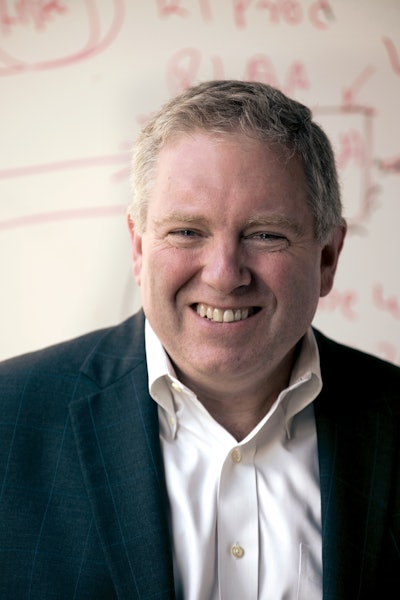
“The world hates change, yet it is the only thing that has brought progress,” said Charles Kettering, American inventor. Today, disruptive technologies are reshaping almost every industry and redefining not just what is possible, but what may soon become the new norm. Even more amazing is the rapid pace of change. Last year, did you imagine that we would be sharing the road with driverless cars? Although change is traditionally slow in supply chain solutions, the rate is picking up as algorithms and automation start to fundamentally alter what is possible in managing and synchronizing supply and demand.
One reason why Kettering’s quote rings true is that opportunities for progress often first appear as challenges. This is definitely the case in supply chain. Rising complexity and headcount pressures triggered a natural response to squeeze more from less, leaving staff struggling to perform. Existing processes and systems are overwhelmed. The data landscape exploded. Teams now face dozens of demand signals from thousands of retailer locations instead of only shipments and orders from internal distribution centers; daily granularity instead of monthly or weekly; and even new types of data like weather forecasts, housing starts and unstructured data from social media. While traditional planning systems are ill-equipped to deal with big data, modern technology is.
A new class of software is emerging that combines automation and algorithms to unlock the value of big data, and transform supply chain from a cost center to a driver of financial performance. Not surprisingly, automated analytics is top of mind with senior leadership looking for change. A recent survey from The Consumer Goods Forum and KPMG found that more than half of supply chain executives ranked data analytics as “very or critically important” to their strategy this year and, according to IDC Manufacturing Insights, “big data analytics will remain one of the top investment priorities for manufacturing organizations of all sizes for the foreseeable future.”
Algorithms in Supply Chain
The market is buzzing with talk about algorithms. Why now? Supply chains are too complex for spreadsheets and overwhelmed the simplistic math used in traditional planning systems. Remember, these systems were designed in the 1980s when markets were far simpler, and both computing power and data resources were limited. The mathematical techniques applied to planning were the best available then, but times are changing. Following Moore’s Law, computing power grew roughly 16,000 times since 1985; data volume increased even more. Filling the gap are new systems like demand sensing that use advanced pattern recognition algorithms to sort through masses of real-time data, understand what is predictive and create the best picture of demand for every item at every location. It is the way you would imagine demand planning to work if it were invented today instead of 50 years ago.
The use of real-time data is a fundamental departure from the traditional approach of modeling demand on shipments from last year at this time. When you decide how much milk to buy for your family, do you check historical shopping lists to see how much milk you bought this week last year or open the fridge to look how much is there? Understanding your customer’s inventory provides a better outcome and, in this case, a happier family. Algorithms designed to look at current data can peek inside the fridge, and simultaneously examine hundreds of other signals to find predictive patterns in and between datasets. These datasets reflect market realities from events that history cannot anticipate, but are crucial to financial performance, such as promotional activities, consumer acceptance of product introductions, unseasonal weather shifts and impacts from competitor programs. It is not that machines are smarter than humans, but that algorithms are very efficient at mathematically complex number-crunching.
Role of Automation
Statisticians could do this, too, if you had an army of them and all the time in the world. However, most companies are shrinking planning departments and headcount pressures make it impossible to hire an army of statisticians. Meanwhile, escalating stock-keeping unit (SKU) proliferation means more items to manage. In consumer goods, roughly 40 percent of items for sale are new each year. For many planners, workload doubled in recent years.
Even if you could hire a planner for every item, there is not enough time in the day to manually perform all the complex calculations required to extract value from the flood of data from important customers like Walmart. To realize the strategic benefits of an agile and demand-driven supply chain, forecasts need to be created each day, every day. Anything less falls short of the mark. The answer to these challenges is automation.
Automation is starting to open new frontiers in supply chain, just as it did in industries like finance, retail and advertising. In traditional demand planning, roughly three-quarters of tasks are manual, such as data entry, fitting models to history and interpreting point-of-sale (POS) data. This is a terrible use of planners’ time. There is no reason that, in today’s world, planners should have to manually tune statistical models and reconcile forecasts. Rather, they should be focused on strategic areas in which data is not available to the system, like planning the next promotion or product launch.
In contrast, demand sensing is mostly automated, with manual activities all but eliminated. This lets planners plan and it pays. Findings from Terra Technology’s Forecasting Benchmark Study show that planners with lighter workloads consistently create more forecast value-added. In addition to productivity, companies are finding that few planners wish to be statisticians. Reducing the level of data analysis in job responsibilities improves both employee satisfaction and retention, and is an important step to creating attractive career paths within planning departments.
As in other industries, don’t look for change to come from the large established players with a vested interest in preserving the status quo. Value stemming from new technology tends to be driven by small, nimble companies with a passion and vision for change. According to Lora Cecere, founder of Supply Chain Insights, “The greatest improvement in inventory and overall value in supply chains continues to come from best-in-breed solutions. While the large system integrators will push offerings from enterprise resource planning (ERP) expansionists, I see greater value coming to clients that bypass hype and focus on business results through the implementation of best-of-breed products on the top of ERP backbones.”