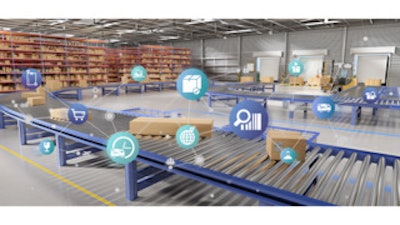
After almost two years of wave upon wave of disruption, the overarching message for supply chain professionals is loud and clear -- the global supply chain operates as a connected ecosystem, and too many of its stakeholders take all the pieces of that system for granted when they’re working well.
While the pre-2020 era certainly had disruptions, they tended to be finite — a dock workers strike, a geographic event like an earthquake, specific market-based commodity constraints or regional costing differences. Today’s challenges are different, with a wide swath of continual disruption broadly falling into three categories:
- Coronavirus disease (COVID-19) pandemic disruptions (for example, factory and logistics operations shutdowns)
- Labor disruption (displaced labor, not enough labor and/or not the right skilled labor)
- The demand equation (at a time in which it is almost impossible to create an accurate 12- to 24-month forecast)
All three add up to a cascading set of events coupled with significant economic growth as countries pump money into their economies to drive rejuvenation, thereby driving demand that the now-disrupted supply chain has not been prepared to meet. Unlike finite events, this cascade hasn’t given the supply chain the breathing room needed to heal itself, instead creating a fundamental imbalance in every area.
In summary, the supply chain of the past, and for that matter, the present, is not the supply chain of the future. Companies must invest in the capability to manage every part of their supply chains throughout disruption. They must build a resilient supply chain.
In the context of the supply chain, “resilience” is a business’s ability to navigate ever-changing supply chain disruptions with its existing capabilities. Resilience is a company’s capacity to react to problems and recover from them without significant impact to operations and customer timelines — to retain the ability to meet customer demand no matter what.
Supply chain resilience — where to start
Supply chain executives will be best served by considering a reboot of their resilience strategy, one that accounts for the vulnerabilities exposed by the past two years of cascading disruptions. Paramount to the success of this strategy will be the ability to meet the needs of the now, with the understanding that those needs can change overnight. While this is a challenge, as with so many challenges in business and in life, it brings with it opportunity.
First, really go back to basics: product design. Cascading disruptions have emphasized the need for engineers to spend time qualifying or requalifying parts and suppliers, evaluating current and future market availability of needed parts and redesigning products to remove legacy parts. Keep an eye on which parts gain legacy status and ensure they're not included in new product designs.
Acknowledge that it will be difficult to keep product designs stable throughout the next 10-15 years. Suppliers will most likely discontinue parts — or at least make fewer of them — so products should be designed with some flexibility to incorporate the different parts that will be readily available in the future. For legacy — but still popular — products, be prepared to redesign to keep pace with the components market. An unexpected redesign process can set both product and company back considerably.
Second, now that history (macroeconomic and market conditions, cyclical markets, etc.) cannot reliably be used to project the future, consider a shift to demand planning. The ongoing unstable environment makes demand forecasting increasingly difficult. Even now, no one can predict what the world will look like in 10 months and how it will affect various markets. In response, many companies are increasing their investments in analytics and visibility — the ability to keep an eye on the full range of the supply chain, from the factories down to the Tier 3 suppliers, in as close to real time as possible.
And finally, develop a business continuity plan that plans on disruptions, even when you don’t know precisely what those disruptions will entail. The list of potential supply disruptions — from climate disasters to geopolitical conflicts to, yes, pandemic — is lengthy. The last one has always been a possibility, but no one in the supply chain world was prepared to handle it. Now we know better, and ramping up a business continuity plan is key to developing supply chain resilience.
The top goals of any company’s supply chain resilience program should be to gain the ability to recover quickly without impacting customer delivery timelines, maintain multiple sourcing options and develop high levels of supply chain agility to increase or decrease production. Creating a continuity plan supports these goals.
Launching the New Year with a supply chain resilience strategy will help keep business moving forward throughout disruption; protect production capacity while maintaining a technology edge; and most importantly, maintain the ability to meet customers' rapidly changing needs at the high standards set in less disruptive times.