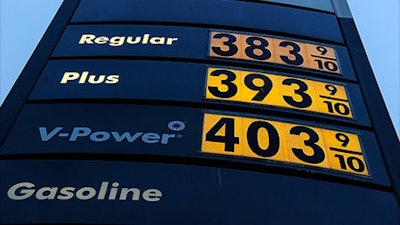
Fuel prices have been on the rise for the last few weeks, as gas prices are reaching record highs. The supply chain is feeling the impact at the pump. No matter the industry, goods must be transported via truck to get to its end destination. With the trucking industry already facing a driver shortage and a capacity crunch, transportation costs have been on the rise. Add in inflated fuel costs, and overall transportation costs will continue to climb, which will ultimately trickle down to consumers.
Whether products are moved internally by a private fleet or outsourced to carriers, all truck fleets are battling the rising costs. So, what can companies do to navigate this challenge? One major cause of fuel waste is truck idling, where reports say that billions of gallons of fuel are wasted annually, adding up to billions of dollars in lost revenue.
According to the U.S. Department of Energy, “Idling a heavy-duty truck consumes about 0.8 gallon of fuel per hour. Even when diesel costs as little as $2.50 a gallon, fuel for one 10-hour rest period will cost $20. Typically, a long-haul truck idles about 1,800 hours per year, using about 1,500 gallons of diesel. Argonne National Laboratory (Argonne) estimates that, in the U.S., rest-period truck idling consumes up to 1 billion gallons of fuel annually at a cost of around $3 billion.”
That doesn’t account for idling along other points of the supply chain, like waiting at traffic stops for extended periods of time or even waiting to get in and out of facilities, where wait times can be upwards of a few hours. While some idling can’t be avoided, speeding up other processes along the supply chain can greatly reduce overall idle times.
By law, truck drivers are legally allowed 11 hours of driving each day, but the reality is, they only spend about 6.5 hours a day on the road because of the time they spend sitting in line at pickup and drop-off points, or waiting for someone to review their paper bill of lading. That dwell and detention time is a huge pain point in the logistics industry and is a major contributor to idle times. The extra 4.5 hours adds up to. Just one truck could waste up to 3.6 gallons of fuel a day. At a conservative cost $4.50 per gallon, that adds up to $16.20 of wasted fuel per day. Multiply that out by the millions of trucks on the road every day.
Solutions to truck idling
Shippers and carriers are worried about rising fuel costs and are looking to take measures to reduce idle times specifically in hopes that will lessen the burden. In warmer weather areas, fleets can ask drivers to completely turn off their vehicles during overnight stops or have them plug into electric outlets – if the stop location offers that amenity – to reduce fuel consumption. The same could be said about colder weather areas, where drivers, instead of keeping the truck running all night to keep the cab warm, can switch to electric resources.
Automatic engine start/stop (AESS) systems, also called idle management systems, turn the engine on and off as necessary to maintain sleeper-cab temperature and sufficient battery charge. These systems do not eliminate idling but reduce it, along with associated fuel use, engine wear and emissions. If fleets aren’t already using AESS systems, they can be an inexpensive option to turn to, but they offer minimal savings in extreme weather. But buyer beware, these systems might not also be up to date with state idling restrictions.
For companies looking for a long-term fix that also improves overall operational efficiency, technology is a solution. Just looking at getting in and out of facilities and potentially addressing the 4.5 hours of wasted drive time per day, automated technology such as an electronic bill of lading that connects shippers, carriers and receivers can simplify the billing and paperwork processes for drivers, reducing idle times waiting to get in and out of a facility from over an hour to as few as 11 minutes and making drivers’ jobs easier. Such a reduction in idle time means that instead of fuel simply being wasted, it gets used to allow more freight to be moved with drivers spending more time on the road rather than sitting in lines. That extra time can also boost driver happiness, as they would rather get paid to drive than pay dwell and detention fees.
An alternative option altogether for fleets would be to make the transition away from diesel-powered vehicles. Heavy-duty, electric commercial vehicles have been a work in progress over the years, and there are still costs associated with charging them. But the impact of that is the cost of electricity doesn’t fluctuate depending on global markets. It will be interesting to see how the adoption of such vehicles progresses over the coming years, as the technology continues to advance and the push to reduce emissions by politicians grows stronger.
While electric options and the adoption of technology have costs associated with them, combatting truck idling can be addressed. The return on such investments might take a few years, but the long-term impact can prove more beneficial to companies’ bottom lines, all without having to rely as much on the volatility of a global commodities market such as oil.