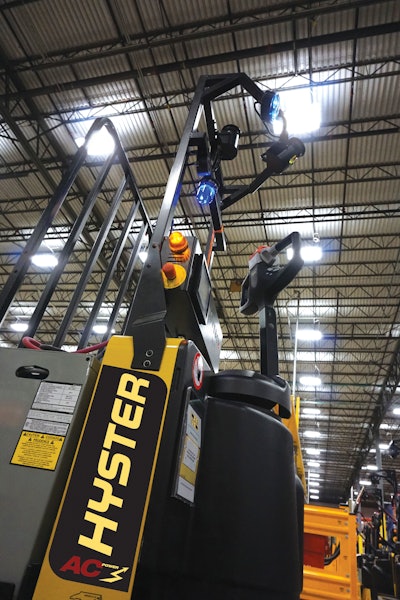
As though the tough labor environment was not enough, soaring throughput targets and rising safety expectations are pressing food logistics operations to do more. As food manufacturing plants look for ways to stay ahead, newer autonomous guided vehicle (AGV) solutions offer potential to solve long-standing, nagging issues operations have simply “dealt with” for years or even decades.
But, what are those challenges? As automation technology has matured, robotic lift trucks have become an increasingly powerful, flexible solution to shore up labor needs while exceeding productivity targets.
A study commissioned by Hyster Company and administered by a third party asked food and beverage operations to identify where automation can address long-festering challenges and provide a competitive advantage.
According to a sample size of 500 respondents in the United States:
- 40% report that lift truck operator turnover is their biggest pain point, followed by 30% who are concerned about increasing labor wages.
- 76% are either researching solutions, in need of help or unhappy with their current automation strategy.
- Truck unloading is the most common use of automation at 45%, followed by 40% who report using automation for the purpose of moving materials such as pallets or carts.
Reducing turnover and labor costs
Meeting or beating aggressive productivity targets leaves no room for uncertainty — everything needs to be planned and executed with precision — especially staffing. But, maintaining staffing levels is a persistent challenge.
Employee turnover, sick days and other unexpected absenteeism pose a constant threat of disruption. High turnover doesn’t just limit your ability to achieve targets and grow topline revenue – it can drive up costs, putting a serious dent in already thin margins. The expenses and time required to recruit, hire and train new employees causes intense competition for the limited available labor pool. Turnover is a nagging, steadily growing challenge that’s plagued logistics operations seemingly forever. But, you don’t have to accept turnover and the major costs associated with it as just status quo.
Using robotics as a continuity solution
Robotics offer a practical, powerful strategy to achieve steady productivity, guard against disruptions to critical workflows and even combat one of the root sources of employee turnover.
Robots do not require frequent rest breaks, take vacations, call out of work or quit. No fatigue or slumping productivity as their shift goes on or resistance to working non-traditional hours. Robots perform in accordance with their programming, hour after hour, day or night.
They also excel at efficiently completing repetitive tasks, which can help free up workers to focus on more engaging, value added positions – boosting employee engagement, productivity and retention.
Academic research shows that organizations augmented by automation technologies are 33% more likely to be more engaging, “human friendly” workplaces, in which employees are 31% more productive. That makes robotics not just a tool to plug holes in your labor pool, but a tool to help reduce churn. A study by Gallup found that organizations with better employee engagement realize substantially better retention, fewer accidents and higher profitability.
Click here to hear more about robotics in warehousing:
Managing costs with robotics
In addition to helping keep costs in check by curbing turnover, automated solutions like robotic lift trucks can also help reduce other costs:
- Wages
- Insurance
- Workers’ compensation
- Retraining
Overall savings realized by using robotic lift trucks can help operations quickly achieve a return on investment, possibly within two years or less for multi-shift operations. And, unlike fixed automation like sorters and conveyor-based systems, robotic lift trucks lend themselves to a flexible, phased approach. Not every business has resources so vast it can afford to behave as a technology incubator, committing massive sums in efforts to refine technology for unknown outcomes. In many cases, automation is a big step and it has to work.
Because they can be deployed as individual units or scaled to an entire fleet, robotic lift trucks allow operations to demonstrate ROI and proof of concept before making a full investment. Infrastructure-free navigation enables robotic units to be deployed relatively quickly to workflows where the need is most urgent before expanding to other applications. As the need arises, additional units can be deployed in a timely manner – think of this as adding a room to a house, rather than constructing an entirely new house.
Address changing needs and solve problems you may not have known about
Traditional fixed automation may provide an appropriate solution for the time of installation, but it can be challenging and resource-intensive to reconfigure. The pace of change is faster than ever, so a best-fit automation strategy requires flexibility to adapt to changing requirements.
Managers may have once resigned themselves to living with the rigidity of fixed automation, but the flexibility offered by robotic lift trucks means that is no longer a necessary concession. From manufacturing to food processing facilities, robotic lift trucks can help operations nimbly respond to changing circumstances.
More capability than unloading and transportation
Truck unloading and material movement are the most popular uses for automation identified by the survey. But, as the range of robotic lift trucks has expanded to include pallet trucks, reach trucks, tow tractors and counterbalanced stackers, so too has the scope of capabilities. Robotics can be an efficient solution for a spectrum of applications and workflows, such as:
- Transport of single or double pallet loads to marshaling/staging areas
- Handle smaller width pallets and stacking or unstacking loads
- Kitting separate ingredients and other items to be supplied as one unit
- Deposit and retrieve loads from as high as 30 feet
For example, a beverage bottling facility that struggles to source labor from the surrounding rural and suburban communities may have once resorted to bringing in lift truck operators from major metropolitan areas over an hour away. To reduce labor dependency, the operation could use a robotic lift truck to transport pallets of raw ingredients. Once the drinks are packaged and palletized, a robotic lift truck might retrieve loads from the conveyor and transport the finished product to storage, before retrieving when ready to be staged for a trailer.
An increasingly practical solution
Automation drivers like labor cost and availability are not abating anytime soon. Together with tech advances, new and existing challenges will make robotics an even more vital and effective means to reach peak performance. However, the right strategy will vary for every operation and application. The most effective use of robotics relies on an assessment of where and how operations can best stand to gain from using robotics.