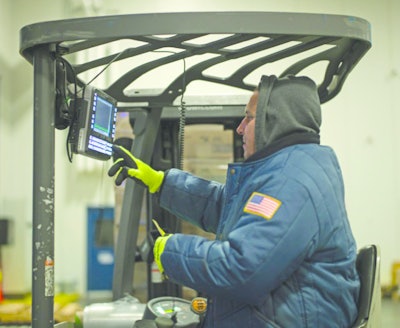
If the recent round of data from the Occupational Safety & Health Administration (OSHA) showing that 11 percent of all forklifts will be involved in some type of accident each year hasn’t already caused most warehouse managers to take a serious look at their lift truck fleet, the idea of OSHA stepping up the scrutiny on inspections of powered industrial trucks to try and reverse those accidents and injury numbers could be the final straw.
Since some industry experts claim that up to 70 percent of a lift truck’s actual cost is really dependent upon who is behind the wheel, with the lift truck itself becoming less of the focus of the sale, it’s really labor that drives lift trucks and their costs. Those are two things: labor and costs, that have a huge effect on the bottom line for everyone as the industry tries to crawl along with slow growth.
Since a lack of training is often cited as the reason for lift truck accidents, nowadays companies are approaching their lift truck operations with a laser focus on training their workforce to operate the equipment they have, and less about what the lift truck itself can do. But just like in every other phase of the food supply chain industry, technology and innovation is helping to make lift trucks safer based on the concept of keeping the operator safe, trained and secure on, or inside, the vehicle.
Keeping operators restrained: the “new” focus
One of the more alarming statistics gleaned from the OSHA data was that 42 percent of fatal accidents happened when the worker jumps off the lift truck or forklift, getting caught in its path or getting crushed by the vehicle tipping over. The second most frequent type of accident was being crushed between the vehicle and a surface (25%), and the third was getting crushed between vehicles (11%).
The main component in all these types of accidents is the operator is not secured inside or on the lift truck. So, with a renewed focus on training and safety, the lift truck industry is addressing today’s safety issues by promoting technology like operator presence, speed control and vibration-reduction systems along with trucks that produce fewer exhaust gases.
Some of the newer towing tractors and order pickers have operator presence sensors spread out over the entire floor, ensuring the driver works in a correct and safe position during operation. Newer models of reach trucks also come with curve control systems that automatically reduce the speed of the lift truck when cornering. Other new trucks come with rear-area monitoring systems that come as extras, which are designed to warn drivers by reducing the speed of the vehicle going backwards.
Controlling speed in corners is one safety feature, but improved forklift speed overall also has a hand in making today’s lift trucks safer for operators. With an emphasis on slimmer lift mast profiles for visibility, and travel speeds that are simply quicker up and down and front to back than older trucks, new technology is making it easier to operate, resulting in safer operating.
The frequent braking and driving on and off of uneven surfaces causes operator wear, as well as vehicle wear, which is something the lift truck industry has approached by introducing vibration-control systems on new models. Some manufacturers are reducing vibration by separating the lift mast and drive axle, and steering axle operations in some models, while forklifts with seats are often equipped with rubber buffers under the cab to absorb vibration for the driver.
With advances in diesel particulate filters today’s diesel lift truck is substantially more eco-friendly that diesel trucks of the past. New models with filters can remove up to 95 percent of the soot, producing emissions well below the limit permitted by law.