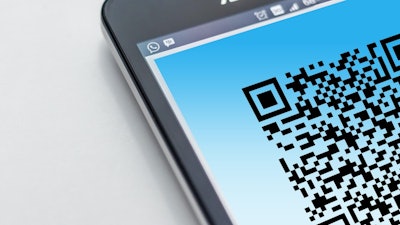
Across the country, supply chains have been severely affected by issues brought on by the pandemic; limiting the capacity to get products to the end of the line in any sort of timely fashion. But, for an industry so reliant on the timely delivery of materials and the overall adherence to schedules, the transportation and logistics (T&L) industry may be feeling the pains of these issues more than others.
As the pandemic keeps employees working remotely, managing operations and device downtime remains challenging for T&L organizations as they have employees dispersed in multiple locations and working from different devices. In fact, according to a SOTI report, T&L organizations are losing more than 3 hours per employee each work week dealing with device downtime, whether out in the field or for operations.
It is clear not having the right mobile technology infrastructure can hinder overall company operations in this sector, causing further inefficiencies across the entire supply chain and affecting the consumer-business relationship.
Lack of integration and room for manual errors
Employees in the space have identified and become aware of the lack of integration when it comes to technological aid in the T&L space. For example, the SOTI report outlined 45% of T&L employees are updating multiple systems manually and 31% of employees state legacy technology is not fully integrated with new systems. This opens the door for manual errors, inability to provide remote access to employees, and most importantly, cybersecurity risks. Without a secure platform in place, attacks on unsecured devices, like employee laptops or self-serve customer kiosks, can lead to data breaches on corporate or consumer data.
With the right mobility management platform, employees can gain complete lifecycle management of Internet of Things (IoT)-enabled devices, including securing, managing and supporting all endpoints to ensure the organization can stay up and running while protected against data breaches from network-connected devices as employees work remotely.
Downtime and delaying shipments
While companies have begun investing in technology to catch up, they are still struggling. The same SOTI report showed that of the T&L professionals surveyed, 70% listed device downtime as the top concern in their business. Furthermore, 24% of surveyed employees site systems are not upgraded frequently enough, which when disregarded, can also cause delays in information being shared between retail and supply chain partners. It is crucial to note that after acquiring additional technology support, it is vital to train staff to reap the true benefits of the investment as 26% of surveyed employees also call out a lack of staff training on the use of technology.
Combined with an integrated business-critical mobility strategy, mobile technology can enable an organization to realize performance gains, see an increase in worker productivity, an improvement in customer satisfaction, and most importantly, it can help ensure the business is always safe, connected and on time, particularly in times of crisis.
As T&L companies look to invest in technology to create further efficiencies within the supply chain, they must be strategic about the technology they have already purchased, otherwise these investments will not make their processes better or more efficient.
Mobility is key
Mobile devices and apps – when utilized in tandem with the right business mobility strategy and platform – hold the key to real-time visibility on products, warehouse workers, drivers and everything in between, improving efficiency, accuracy and timeliness across the entire delivery process. T&L companies need to evaluate every step along their supply chain; speaking with employees to truly take stock of where inefficiencies exist that can be corrected and then applying those lessons learned to their operations plan for future technology investments.
With the addition of IoT, retailers and logistics partners can now use RFID tags and sensors to accurately track inventory and delivery. These solutions will also provide insights that can help businesses make informed decisions, such as when to scale employee capacity up or down and when to adapt operations in response to a disruption, ensuring minimal delay and an efficient supply chain to meet demand.
As retailers strategize and plan for the incoming wave of returns in the last quarter of 2021, there is an opportunity to streamline and improve the operations of their organization for the long-term. Through a combination of policy changes and technology implementation, T&L organizations can become more resilient, adaptable and streamlined.
Looking forward, it will take some time for supply chains to catch up and return to normal levels. This is unavoidable. But, what the industry can do is begin preparing and strategizing to create a more efficient supply chain – one that can survive with relatively little disruption when the next major issue inevitably arrives.
Click here to hear more about technology and employees working in tandem: