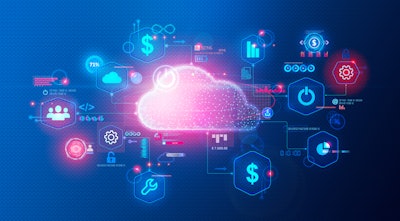
In 2021, one in five of the 2,000 largest publicly listed companies worldwide committed to a “net-zero” emissions plan by 2050 to help tackle global climate change. Collectively our planet needs to reduce annual emissions from the current 57 gigatons of CO2 to net zero, in just a few decades.
Corporations are under heavy scrutiny for their contribution to carbon emissions and the pressure is now on field service organizations to get smarter and deliver more sustainable services. The industry, often thought to be an unavoidably energy-intensive business, needs to continually improve with time—moving from the use of digital planning tools to optimize technician mileage and cut energy waste to more advanced AI that creates a unique service fingerprint for continual sustainable optimization.
The world produced a shocking 40.8 billion metric tons of greenhouse gases in 2021 alone. The U.S. accounted for almost one sixth of this total output. As the world’s second largest producer of greenhouse gas emissions, the U.S. has pledged to achieve net-zero targets no later than 2050. The Long-Term Strategy (LTS) for reaching this target states that cutting energy waste is one of the critical ways to achieve these ambitious but necessary goals for climate change.
This is how field service, by its very nature as a high mileage user, can make a difference.
Field service’s role in fighting climate change
The transportation industry is the largest contributor to U.S. emissions, so it has an important role to play in the transition to net zero. In just one year, U.S. vehicles produce 1,098 million metric tons of carbon dioxide equivalents—almost one-fifth of the nation’s total carbon dioxide emissions. Reducing drive time is a crucial way to reduce the nation’s carbon footprint.
While we see more and more service organizations adopting a remote-first approach, which will reduce the number of on-site visits necessary for field technicians to complete, companies agree that there’s no foreseeable future in which field service doesn’t include an on-site component. Where and when service visits remain necessary, optimized resource utilization and route scheduling provide an impactful way for field service organizations to tighten fuel consumption, to reduce energy waste and carbon emissions.
However, this is easier said than done. Matching team resources with fluctuating demand over multiple time horizons is a tough challenge. The task of managing customer expectations with unexpected delays and unforeseen events in real-time must often take priority over perfectly optimized resource utilization.
But AI-powered Planning, Scheduling & Optimization (PSO) technology can save field service organizations many hours of time, countless miles and hundreds of thousands of dollars, ensuring operations are as efficient and sustainable as possible without sacrificing customer experience.
AI-based technology brings new opportunities for more sustainable field service
Real-time optimization, scalability and built-in intelligence are key when it comes to workforce planning and scheduling. The AI technology embedded in an advanced PSO solution finds and fixes invisible inefficiencies that businesses cannot see. It automates the optimization of workforce planning, scheduling and routing for a more streamlined, efficient, environmentally friendly version of field service operations.
PSO automatically schedules service time slots based on resource availability and prioritizes jobs depending on the level of urgency so that the most pressing and time sensitive jobs can be scheduled as soon as possible, without interfering with pre-existing jobs. This means the right resources are available at the right time for the right job without the risk of double-booking or the need for technicians to make multiple trips.
When there are sudden changes in either demand and urgent request or resource availability for instance, due to illness, PSO can immediately absorb incoming workload imbalances by automating capacity and the movement of resources, minimizing the number of trips a technician must make, and maximizing operational efficiency in real-time.
Dynamic route optimization: cut drive time and delays to service
The dynamic route optimization function of PSO technology assigns jobs to technicians that will optimize drive time by taking the most efficient route. It achieves this by using AI to calculate time needed to complete each task based on existing data for each technician, so that an appropriate timeframe is given to jobs that are more complex or have a larger scale, to guarantee there is enough time for completion and to prevent overruns. Routing is also optimized based on geographic parameters, such as operating in an urban versus rural catchment area and assigns jobs that are as close together as resource availability will allow. This ensures the order of jobs is not only time optimized, but route optimized so that each field technician travels the minimum amount of distance necessary.
The numbers don’t lie
Businesses can reduce average technician travel time by up to 35%-50% when implementing an advanced PSO solution. One example is CoolSys, a U.S.-based HVAC/R services parent company who was able to reduce average technician travel time by 35% with the use of IFS PSO.
As you can imagine, the reduction in travel time and mileage has a significant environmental impact. Take, for example, a field service organization with a workforce of 1,000 technicians that complete a total of 780,000 jobs a year, covering approx. 14 million miles. With medium-sized trucks averaging 8 miles/gallon and every gallon of gasoline releasing 22 pounds of CO2 emissions into the atmosphere, the typical field service business can produce up to 38,500,000 pounds of CO2 every year. After deploying PSO and cutting travel time by 35% to a total of 9.1 million miles, annual carbon emissions can be reduced by 65% to just 13,475,000 pounds per year.
Along with these important emissions reductions come significant business cost savings. For instance, if fuel prices average $5 per gallon, a 35% reduction in travel time from planning and scheduling optimization could provide a fuel cost saving in this example of $3,087,000 per year.
Optimized scheduling gets better with time
The cost-saving and eco benefits of PSO only get better over time thanks to its AI and machine learning capabilities. The machine learning within the optimization engine continually improves the accuracy of job durations by self-learning how long each technician takes to perform various activities and creating a fingerprint for each field service engineer and enabling the system to match the best engineer to each specific job. This means PSO becomes completely tailored to each business’ specific operations, providing a truly customized optimization system that offers an increasingly greater ROI over time.
PSO perfects field service optimization enabling organizations to achieve significant cost-savings while reducing their carbon footprint and maintaining first-rate customer experience. When it comes to sustainability, it’s harder to find a more tangible application of AI for a field service organization that’s not just forward-looking with growth but committed to contributing positively to more sustainable operations.