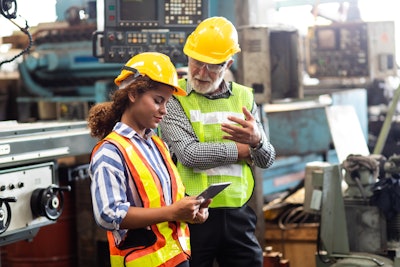
Manufacturers are well aware of the labor shortage in their industry. Deloitte and The Manufacturing Institute estimate that 2.1 million jobs could potentially be unfilled by the year 2030, potentially costing the industry $1 trillion dollars in that year alone. The ripple effect will be significant as goods become harder to obtain, labor costs and consumer prices increase, and economic uncertainties are elevated. In a recent survey of manufacturers, 90% say that turnover and labor shortages have negatively impacted production. One side effect is additional pressure being placed on employees, exacerbating the retention issue.
Manufacturers deploy several concurrent strategies
In response, manufacturers are taking a multi-pronged approach to fill staffing gaps and keep production on track, but the results have been mixed, at best. These efforts include:
- Aggressive recruitment to replace retiring manufacturing professionals along with filling ongoing staffing gaps. Yet Gen Z has been reluctant to pursue careers in the industry. Instead, they are opting for roles they deem are higher paying and in more innovative industries. What many don’t realize is that manufacturing’s digital transformation has resulted in new roles and challenging opportunities with arguably less volatility than other industries.
- Increasing training efforts: 71% of manufacturers report increasing training as part of succession planning because more experienced employees are nearing retirement. However, 41% say the knowledge transfer between experienced workers and new hires remains inadequate. Additionally, 29% of manufacturers are hiring less qualified staff and investing in training them on the go. This creates new, stable opportunities for workers that may not have considered manufacturing as a career choice. However, it can heighten safety risks on the shop floor and impact retention if training is not sufficient.
- Offering competitive wages: To attract skilled talent, 57% of manufacturers are offering higher wages though this strategy may not be sustainable long-term.
- Investing in technology: For 80% of manufacturers, digitalization is either already in operation or on its way toward being implemented, according to a recent survey by the Manufacturers Alliance Foundation in collaboration with Siemens. However, progress has been slowed by one-off, high priority pilots versus long-term systematic approaches.
Eliminating silos accelerates digitalization and closes staffing gaps
All these efforts by manufacturers show progress yet are they enough to close the significant staffing gaps within five years? The one-off pilots cited by the Manufacturers Alliance Foundation survey also reflect a larger on-going issue of manufacturers taking a silo approach to work. Addressing it could potentially unlock the talent shortage.
Think about how most work gets done today, especially in manufacturing environments that have embraced digital transformation. Teams rely on a mix of paper forms and familiar digital tools and apps that are specific to their job function and over time, those tools amass critical institutional knowledge.
On a regular basis, each team needs to roll up their progress and results in the form of reports and presentations. Eventually, there is a condensed snapshot of performance across the entire company provided to executives. Sounds like business as usual except that this approach is a hidden productivity killer.
What employees may be reluctant to call out, and managers may not be aware of, is the amount of time it takes to gather important information from those various paper forms and digital tools to create reports.
A recent productivity survey found that employees are spending 11 hours or more each week hopping from one digital tool or data source to another just to get the information they need to do their jobs. This issue is known as Gray Work, and it steals time – and productivity - that could be better spent on more impactful activities that also boosts employee satisfaction.
By replacing silos with a collaboration strategy across the workforce and the digital tools they use, manufacturers can get an accurate view into every activity happening across the company without creating gray work.
The state of automation in manufacturing
Manufacturers agree that automation can help combat labor shortages as nearly half plan to use technology for that very reason, according to a recent manufacturing survey. However, only 39% of manufacturers are currently embracing automation to close staffing gaps. On a more positive note, 49% have plans to enhance automation and technology in the coming year.
Manufacturers that can bring together the workforce on a centralized work management platform that supports automation of repetitive tasks are likely to see significant productivity gains, successful knowledge transfers, and the ability to attract and retain top talent.