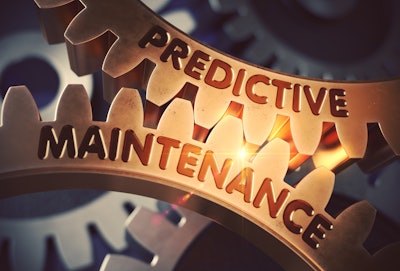
For many Americans, summer came early this year, with higher-than-average temperatures baking much of the country. After a long winter, people are outdoors again, gathering with their family and friends.
This is good news not just for businesses across the country, but also for the food and beverage companies whose products are staples on store shelves.
There is already evidence of pent-up demand for these products: Beverage giants reported a sales spike of as much as 35% beginning in February, months before the usual summer rush. Snack food companies are producing as fast as they can to keep up with skyrocketing demand.
It’s shaping up to be a busy summer and a banner year for food and beverage brands. However, these companies face the challenge of consistently getting food and drinks to the shelves of stores in every part of the country, ensuring those shelves remain stocked or else risk losing sales to competitor brands.
This means their profit margins will be dependent on the vehicle fleets they use to move their products from town to town, state to state and from one side of the country to the other. It means every delay on the road will eat at the bottom line.
Food and beverage companies are depending more than ever on their trucks. And these vehicles are aging.
Challenges in distribution
When consumers and businesses are flush with cash, the average age of all vehicles on the road—everything from cars to big-rig trucks—goes down. This is because drivers are more likely to spring for new vehicles when they have the resources they need.
Then there are economic downturns, and times when businesses and consumers watch every penny, and try to get longer life out of the things they already have. That’s where U.S. businesses and consumers have been for some time, and the reason the average age of cars and trucks has been going up.
For food and beverage companies already facing a busy summer, a fleet of older vehicles presents two problems: more time spent waiting on repairs and increased difficulty recruiting new drivers.
Unsatisfactory working conditions are among the main reasons truck drivers have been leaving the industry, creating a nationwide driver shortage. To drivers, few things are as disappointing as sitting idle, waiting on parts or repairs when they should be driving and earning.
Aging fleets make the transportation industry also seem less attractive to younger drivers, who the American Trucking Association hopes will help them reach their goal of putting 1 million new drivers behind the wheel by 2030.
The idea of losing time due to a lack of drivers or unplanned breakdowns and repairs—when they should be delivering product—is a pressing problem for food and beverage companies, especially during peak season. Fortunately, there are new technologies that can help them maximize the time they spend on the road.
From preventive to predictive maintenance
Food and beverage giants that operate vehicle fleets keep their trucks on regular schedules of preventive maintenance, replacing parts and vehicles when they reach a certain age in the hope of averting a breakdown. Even with routine tune-ups, parts still wear out and trucks still break down at unexpected times.
Every vehicle is used differently and driven in variable conditions, so the one-size-fits-all approach to preventive maintenance falls short.
There is a way to better tailor the right repair to the right vehicle at the right time and move to a model of predictive maintenance that will be more effective at keeping vehicles on the road. The key lies in the data.
Trucks are constantly generating valuable telematics data with sensors and electronic logging devices (ELDs), but this data—often presented in no particular order—can easily overwhelm fleet managers.
These managers should avail themselves of new technologies that synthesize the information their fleets are generating and take from it actionable insights about which vehicles need specific repairs and how soon they need them. Predictive analytics make this level of knowledge possible, down to each individual vehicle in a fleet. Analytics programs synthesize and comb through volumes of data and recommend specific actions to maintenance teams, enabling them to proactively order necessary parts and keep drivers happy by avoiding unplanned downtime.
Standard preventive maintenance that is outlined by OEMs—or doing the same repairs to every vehicle based on predetermined, generic intervals—represents the old way of doing things. Using analytics to put every individual vehicle on its own dynamic repair schedule is the wave of the future. It offers fleet managers the chance to go beyond the one-size-fits-all approach and achieve a predictive maintenance strategy.
Facing cost pressures from every side, food and beverage companies need to make the most of the warmer months ahead, when demand for their products is through the roof. Stores in every town in America are counting on an ample supply of soft drinks, beer and the foods consumers associate with summer.
Relying on yesterday’s maintenance schedules means taking the risk of letting those consumers down. Luckily, predictive maintenance technology ensures food and beverage companies no longer need to take that risk.