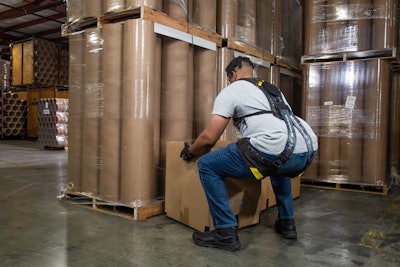
There is a big shift happening in the way work is being done in the food distribution industry, and it sounds like it’s straight out of a sci-fi movie: workers are picking orders while wearing exoskeletons. But these are not the huge, motorized devices from the Hollywood films. Over the last few years, new companies and innovative technologies have emerged that are building practical, proven devices designed to be worn all day by workers around the world.
These assistive devices, known as exosuits, are slimmer, more comfortable, and textile-based for more flexibility. This growth in exosuit (exo) utilization is being driven by a growing body of evidence of the effectiveness of exos on workers’ health and companies’ bottom lines. Organizations that are implementing this technology are seeing significant cost savings, and as a result, are rapidly rolling out the technology across their networks.
The philosophy behind exo technology is simple: Workers put on a lightweight wearable device that takes the strain— up to 100 pounds —off their back muscles every time they bend over to lift an object. That means every lift is a little easier and workers not only feel less fatigue, but the load on their back muscles is significantly decreased (20-40%), which decreases the cumulative stress on their tissues.
The impact of exos on companies’ bottom lines is significant because they impact the three biggest drivers of labor costs for most warehouses: Exos now have solid data demonstrating the ability to decrease injury rates, boost productivity, and improve retention rates.
How exos reduce strain and decrease injuries
While ergonomics and personal protective equipment (PPE) have been generally successful in reducing some musculoskeletal disorder (MSD) injury risks in the workplace, back injuries—the No. 1 MSD for material handling jobs—have remained high. For most warehouses with case-picking operations, the ability to decrease pick rates or decrease bend angles is not achievable without major operational changes.
Rather than try to completely restructure the warehouse, many companies are turning to exosuits as a method to reduce injury risk. Soft exos have elastic bands that work by effectively providing artificial back muscles that reduce some of the strain going through the low backs of the workers. As a result, there is less microdamage to the tissue, which means workers go home at the end of the day less sore and able to recover at home before their next shift.
One study of four DCs looked at the ability of exos to drive down injuries over more than a year of use. Historically, these DCs had, on average, one back injury per 27,000 hours worked. In the study, there were zero back strain injuries after more than 281,000 hours worked (that’s equivalent to 140 workers picking full-time for a year). With the average cost of a back strain injury at over $67,000 (according to OSHA), that reduction in injuries can lead to significant savings.
Decreased fatigue leads to improved productivity
Manual material handling is a tough job. Workers will tell you that when they get home after an 8- or 10-hour shift, they collapse on the couch, and their back is sore on most days. Due to the nature of the continuous lifting on the job, operations managers see a decrease in productivity over the last few hours of a shift. The limiter of productivity for these warehouse jobs is often what the human body can handle day in and day out.
It’s been known for several years now that workers report their jobs take 20% less physical effort when using an exosuit (based on worker surveys using a perceived exertion scale). Until recently, it wasn’t clear if this decrease in fatigue lead would lead to changes in pick rates. To answer that question, another set of recent studies looked at worker productivity before and after the introduction of exos. The results are clear: workers using exos are picking more while reporting that work feels easier.
These studies have shown 5-15% boosts in productivity across multiple companies and multiple use cases. Some of these studies have followed productivity rates for over a year, and the productivity gains have not only been maintained but are also achieved at multiple locations within a distribution network.
When workers are happier, retention improves
Worker turnover is one of the largest issues in distribution with the current tight labor market. Recruitment and retraining are extremely expensive. While the reasons behind worker turnover are a complicated topic, it is clear that more physically demanding jobs tend to have a higher turnover rate. So, it has been hypothesized that if worker fatigue was reduced, that turnover might also drop.
While more work needs to be done to further validate if exos can be expected to reduce turnover for most companies, it is not a large leap to anticipate that if workers are healthier and feeling better, they would be less likely to search for alternative employment.
Calculating ROI of safety technology
At the end of the day, any program or safety initiative requires a financial investment. But it is an investment in your workers' lives to ensure that they not only enjoy working, but can also go home to their kids at the end of the day with more energy.
On top of keeping workers safe, the return on investment of an exo program can be significant. Combining decreased strains and sprains, productivity increases, and increased employee retention can easily demonstrate a 10 times or greater ROI in less than 3 years, with many companies forecasting a payback period of just a few months. Companies can calculate their ROI from an exo deployment with online tools that assess these challenges against the number of employees, operating costs, and wages. At the end of the day, clear ROI and productivity data is driving the rise of the use of exos in the warehouse.