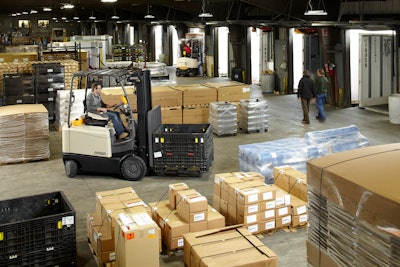
The pressure to reduce costs in the supply chain is relentless. Almost every material handling organization is evaluating the role of technology in improving warehouse productivity and efficiency, including forklift-based features that are transparent to operators.
Leveraging data from the forklift is a strategy that continues to demonstrate value in delivering measurable improvements in warehouse management. The connected forklift is a mobile information technology hub capable of collecting and processing data from products, operators, the environment and other material handling systems. And, a connected forklift provides necessary visibility so that managers can make smarter, faster, and fact-based decisions to simplify asset management, achieve greater cost control and strategically adjust to evolving needs.
The most common application of a connected forklift to date is through a fleet and operator management system that typically features two key components: maintenance and operations. The maintenance component collects and consolidates information from forklift service events to better manage costs, standardize processes and extend forklift life. The operations component involves collecting data on forklifts and operators to improve safety, utilization and productivity.
Collecting real-time data requires that forklifts be equipped with a communications terminal that integrates with the forklift’s electronics. The system wirelessly communicates data on impacts, energy consumption, utilization, location, performance and other factors. This transforms the truck from an isolated piece of equipment into a networked device and brings data-driven decision making to the warehouse floor.
Systems integration is just one part of maximizing the investment. Through our experience with forklift fleet and operator management implementations, Crown has identified four keys to realizing value from the connected forklift.
❶ Clear Goals
A forklift fleet management system’s versatility is part of its attraction. It can be used to monitor a wide range of warehouse and performance metrics, but it can also be a drawback if an organization doesn’t establish clear goals prior to implementation.
This doesn’t mean that forklift fleet management must be a single-issue solution; most users derive multiple benefits from their system. But it does mean that having a clear goal in the early stages is the best way to ensure the system gets integrated into management processes. Once progress has been made on the initial goal, new goals can be defined.
The goals an organization might consider in relation to forklift fleet management include reducing impacts, increasing equipment utilization, streamlining compliance, improving operator productivity and reducing service costs.
One of the most effective tools for ensuring continuous improvement is a scorecard that benchmarks the current state and documents initial results. Once initial goals have been achieved, the bar can be raised and goals can be expanded to create a continuous improvement process.
❷ Relevant, Timely Data
The ability to achieve your goals can be compromised without the right data at the right time.
In today’s world, the challenge is as likely to be too much data as not enough. Forklifts can provide a wealth of data to a management system, so the system must be designed to present this data to busy managers in a way that makes efficient use of their time while providing the basis for decision making. That requires information to be timely and have appropriate context. It’s also important that the system includes interactive features that can communicate and record results.
Forklift fleet management systems rely on three types of information delivery to meet these requirements:
Alerts: Alerts can be delivered to managers via email, text message or the management dashboard. They provide immediate notification of events that require attention, such as impacts or operating conditions that exceed preset thresholds. They also can be a powerful tool in managing change if they are set up properly.
Management Dashboard: The forklift fleet and operator management dashboard needs to provide managers with a quick overview or snapshot of operating trends within the warehouse. This allows managers to monitor trends and act before they reach critical levels and trigger an alert. A well-designed dashboard can enable a shift from reactive to proactive management by providing managers a visual overview of key operating trends and a clear path for quickly drilling into issues that require attention.
Detailed Reports: Based on the information presented by the management dashboard, managers need the ability to drill down to isolate problems. This is where the depth of data provided by the system becomes important. It should enable managers to quickly and accurately isolate root causes of issues, such as low utilization or low productivity related to specific operators.
❸ Consistent Management Commitment
Forklift fleet and operator management systems put the impetus for success squarely on management. It’s tempting with any technology for managers to be engaged during the early stages and then shift their focus once they believe it has been successfully implemented. That’s exactly the wrong approach; engagement with the system needs to grow—not diminish—following startup. If management doesn’t stay engaged with the system and consistently demonstrate that data from the system is being used to evaluate performance, there is little chance for sustainable change.
The data to drive change is available, but if supervisors don’t hold operators accountable, their behavior won’t change. Senior management needs to communicate their support, as well as ensure support and collaboration extends across departments to achieve defined goals.
❹ Site Preparation
Implementation problems based on inadequate site preparation can dampen enthusiasm for new technology and discourage adoption. One of the keys to site preparation is getting all stakeholders involved in the planning process, including affected departments (maintenance, operations and safety, among others) as well as IT.
Early participation by IT can identify potential issues and help ensure the proper infrastructure is in place to support forklift fleet management. IT can also guide the decision about whether the data should reside on-site or if a cloud-based implementation is preferred.
In addition, data sharing processes should be defined and documented to guarantee that the right information is shared with the right departments at the right time. These processes may ultimately evolve once the system is in place, but establishing them in the beginning increases the likelihood that all departments that can benefit from the technology will use it.
Forklift connectivity and fleet management uses technology that is proven and reliable to deliver insight into truck utilization, compliance, safety, performance and productivity. There is sufficient experience with forklift connectivity to ensure that implementation issues are resolved relatively quickly and significant value is realized if the organization sets clear goals. Organizations that address these issues directly today will realize the benefits of forklift connectivity in the short term, while positioning themselves to build on the technology foundation it provides in the long term.