protect warehouses and workers. This simple solution provides visible borders to direct vehicles and foot traffic in the warehouse.
As well as investing in the right tools and equipment, it is also important to prioritize routine cleaning and maintenance of floors and fixtures in food and beverage warehouses. Make sure any debris or foreign contaminants are cleaned up as soon as possible. This ensures safety among staff and prevents damage and contamination to food and beverage products.
Train and retrain the trainer
According to a Cerasis study, 5% of warehouse workers will suffer some form of injury this year. To keep warehouse workers safe, be sure to provide the proper training resources to new hires. This is a great way to execute a safety culture and keep employees educated on warehouse safety as soon as they join the team.
One approach to truly sustaining a culture of safety is to train one or more employees who successfully demonstrate warehouse safety to lead and guide safety initiatives. Training a small group of individuals to work with local facilities on executing safety protocols will create a self-sustaining and cost-effective training plan. In the long-term, warehouses will be more organized and there will be minimal disruption to your business, saving money on repairs and potentially saving employees and your facility from serious damage.
Keep striving for new ways to keep employees safe and continue to reinvest in updated training materials. Safety should be a top initiative.
Find safety strategies tailored to your business needs
There are a handful of concepts that can help deepen your commitment to warehouse organization and safety. The hardest step is always the first step -- prioritizing warehouse safety. Once logistics companies understand the vitality of this investment, they can find numerous resources and approaches readily available to them. Still, each company will need to decide which strategies will fit best within their organization. Understanding the well-being of employees, customers and products will help logistics companies know how to implement the best safety solutions.