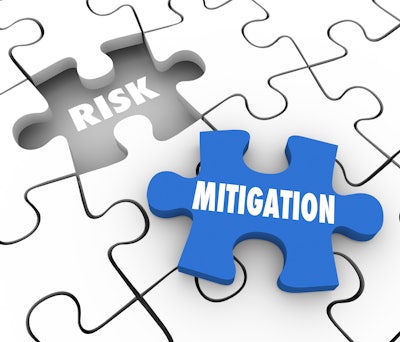
An above-average number of food recalls over the past year has sparked widespread concern among consumers. Anxiety is running high as shoppers scrutinize grocery store shelves with caution, seeking the products they need and contemplating which ones carry the lowest risk of contamination. The FDA reported a total of 1,908 product withdrawals in the most recent fiscal year — the highest number since 2019 when 2,046 products were removed from the market. This surge underscores the need for enhanced quality control measures.
What’s more, incidents like listeria outbreaks in deli meats and E. coli-laced onions impact more than the health of people who consume tainted products. These occurrences, combined with declining public trust, have underscored vulnerabilities in the U.S. food safety system. According to a recent Gallup poll, only 39% of Americans trust the government to ensure the security of the food supply, down from 47% in 2019. This highlights the need for manufacturers to safeguard product integrity and prevent contamination proactively.
Beyond federal regulations, advanced technology, such as statistical process control (SPC) software, offers new avenues for food manufacturers to minimize risks and strengthen internal processes. From real-time quality monitoring to robust traceability for recalls, SPC systems empower companies to meet heightened food safety standards and stand out from competitors. Paired with complementary tools like warehouse management systems (WMS) and manufacturing execution systems (MES), these data-driven tools can enhance efficiency, compliance, and consumer trust. Taking control of food safety and auditing processes by harnessing the power of cutting-edge technology helps food manufacturers stay compliant, competitive, customer-focused, and ahead of shifting regulations.
SPC streamlines auditing and compliance in food manufacturing
SPC software is an innovative tool that uses data-driven insights to monitor, control, and optimize processes. By tracking metrics like temperature, humidity, and weight in real time, SPC flags deviations that could compromise product safety or quality, enabling companies to address problems before they escalate.
With traditional, paper-based systems still prevalent among 75% of food and beverage manufacturers, organizations without an automated SPC solution remain vulnerable to inefficiencies, increased costs, and major recalls. Advanced SPC systems provide a modern alternative that can streamline these processes and enhance precision.
The complexity of food manufacturing — and its many regulations — demands rigorous compliance efforts. SPC software simplifies this by enabling lot genealogy and traceability, seamlessly tracking every ingredient from raw material acquisition to final product distribution. For example, consider a batch of contaminated peanut butter detected during production. With lot traceability, it’s possible to quickly identify affected batches and pinpoint impacted stores while collaborating with suppliers to rectify issues and prevent future occurrences.
SPC software can also generate detailed reports, boosting manufacturers' confidence ahead of audits. Navigating FDA guidelines or tighter export standards is more manageable with easily accessible data, fostering transparency and regulatory compliance.
Revolutionize recall management to minimize damage
Taking quick and precise action can mitigate reputational and financial consequences when incidents occur. SPC systems accelerate recall initiation by identifying which batches are linked to faulty processes or contaminated raw materials. With clear genealogy, manufacturers can react swiftly—saving time, money, and, most importantly, consumer trust.
Many companies without SPC report average recall costs hitting $10 million per event, fueled by lost revenue, replacement products, and legal action. By enabling real-time data capture and analysis, SPC minimizes these consequences, protecting companies’ financial stability and public persona.
While SPC stands out as a robust quality solution, complementary tools like WMS and MES can take proactivity one step further by also addressing significant pain points in supply chain visibility, inventory control, and production accountability.
For manufacturers managing complex supply chains, WMS platforms bring clarity and efficiency to inventory tracking. Real-time visibility into material movements, expiration dates, and storage conditions ensures compliance with FDA safety standards while reducing waste and spoilage.
Mid-to-large-scale manufacturers looking for end-to-end workflow optimization can rely on MES software to improve production planning and execution. Real-time monitoring and predictive maintenance allow for proactive resolution of disruptions to ensure consistent quality and power a competitive market edge.
These technologies work in tandem with SPC to offer a comprehensive solution for companies aiming to meet rigorous safety, quality, and operational goals. Other key benefits of WMS and MES in food manufacturing include:
● Enhanced compliance with labeling and allergen requirements
● Real-time production flow visibility for improved responsiveness
● Inventory management that prevents overstock or understock scenarios
● Efficient handling of perishable goods under stringent temperature controls
Food safety technology is non-negotiable
Recent advancements, like whole-genome sequencing for pathogen tracing, underscore just how sophisticated food safety requirements have become. Yet, as inspection methods improve, so too do consumer expectations. Over 53% of Americans report avoiding certain brands due to recent recalls, making proactive measures essential for building trust in an increasingly skeptical market.
Solutions like SPC, WMS, and MES safeguard against recalls and transform food safety strategies. These industry-leading systems elevate companies from reactive problem-solvers to proactive risk managers, establishing brands as trusted marketplace leaders.
No food manufacturer is immune to the possibility of a recall. However, scalable and innovative technology solutions — like SPC software — empower companies to prepare, respond, and thrive in a landscape where safety is paramount. Organizations that combine SPC with WMS and MES can better manage processes that affect quality control and efficiency.
For food manufacturers and quality assurance professionals, modernizing safety systems with tools like SPC offers a competitive advantage rather than an optional investment. While recalls and outbreaks may be inevitable, the ability to quickly adapt and address these challenges will make or break a brand’s resilience.