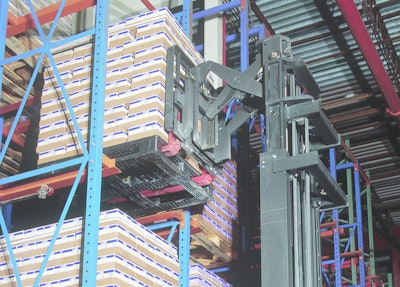
The Food Safety and Modernization Act (FSMA) has moved into its fourth year of practice, highlighting the continued importance for food and beverage processors and suppliers to reassess how they’ve been operating over that period.
But, as with the implementation of any new strategic and overarching guideline, what really has some companies thinking is not just (or merely) compliance – it’s the potential costs associated with operational change.
FSMA dictates a number of regulations and inspections, fundamentally placing it in the category of the biggest overhaul of the food safety system in nearly 100 years. While these preventative measures will result in a safer supply chain, the costs can easily rise for companies trying to comply with such extensive organizational change, particularly those unsure of how to efficiently meet the new standards in front of them.
The situation has placed reusable plastic packaging in the spotlight as a solution. Reusable plastic packaging can support the sanitation standards FSMA demands. It also opens up opportunities to make holistic supply chain improvements and reduce costs, while enabling compliance.
Let’s explore just how your company’s answer to FSMA might be right under your product.
For years, palletization has driven efficiency in today’s food processing plants and distribution systems. Raw materials and finished goods fit on standard sized pallets and these pallets fit into a 53-foot trailer for distribution. In today’s food and beverage supply chains, these pallets touch nearly everything.
With that in mind, one thing has become increasingly clear during the past four years of the FSMA: Companies that are reviewing and reevaluating the packaging used to ship their goods have a ready-made solution.
It just makes sense. The FSMA guidelines set up safety parameters throughout the supply chain, at every touchpoint, to proactively prevent food contamination. If every touchpoint is an opportunity for improvement, clear focus would be on transport pallets.
Food Safety in the Foreground
I recently had the opportunity to serve on the working group that assisted the Reusable Packaging Association (RPA) with the development of comprehensive guidelines for the use of reusable plastic containers for fresh and perishable products in the supply chain.
These guidelines detail best practices for washing, handling, storing, packing, displaying and managing reusable plastic containers in the supply chain.
These updated protocols are essential to what we do in this industry, particularly as we strive to meet and exceed the strict rules in the food and beverage supply chain. These RPA guidelines dovetail perfectly with the FSMA instructions. That provides a true opportunity for companies ready and willing to explore the role reusable packaging plays in their adherence to the new standards.
Reusable plastic packaging can be a vital option to help companies meet current and future FSMA standards.
Why reusable pallets?
Food and beverage companies are implementing plastic pallets and containers at an ever-increasing rate, for economic, environmental and sanitation benefits. They’re reusable, hygienic, easily sanitized, non-porous and can cleanly move and store food products within a facility – supporting overall sanitary conditions required in the FSMA.
For transport packaging in the food and beverage industry, cleanability is top of mind. Reusable plastic pallets used within the food supply chain need to be designed with non-porous material that does not absorb moisture. These pallets feature one-piece designs with no crevices, cells, hollow area or cavities, eliminating the potential for contaminants to collect, regardless of pallet orientation (on floor, stacked, upright, etc.). An open deck pallet allows for more efficient flow-through cleaning and quick drying, getting the pallet back into your supply chain with little downtime.
The benefits don’t stop there. Plastic pallets are designed to be dimensionally consistent. They are free of sharp edges or protruding fasteners that can damage products, automation, the plant floor or personnel. They are also free of nails or staples and will not splinter or break, causing damage to machines and downtime in your facility. This ensures greater safety for the end product, cleaner workplace for floor workers, and repeatable performance that keeps your facility functioning efficiently.
There’s also more room for innovation. Reusable plastic pallets can be molded with a wide variety of innovative materials and can be processed in different ways to deliver the right performance characteristics for a given operation. These kinds of innovation include:
- FDA-approved materials - This calls for 100 percent virgin inorganic content and should be used if there is direct food contact.
- Non-porous materials that do not readily absorb environmental contaminants like odors, bacteria, pesticides, etc.
- Materials that allow for high-temperature washing. And, materials that can work in a variety of temperatures (i.e., cold storage).
- Custom coloring and identification options to color code and segregate loads.
- Materials and design that can increase edge racking capacity.
- Optional x-ray- and metal-detectable material for modernized load inspections.
The process all starts with a supply chain assessment, to determine areas to optimize. Companies exploring a reusable plastic packaging partnership should expect actual consultation to ensure the right solutions for the right opportunity. That absolutely keeps in mind the need to meet FSMA standards – and, in fact, to lead in their industry. That includes the significant benefits reusable plastic packaging provides, beyond ensuring product integrity throughout the supply chain.
Uncovering more than just a clean plant
The FSMA impacts all facets of how a company serves its customers and conducts its logistics management. That includes packaging, internal processes and education to manage packaging assets through storage, use and shipping, and how packaging is ultimately delivered to and presented in its final destination. This goes beyond the walls of the plant.
By observing your transport packaging movements, you have the unique opportunity to attain a holistic view of your entire supply chain – allowing you to see more than just reusable plastic packaging’s impact on your food safety.
When companies shift to using reusable plastic packaging, a proper next step is to adopt a management program of those pallets. Manage it like the asset it is.
Services like asset management, tracking, cleaning and replenishment are critical to the success of a reusable pallet program. With these services, decision makers and stakeholders can be sure they’re extracting full value from their assets.
Benefits don’t stop with FSMA
As companies strive to comply with FSMA with reusable pallets, there are additional benefits that can be used to justify change beyond food safety. Within any supply chain, transport packaging travels far and wide, through numerous starts and stops. Capturing all associated packaging movements that occur through the various stages of a supply chain is essential in order to comprehend the financial and environmental benefits associated with a given supply chain.
By collaborating with supply chain partners (suppliers and customers alike), companies will reduce operational expenses, streamline logistics and increase labor efficiencies at touchpoints throughout that supply chain – making positive economic and environmental impacts.
To financially justify your investment in reusable packaging, be sure to conduct a cost analysis. And, don’t forget to calculate the cost-per-trip of your packaging. With reuse, trip costs can be dramatically reduced.
It’s also good practice to gain a thorough understanding of the environmental impacts of your packaging program. Factors such as packaging weight, volume, velocity, density and more are all collected to provide a more complete picture of the sustainability score that could win or lose millions of dollars’ worth of business or drive significant, legacy-defining profit or positive environmental stewardship. One of the best ways to view a full 360-degree picture of this is through life-cycle assessment (LCA) methodology.
With the calculations available through tools like these, your business can compare the carbon emissions, solid waste generated and energy use of different packaging scenarios to help you make informed decisions.
By taking a closer look and carefully analyzing these measurements, you’ll have the data needed for your company to make a significant impact. That gives businesses a tremendous opportunity to make a difference — delivering a consumer-safe product quickly and efficiently to the marketplace, therefore increasing profitability, enhancing safety, increasing consumer confidence and saving those dollars that used to collect in loss margins.
Could a pallet really do this much?
In short, yes. Reusable plastic packaging is in the spotlight because their specific features positively impact every supply chain’s compliance with FSMA standards. But even more than that, from implementation to usage and management, reusable plastic packaging, and the partnerships forged around them, will allow companies to evaluate more than just their impact on food safety; rather, the benefits these assets will have on their economic and environmental goals. It’s a holistic diagnosis of a supply chain’s overall health – and its success is riding in hidden areas, like reusable packaging.