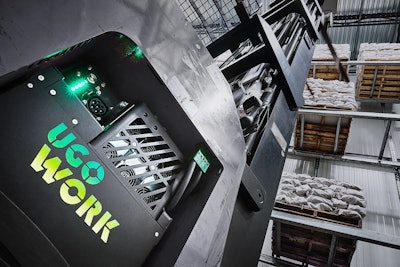
This content was sponsored by UgoWork.
As nations around the globe adopt stricter emissions and fuel economy targets in order to achieve the Paris Agreement’s ultimate goal of limiting global warming to well below 2, and preferably to 1.5 degrees Celsius, consumer demand for electric vehicles (EVs) has surged. People’s elevated environmental awareness, gas prices and generous government grants are behind the surge. According to Deloitte, there will be at least 400 million EVs on the road by 2040.
Inevitably, rising demand for EVs begets rising demand for EV batteries. As per a recent report, entitled Electric Vehicle Battery Market, 2021-2028, the EV battery market will reach US$154.90 billion by 2028.
Interestingly enough, while there is a lot of hype surrounding the electrification of consumer EVs, industrial EVs, also known as forklifts, are starting to emerge as another way to curb greenhouse gas emissions and help companies achieve their environmental, social and governance (ESG) objectives.
The market is definitely changing. Based on data from the Industrial Truck Association, electric forklifts now make up 64% of the total North American market. Material handling teams across all industries are accelerating the adoption of electric forklifts thanks to improved performance, longer run times, ease of use, and minimal maintenance. But where do all of these benefits come from?
The evolution of EV battery technologies
In the past, lead-acid batteries were the first option for the electrification of forklifts. However, they require at least eight hours to charge and another eight to cool down before use. This means each forklift has to have several batteries on hand to operate on more than one work shift.
Lead-acid batteries also require significant maintenance and a space or room to store the batteries while they are charging. What’s more, the charging process comprises health and safety risks since it involves handling of heavy loads and potentially generates toxic fumes and leaks; staff must be trained and act diligently when performing charging related duties.
However, lithium-ion batteries, which are overtaking lead-acid batteries to power forklifts in intense applications, present none of these challenges. Compared to legacy lead-acid technology, lithium-ion batteries are more energy-efficient, so they require less energy and emit less CO2 (up to 41% less), charge faster (typically 5 times faster), require no maintenance, last longer (up to 5 times longer) and are safe for operators since no battery swap is needed and they don't emit toxic fumes.
With lithium-ion batteries, you can reclaim valuable real estate on your production floor. With their simple plug-and-charge infrastructure, operator efficiency and safety are higher.
Nevertheless, although lithium-ion battery-powered forklifts are gaining huge traction due to all these advantages, there are still misconceptions as to the sourcing and sustainability of lithium-ion batteries.
Debunking sourcing and sustainability myths surrounding lithium-ion batteries
Myth #1: Lithium shortages
Lithium-ion batteries composition may vary; most common chemistries found in material handling applications are Lithium Nickel Manganese Cobalt Oxide (LiNiMnCoO2 or NMC) and Lithium Iron Phosphate (LiFePO4 or LFP). Fearmongering news headlines, as well as marketing from the oil industry and vendors of competing technologies, point to a looming shortage in lithium.
There is no lithium shortage per se. The US Geological Survey estimates that total lithium resources around the world are about 80 million tons, with new sources being regularly found in non-traditional lithium locations, as opposed to Argentina, Chile, Bolivia, China and Australia, which make up almost all of the world’s lithium supply.
The issues surrounding lithium supply are more about where the metal is sourced as well as the need for political and economic support to developing it in Western nations for easier access.
Myth #2: Lithium extraction will never be sustainable
Conventional lithium mining operations are detrimental to the environment. According to the Global Battery Alliance:
“The production of a rechargeable battery – from mine to electric vehicle – poses significant social and environmental risks. These range from mineral extraction (child labor, unsafe working conditions, indigenous rights), to production processes (C02 footprint, water use, biodiversity loss, pollution) and significantly impact the overall sustainability of the end product.”
It is important to note, however, that government regulations and new innovations to eliminate unsustainable lithium mining practices are underway.
For example, major agreements between more sustainable mining companies and battery makers are being heralded as a major step in the right direction.
Battery makers, including UgoWork, are also heavily investing in research and development to design new batteries that optimize the use of lithium and minimize the carbon footprint of the battery over its entire lifecycle. UgoWork's modular design monitors the state of health of the lithium pack and facilitates swapping when capacity doesn't meet the requirement of the application anymore. By doing so, the useful life of the other components (steel, electronics) is maximized and the extracted lithium pack can be assigned to less demanding applications or even fully recycled. More on that in Myth #3…
Myth #3: Lithium-ion batteries end up in landfills
Contrary to popular belief, lithium-ion batteries for forklifts (and cars for that matter!) do not end up in landfills. When lithium-ion batteries do end up reaching the end of their first useful life, two approaches can be taken. They can be revalorized for other applications that may need reduced levels of performance, like emergency power backups, surveillance systems, solar power storage, mobility equipment, etc.
An alternative approach is to recycle all the metals and other materials found in lithium-ion batteries. Companies like Lithion Recycling and Li-Cycle are making massive advances in recycling up to 95% of lithium-ion battery components with processes that produce very low GHG emissions. UgoWork recently announced a North American partnership with Lithion Recycling to recycle all of its forklift batteries.
It is these types of initiatives that are paving the way to a robust lithium-ion recycling infrastructure—and a complete circular economy in the EV battery sector.
The EV battery passport: Proving the role of lithium-ion batteries in global decarbonization
More and more countries are implementing policies that require manufacturers to develop products that contain a percentage of recycled material.
A case in point? The European Union’s circular standards for consumer products as well as high-impact products, including lithium-ion batteries. These rules purport that products must be recyclable, can be revalorized, and contain recycled materials if manufacturers want to sell them in the EU. Similar legislation is bound to come to North America.
Even national governments and investors are asking that manufacturers clearly demonstrate the ESG compliance of their products in order to receive grants and investments.
But how can a battery manufacturer prove such levels of compliance? Enter the Battery Passport.
Developed by the Global Battery Alliance, a public-private collaboration platform, the Battery Passport is promising to be yet another solution to ensure the sustainability of lithium-ion batteries.
The Battery Passport is a digital representation of an EV battery that provides comprehensive information about its lifecycle, from mine to vehicle and beyond. This means, at any given moment in the value chain, stakeholders and auditors can obtain real-time information and end-to-end traceability of how the battery was made, where the metals and materials came from, performance levels, maintenance work, and more. The Battery Passport aims to provide complete ESG transparency so that companies can meet their ESG goals, even at the battery level.
While tracing a lithium-ion battery’s history with the Battery Passport will be somewhat simple for its first lifespan (from the mining to the cell and packing and all the way to its industrial application in powering forklifts), lithium-ion battery manufacturers, such as UgoWork, are collaborating with recycling experts, like Lithion Recycling, and the developers of traceability platforms to add critical data to the Battery Passport when batteries are either revalorized or undergo urban mining.
Lithium-ion batteries are indeed a proven technology to power forklifts and boost the performance of material handling teams. The exciting new frontier is now making these batteries at the heart of a completely circular economy.
Interested in learning more about UgoWork's industrial lithium-ion batteries and how they are part of an emerging circular economy? Watch this interview with Supply & Demand Chain Executive live from MODEX 2022 below or contact UgoWork today.