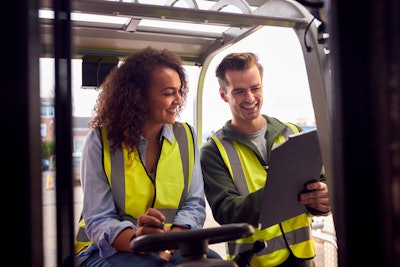
The recent U.S. port strike has sent shockwaves through supply chains, creating significant challenges for warehouse operations at major retailers. These businesses now face shipping delays and logistical confusion leaving warehouse managers on the frontlines to adapt quickly to ensure that operational setbacks are minimized.
With a focus on real-time communication, task flexibility, and maintaining worker morale, managers can effectively steer their teams through this difficult period. In order to best support the frontline, supply chain leaders should implement these key strategies to maintain productivity, safety, and efficiency during disruptions.
1. Real-time communication: The backbone of operational stability
Clear and transparent communication is critical. Without it, confusion spreads quickly, hampering productivity and creating safety risks. Managers must ensure that all frontline workers are kept informed about the changes of the work environment and how it influences daily operations.
Use mobile-first tools for instant updates. Mobile platforms should become a central tool in this effort, allowing managers to send real-time updates on shipment statuses, task assignments, and any last-minute changes to the workflow. These tools are supportive in maintaining operational coherence in rapidly shifting situations. With mobile apps or messaging platforms, warehouse workers can stay informed on what’s happening as it unfolds, ensuring the entire team is on the same page.
Transparent messaging to reduce uncertainty. Clear messaging reduces anxiety and allows employees to focus on their responsibilities. Workers should understand how shipping delays will impact shipment timelines, work priorities, and the expected length of any changes to their tasks. Managers must openly communicate these details, ensuring employees know their role in mitigating the broader challenges. When workers have clarity on how their job fits into the evolving landscape, it leads to more informed and confident decision-making at the ground level.
Frequent check-ins to assess and adjust. Regular briefings—whether in-person or virtual—should be a key part of the communication strategy. These briefings not only allow managers to provide updates and guidance but also give workers a platform to voice concerns. Listening to employee feedback ensures that managers can adjust strategies in response to real-time issues, and workers feel heard and supported. These frequent check-ins serve as touchpoints to keep everyone aligned, boosting coordination and productivity.
2. Flexibility and agility in task management
Adapting to shipping delays means workforce flexibility is essential. As shipment schedules become unpredictable, warehouse managers must find ways to dynamically allocate labor where it is most needed. This requires agile scheduling and a continuous focus on upskilling workers to handle new tasks.
Agile scheduling for shifting workloads. Warehouse teams may need to operate under unconventional hours to accommodate delayed shipments. Whether it’s adjusting shifts to manage late arrivals or extending workdays to keep pace with demand, agile scheduling ensures that the right number of workers are available when needed. Dynamic shift management tools can help by automating these adjustments, allowing managers to assign workers based on real-time demand.
On-demand learning to address task changes. With changing priorities comes new responsibilities. Managers should provide on-demand learning opportunities to equip workers for evolving tasks and new ongoing changes. Just-in-time training can help workers rapidly develop the skills needed to complete unfamiliar tasks safely and efficiently. Whether it's learning new safety protocols or adapting to new warehouse technologies, continuous learning ensures the workforce is adaptable and ready for change.
3. Maintaining productivity and morale in challenging times
One of the greatest challenges during disruptions like a strike is the toll it can take on worker morale. Employees are likely to feel stressed or overwhelmed due to the uncertainty and increased workload. Managers must be proactive in maintaining morale to keep productivity high.
Recognizing and rewarding flexibility. Acknowledging frontline workers for their adaptability and resilience is crucial in boosting morale. A simple gesture of recognition for those who have stepped up during the strike can have a powerful impact. Managers can use formal recognition programs or informal praise to highlight individual and team contributions. This recognition not only improves morale but also strengthens employee engagement and loyalty during tough times.
Deepening employee engagement. To further boost engagement, managers can introduce team-building activities or stress-relief initiatives. Even in high-pressure environments, small actions to improve employee well-being can go a long way. Managers should foster a positive work environment where workers feel supported and valued, reducing the risk of burnout and ensuring sustained productivity.
4. Upskilling managers for effective leadership
Upskilling warehouse managers to better handle crises and make swift decisions ensures that the entire operation runs smoothly. It’s important that managers are able to assess changes in production needs and reallocate resources accordingly. This requires leadership training that emphasizes adaptability, strategic thinking, and quick decision-making under pressure.
Leadership training for flexibility and decision-making. Providing managers with real-time data on shipment statuses and workload distribution helps them make informed decisions faster. With proper training, managers can assess potential risks, adjust staffing, and redeploy resources in real-time to prevent bottlenecks. The ability to react swiftly to operational challenges minimizes the impact of disruptions on the broader supply chain.
5. Ensuring safety during operational shifts
As new tasks are assigned and production ramps up after delays, safety must remain a top priority. Workers may be asked to handle new machinery or unfamiliar processes which could lead to an increase of accidents. To mitigate these risks, warehouse managers must prioritize safety training and conduct frequent risk assessments.
Safety protocols and continuous training. Reskilling employees for new roles should always include safety training. Workers must be reminded of existing protocols and informed of any new safety measures required for their changed responsibilities. This training can be delivered through on-demand platforms or in small group sessions, depending on the nature of the new tasks.
Risk assessments to ensure compliance. Managers should also conduct risk assessments to ensure that all machinery, equipment, and processes are safe to use following operational changes. This is particularly important after a period of downtime, where machinery may not have been in regular use. A thorough assessment of equipment and adherence to safety standards ensures that workers are protected and that operations resume smoothly.
Navigating the disruption caused by strikes and shipping delays requires warehouse managers to be adaptable, proactive, and highly communicative. By focusing on real-time communication, agile scheduling, and continuous training, managers can mitigate the impact of disruptions and keep operations running smoothly. Maintaining worker morale and safety during these times is essential to preserving long-term productivity and ensuring that businesses can recover swiftly from supply chain interruptions.
Effective leadership is key to navigating these challenging circumstances. With the right training and tools, managers can lead their teams through any disruption, ensuring that the supply chain remains as resilient as possible in the face of adversity.