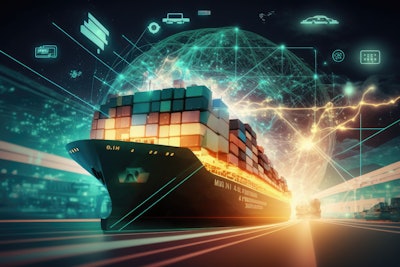
End-to-end visibility and transparency in global supply chains, particularly within the food supply chains, have become hot topics of discussion. From major food and beverage (F&B) companies to small- to medium enterprises (SMEs), organizations are increasingly automating their supply chain processes and striving to achieve comprehensive visibility.
However, the question remains: are they truly gaining visibility into the key milestones of their container shipments? And more importantly, do they know which shipment legs and milestones are critical to monitor before disruptions occur, thereby minimising risks, preventing food wastage, and ensuring timely deliveries to end customers?
This means going beyond the traditional approach of monitoring container locations and diving into the realm of use-case or scenario-based exceptions.
Let's consider a scenario involving an F&B company based in New Zealand that exports fresh fruits to a major retail supermarket chain in the UK. The supply chain begins with the F&B company shipping fresh fruits from New Zealand to the UK. Upon arrival in the UK, a freight forwarder takes charge of local haulage, transporting the fruits to a third-party repacking site within the UK, where the packaging process is completed. The packed fruits are then delivered to the distribution centres of the supermarket chain across the country.
Although having real-time information about the shipment's location during transit might seem like sufficient visibility to plan downstream operations and update stakeholders on the delivery status, numerous scenarios can still jeopardize timely delivery. Port congestion and weather delays are just a few of the factors involved; other crucial considerations must be made.
Unforeseen scenarios: Potential challenges for the F&B company
Imagine the F&B company with transhipment at Singapore port. In this scenario, the first vessel leg, responsible for transporting the F&B company's containers from New Zealand to Singapore, experiences a delay for various reasons. Consequently, it arrives later than the second vessel, which is supposed to carry the containers from Singapore to the UK. The second vessel has already departed from the transhipment port, unbeknownst to the company.
In this situation, it becomes crucial for the F&B company to be alerted in advance about the potential risk of missing the transhipment. With timely notification, the company can proactively secure space in the next available vessel. Failure to receive such an alert could lead to the containers lingering at the transhipment port, causing further delays.
This example highlights the necessity of understanding the role of supply chain visibility, which goes beyond tracking and addresses potential disruptions, ensuring a smooth and efficient supply chain operation.
Dwell time at point of loading
The F&B company may encounter situations where specific containers remain idle at the point of loading (POL) without any updates from the carrier regarding the delay. In such instances, the company might mistakenly assume that the containers have been loaded and departed while, in reality, they are still at the port. Similarly, container rollovers could happen at the transhipment port as well. Although such occurrences may be infrequent, they can prove to be operational nightmares for exporters, leading to the challenge of managing dissatisfied customers at the receiving end.
The terminal milestones for downstream planning
Basic tracking provides exporters with confirmation of shipment arrivals at the destination port, like the UK in this scenario. However, crucial information about the container status at the terminal remains elusive. With port terminal operations playing a pivotal role in supply chains, the involvement of multiple stakeholders and the complexities of various tracking technologies contribute to a wide visibility gap across terminals. In light of this, how can the F&B company effectively stay informed about potential delays? Let's explore the solution.
Delays caused by customs and holds can lead to unintended Demurrage charges for companies lacking visibility into crucial container milestones at the terminal. Moreover, coordinating timely drayage to move containers out of the gate poses significant challenges. To navigate these hurdles, it becomes crucial to identify and filter containers awaiting the next step, such as those discharged but not yet gated out. Only by gaining visibility into essential information like container availability for pick-up, appointment dates, and yard locations can F&B companies streamline their downstream logistics, ensuring efficient operations and cost-effective supply chain management.
But, how do you address exception management and define crucial alerts within the visibility solution?
Defining vital alerts in the visibility solution
An essential aspect of visibility in food supply chains is the ability to prioritize shipments based on their level of urgency and attention required. For instance, handling exceptions such as rollovers, pre-arrivals, route deviations, unexpected delays due to natural disasters and adverse weather conditions, or customs clearance issues takes precedence over merely knowing the shipment's transit status.
Here are the crucial alerts:
- Transhipment status. Whether the transhipment is successful or delayed.
- Container rollovers. Alerts for instances where containers are rolled over to a later departure.
- Change in ETA. Updates on any changes to the estimated time of arrival.
- Port congestion and delays. Information regarding port congestion and its impact on shipment timelines.
- Early receipt date and vessel cutoffs. Provide the F&B company with details about the early receipt date and cutoffs to adjust delivery schedules and avoid additional costs.
- Last free days. Monitoring the available free days before demurrage charges accrue.
- Holds and customs delays. Alerts on any holds or delays in customs clearance processes.
Data insights: Keeping the F&B supply chain in motion
In the face of operational bottlenecks, the F&B company must ensure its products continue to move smoothly. One effective way to achieve this is by leveraging data beyond basic container visibility during transit. Data that can provide valuable insights that drive critical decisions, significantly impacting the ROI of the food supply chain.
- Average transit times. Analysing and comparing initial ETA to final ETA helps identify the longest delays and improves lead time planning.
- Carrier performance analytics. Comprehensive reports on carrier performance empowers F&B businesses to identify the most suitable carriers for specific trade routes. With valuable insights, companies can negotiate contracts more effectively, ensuring better risk diversification within their supply chain.
- Data filters. With these capabilities, the F&B company can access information according to their specific needs. This includes tracking the number of containers on a particular vessel in transit, identifying containers affected by delays, and assessing the value of the goods. Moreover, this enables tracking at an order or product level using internal reference numbers and sorting shipment statuses based on carriers (SCAC), port of destination, Bill of Lading, or product categories. This flexibility in data access empowers the F&B company to make informed decisions and streamline its supply chain operations with greater precision.
Conclusion
In the ever-evolving food and beverage industry, supply chain visibility has emerged as a game-changer rather than a mere tracking tool. By embracing a holistic approach to supply chain visibility, the F&B industry gains the power to anticipate, proactively respond, and strategize like never before. From understanding crucial container milestones at port terminals to prioritising shipments based on urgency, from unlocking data insights to optimising trade routes to leveraging carrier analytics for effective negotiations, every aspect contributes to a more agile, efficient and resilient food supply chain. For F&B companies, this shift in perspective transforms a visibility solution into a potent competitive advantage.