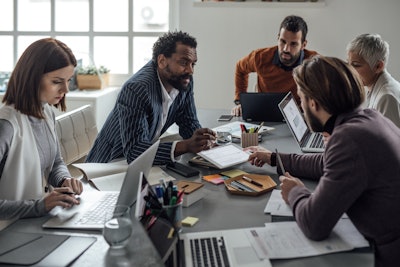
As technology and innovation continue to expand the capabilities of distribution operations, companies are looking to automation to solve the rising labor costs, high turnover, and increasing productivity demands.
While automated solutions can solve many of these demands, they are likely expensive and can be difficult to show a robust ROI. Additionally, not all organizations have the luxury of investing in fully autonomous systems or incorporating innovative technology into existing operations, leaving the question, how do you compete and grow, while driving down costs without breaking the bank?
Most companies are diligently driving down labor costs by improving processes, modifying material flow/layout configurations, and making low-cost adjustments to storage and pick equipment, however a broader topic of workforce development must also be considered to remain competitive.
When considering workforce development, multiple topics come to mind, including staffing levels, shift structures, labor rates, key performance indicators, incentive programs, bonus programs, pay for performance, work culture, work environment, attracting labor force, and increasing retention.
The foundation of most of the above is applicable to any facility that relies on an integrated workplace of people, equipment, and technology to support daily operational goals, and is known as a labor management program.
When considering how a labor management program can keep an organization competitive in today’s market, it is important to understand the facts and fiction often associated with labor management.
Labor management is just a software solution – fact or fiction?
Fiction. While a labor management program is often associated with a software solution, this view is extremely limiting and does not capture the true value a comprehensive labor management program can add to an organization. Labor management software (or technology) alone cannot make an organization more productive.
To capture the full scope of possibilities, it is more accurate to think of labor management software as one part of a labor management program, which can enhance productivity and assist with managing labor metrics and reporting. This system complements standardized processes, automation, layout, shift strategies, optimized storage, replenishment policies, travel paths, slotting, waving/batching strategies, directed work/zoning logic, as well as performance standards, which includes employee assessment, incentives, training, structured engagement, and an accountability infrastructure.
Labor management programs require dedicated engineers – fact or fiction?
Fiction. While it is beneficial to have organizational or site engineers support labor management standards, it is not a requirement to get started or improve an existing labor management program.
Most program success depends more on the creation of a strategy for improvement and an operational leadership team that understands how daily decisions impact the program outcome. To sustain a labor management program, even one with robust standards and software, leaders must understand how to remove barriers that impact productivity. These barriers can be systemic, staffing, non-standard processes, exceptions, behavioral gaps, inadequate training, building layout, and ergonomics.
As an organization matures, industrial engineers are often hired to support labor management programs, but many times these resources are utilized extensively on larger projects which may take them away from the tasks required to maintain the system. An alternative to organizations is to engage labor standard consultants to assist with operational assessments, strategic planning, and labor standard development.
Labor management programs require more than operational involvement – fact or fiction?
Fact. Labor management is a culture for all levels of an organization, and not only all levels of the operations, but all supporting departments. This includes but is not limited to human resources, safety, quality, training, warehouse support and planning, and slotting, to name a few. This level of engagement helps develop buy in, as well as creates understanding of how a labor management program will benefit the business. Engaging others in the creation of a program also assists with the development of accurate labor standards by ensuring the inclusion of appropriate safety and quality actions, proper application of personal time, fatigue, and delay (PF&D), establishing individual accountability through labor policy, providing resources during go-live, as well greatly increasing the support of the change management process and throughout the program maturity.
Implementing a labor management program is costly and time consuming– fact or fiction?
Fact and fiction. Implementing labor management can be both, depending on where you start and what you are trying to accomplish. BUT it does not have to break the bank!
There is a growing number of labor management programs available in the marketplace, including stand-alone systems. These systems are surprisingly low-cost, certainly so compared to the automated material handling and storage solutions. The key is not rushing through the development and implementation of a new labor management program, especially within an organization not utilizing one today.
When considering where to start on a network, it important to gain organizational buy in and quick wins by starting with an operation that is “easier” to set up the first labor management program. This program includes establishing labor standards, key performance indicators, labor productivity reports, personnel feedback structure, labor performance accountability policy, pay structure, and other change management requirements. Once implemented, it is encouraged to audit the overall success of the program before rolling out to additional facilities. An “easier” site might be one that is already using basic labor productivity metrics, low to medium volumes, and management/staffing eager to improve the labor management practices. It is also good to start with an operation that includes the warehouse functions utilized across the network. Often, the journey to implementing a new labor program starts with an operational audit to identify and develop standardized processes, as well as to decide which operation is most ready for the labor management program.
By taking the time to assess and address the operational gaps of the organization, you can maximize the full potential for on-going improvement efforts, including the future use of automation.
A new labor management system is required to make labor management improvements – Fact or fiction?
Fiction. If there is no money (or appetite) to invest in a new labor management program or system, examine how existing practices can be changed to improve labor management. This may start by observing the operation and talking with operators to discover what problems they encounter daily. Then, investigate improvements to these daily issues, increase performance feedback and conduct on-going training to support productivity improvements.
While engineered labor standards are a key component of a labor management program, units per hour or reasonable expectancy rates are also a frequent practice. Engineered standards are developed to establish task times to account for the exact/discrete work being performed (i.e., distance traveled, item weight, quantity picked, etc..). General units per hour, or reasonable expectancy rates are based on operational averages and general knowledge of operations to establish the labor rates. While not specific to the actual activity performed, these general labor rates provide insight to the level of productivity within the operation and support the identification of areas to focus on improvement efforts. For many organizations, starting with reasonable expectancies is the first step in a labor management program strategy as it allows a workforce to adjust to a more structured and standardized environment while building a performance management culture.
Next steps
As with anything new, the hardest step is often the first step. With some strategic planning, an organization can chart the course of operational excellence through a labor management program that includes a sustainable foundation, integrated systems, optimized processes, and engaged people to manage metrics, output, and organizational productivity.
In summary, a labor management program does not have to be complicated to be effective and help a business stay competitive. By examining the factors that contribute to an organization’s ability to reach their full potential, operations can increase productivity, decrease costs, and keep the bottom-line healthy.