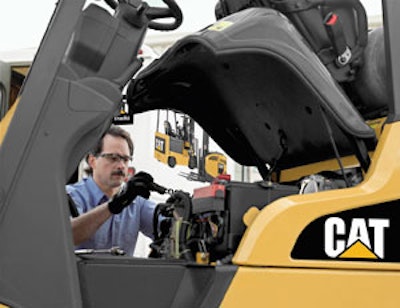
Forklift trucks are the overburdened packhorse of the warehousing business. They're driven too fast, subjected to shocks and collisions and overloaded-and yet they're expected to never fail.
"You can't prevent things from happening," says Michael Toering, manager of OEM parts marketing group for Houston-based Caterpillar Lift Trucks. "There's no such thing as 'preventative' maintenance."
The fact is that forklifts are a hefty investment, especially for companies that have to maintain large fleets. It's imperative for them to learn how to get the most out of their investment by maintaining the "health" of their lift trucks.
According to statistics, only 20 percent of warehousing operations have any kind of maintenance program and those that do are only performing the maintenance 50 percent of the time at the designated time. Too often, the norm is "maintenance by crisis," where companies wait until trucks break down before they do any kind of inspections. Companies need to break this cycle if they want to see a lower cost of ownership for their trucks. The manufacturers suggest they develop a "Planned Maintenance" mentality, where companies perform inspections on a regular basis to reduce the possibilities of cascading failures in their lift trucks' systems.
All manufacturers provide recommended maintenance periods in their service manuals. However, many operations may need to adjust these suggested PMs in order to fit their working conditions. "For example, some warehouses maintain three shifts of operation," says Wayne Wilde, director of training and technical publications for Nissan Forklift Co., Marengo, IL. "PMs may need to be increased because of the work hours their trucks are subjected to."
The experts agree that PMs should be done based on hours of usage (hour meters on each truck indicate how long they've been operating.) However, even that's not an infallible method, says James Clark, director of service and warranty for Nissan. He suggests doing PMs every 200 hours or 30 days, whichever comes first. The reason for this, he says, is that some trucks may only have "short run usage," where the engine runs for a short time and never gets up to a full operating temperature. "This leads to the buildup of moisture in the engine and the oil never gets to a temperature where the engine evaporates it." This situation may dilute oil lubrication in the truck, which accelerates engine wear.
The PM Process
A PM should take about an hour to perform on a lift truck, says Jim Fisher, of J&P Fisher Enterprises LLC, a West Chester, OH company that provides forklift consultation advice. "It should also consist of more than just a grease job and an oil change-that's only a minor part of a PM."
According to Fisher, the PM should also consist of a complete physical examination of the truck, including both visual and operational tests on the unit to ensure that all of its systems are in good working order. The technician performing the PM should make sure to speak to the lift truck operator and ask them how the truck has been running. "They have their finger on the pulse of the truck," Fisher explains.
The technician should not only change the engine oil and oil filter (for internal combustion vehicles), but also check to make sure the lift chain linkages are tight, that the forks aren't dragging on the ground and that all mast rollers are intact. They should also make sure that both brakes are working properly on the truck (two breaks are required to provide sufficient stopping power). Lubricating the vehicle is important as well-pivot points, axles, pins and bearings must all be well-lubricated.
In addition to checking the fluid levels on all systems, technicians should also make sure to replace the vehicle's hydraulic fluid and filter, according to specified intervals. Otherwise, contaminants that get in the fluid, such as metal shavings, could damage the system's electric or electromechanical valves-an expensive repair job.
Technicians must also be sure to use the proper oil for a truck's application. According to Lou Micheletto, warehouse products manager for Yale Materials Handling Corp., Greenville, NC, there are at least half-a-dozen different oils for freezer use alone.
"There are different oils for trucks that are left in minus 20 freezers as well as for trucks that operate in and out of freezers-each one requires a different oil technology." Under changing temperature conditions, using the wrong oil can lead to frothing, which leeches compressibility from the oil and promotes engine wear. "How do you extend the life of your lift truck? Use approved oils."
