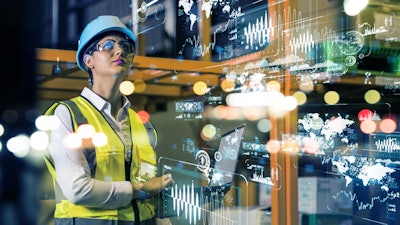
The most recent NHTSA Electronic Tire Identification Study recognizes that in order to improve efficiency, the automotive industry needs better methods for identifying tires. One common solution is the use of RFID tags in tires that can easily be read by technicians and mechanics, ultimately improving precision in gathering this information.
RFID chips offer some benefits to supply chain managers and technicians, certainly. With the right device, workers can read tire data from the chip and connect this with their internal systems. However, complete dependence on RFID chips for tire management actually comes with a number of downsides.
Downsides of complete dependence on RFID
In order to read the RFID chips and have complete tire traceability, every partner organization in the supply chain that handles the tires must purchase specialized, and often costly, scanners that support the technology. As mechanics who have worked with them can confirm, other significant issues that come with RFID-enabled tires include:
● When tires are stacked on top of each other, it’s very difficult to identify the correct tire, as you will often get a reading from the wrong tire’s RFID.
● RFID tags currently in use have limited memory and generally do not carry the tire DOT/TIN in them.
● Additionally, RFID chips are not standard across all manufacturers, leaving a significant number of ‘analog’ tires in circulation.
For the foreseeable future, shipments of older tires will have chipped and unchipped tires together, meaning that workers will have to identify them manually, leading to errors and increased labor costs.
Mobile data capture simplifies tire sidewall scanning
Mobile data capture uses optical recognition (OCR) technology to scan vehicle tire numbers in an instant with any mobile device. Optical character recognition (OCR) technology is fast and efficient at scanning codes, numbers or a series of characters. This means that workers throughout the supply chain can use any standard smart device to scan the tire DOT code and transfer them directly into their system or database, ensuring that all the data captured is accurate and up-to-date.
For tire retailers, OCR technology allows technicians to scan each tire as it arrives and register it into their internal database to keep track of each tire’s manufacturing date, based on type. This makes it simple for mechanics to search for and pull the tire that has been sitting in inventory the longest, putting it on a vehicle instead of a newer one to ensure first-in-first-out (FIFO) inventory standards are followed.
With this process, each tire can also be automatically checked against the NHTSA recall database, a process that is typically five times faster and far more accurate than entering it manually. This creates an error-proof and complete database of every sold or installed tire. The mobile scanning process not only saves time but also reduces the risk of human error, eliminating the need to write each code using pen and paper or manually enter the code into a mobile device. Also with mobile data capture, tire technicians can scan tires even when offline and in adverse conditions, eliminating the risk of being unable to access the system.
The gains in efficiency and speed are proven
All in all, mobile data capture serves as a better method for identifying tires, resulting in better labor management and a comprehensive logging of tires based on manufacture date. It is critical for the industry to move away from costly technologies and dated methods of inventory keeping, like manual entry and RFID chips. A more modern approach, such as mobile data capture, is more accurate, more cost-effective and less time-consuming.