Tire Watch
"One of the biggest maintenance items on lift trucks is the tires. They take a beating," says Matt Ranly, senior marketing product manager for Crown Equipment Corp., New Bremen, OH. "They've got 8,000 pounds right on top of them and they're going across concrete floors, over screws and pieces of wood. They get beat up. One of the best ways that companies can save money is by paying close attention to their tires."
Joe LaFergola, manager of fleet operations for The Raymond Corp. in Greene, NY, notes that lift truck tires with flat spots on them lend themselves to the creation of vibrations. This is because the load wheel diameters on lift trucks are narrow, making for high RPMs. Lift trucks have no shock absorbers on them. The resulting vibrations caused by the damaged tire shake the body of the lift truck and cause cracking around the battery box or on the linkages of the pallet jacks. "Changing a $30 dollar wheel to avoid a $1,000 welding bill makes good business sense," he says.
Technician Training
The experts stress that the single most important factor in extending the life of a company's lift truck is the person doing the planned maintenance. If the PMs are being done by in-house technicians, it behooves a company to spend money on technical training. A qualified maintenance staff is the key to decreasing truck downtime as well as extending the life of a lift truck.
"We can assess the need and set-up a tailor-made training program to ensure that the in-house technician is well-qualified," notes Raymond's LaFergola. He suggests that a 'train the trainer" type of program be undertaken, so that after the company's chief technician receives dealer training, he will be able to train technicians under him.
"If a non-qualified technician were to attempt to diagnose problems with an advanced control system, it could lead to hours of guess work," explains Jeff Bowles, product manager for Jungheinrich Lift Truck Corp., Richmond, VA. "It can also lead to the unnecessary replacement of high dollar components-I find a lot of lift truck controllers in my warranty bin that were swapped out in the course of guesswork and there was nothing wrong with them."
Everyone in the industry knows that OSHA legally requires forklift truck operators to do a pre-shift safety inspection of their vehicles and most manufacturers offer training classes for operators in how to properly inspect their lift trucks, in order to confirm a truck is free of wear on tires, chains and forks.
"We don't expect them to be experts," notes Bruce Marti, national manager, parts and service field operations for Toyota Material Handling USA Inc., Irvine, CA. "They just need to know the basics-how to check for leaks, how to determine that fluids are at their proper levels. The daily inspection will identify a situation that could become extremely unsafe for the operator."
Companies need to make sure that their operators aren't just paying lip service to these daily inspections. Catching a problem while it's in the beginning stage can be an easy fix-such as fixing a leaky fitting by tightening it.
However, ignoring the problem could result in having to replace a bad valve or hose-a repair that could cost a company hundreds of dollars.
"There are four main objectives when performing PMs," explains Fisher of J&P Fisher. "To reduce maintenance costs, to reduce down time, to improve productivity and, most importantly, to improve safety. If you can do all four of those things, then you've performed a quality PM."
Six Steps To Planned Maintenance
Lou Micheletto, warehouse products manager for Yale Materials Handling Corp., offers these tips for lift truck maintenance and safety:
1. Operate equipment following manufacturer guidelines.
- Proper operation of lift equipment will pay long term dividends.
- Understand the truck's capacity-never handle loads that exceed truck rating.
- Follow proper industrial battery charging procedures.
2. Building maintenance needs to be done.
- Lift trucks have no suspension systems. Every bad expansion joint in a floor increases potential maintenance.
- Stretch wrap and banding material left on the floor can wrap around a wheel.
3. Stop cascading failures.
- If a problem is caught early the repair may be minimal.
- Do the per-shift inspections and take action with problems.
4. Operational maintenance vs. crisis maintenance.
- Operational Maintenance (OM) done on a timely basis will catch minor problems before they can cascade into major problems.
- Do the OM based on the hour meter, not the calendar.
5. Use the right replacement part.
- Non-OEM parts may fit but may not do the job.
- All oils are not created equal.
6. Always use safe operating procedures.
- Follow proper forklift safety tips.