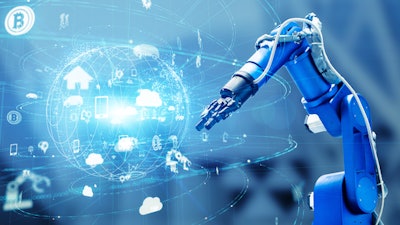
Automation is a key contributor for food production, from sorting and processing to packaging goods. While traditional machinery allows for extremely high-speed handling of workpieces, flexibility is often a limitation. Fast adaption to wider ranges of existing or new food products present challenges. Robots and other means of employing flexible automation are continually on the rise, providing solutions to suppliers in the food industry looking to increase their efficiency in areas of their varying production needs.
Robots are a natural fit for production lines where goods to be handled are constantly changing or even just where the processes vary. For example, products could be loaded into boxes in one quantity and later loaded into differing boxes of another quantity or differing spacing. By design, robots are intended to be flexible. Programs that control their motion paths can be quickly updated along with end-of-arm tools (EOATs) easily changed to adapt to the next task.
There has been a surge in new gains involving both the robots themselves and peripheral components that enable users to deploy and re-deploy even more effectively. Advances have sprung from a multitude of automation industry entities, including businesses, education and R&D sources collaborating on improved mechanics, sensing and vision technology and software. As always, industrial robots are evolving, becoming stronger and faster while at the same time, lighter and more compact. Programming is becoming simpler and more intuitive for new users to learn quickly. Even more exciting to see is that communities of component and software companies are forming together around robot platforms, hastening the growth in robotic handling capabilities.
Mechanics leap forward
New mechanical breakthroughs in robotic handling solutions are boosting productivity for food suppliers. Two recent examples are soft gripping technology and Van der Waal force grippers, also known as gecko grippers.
Soft grippers compliment traditional mechanical solutions providing compliant “fingers” that envelop food products to capture them effectively without deforming or damaging them. Soft gripping solutions are becoming widely available to simple digital open/closed operations to complex dynamic servo control of gripper-finger opening/closing positions and applied forces.
Van der Waal grippers consist of tiny hair-like filaments resembling a gecko lizard’s hands, and compliment traditional vacuum technology approaches. They are ideal for handling wrapped foods, boxes and labels. But, unlike with using vacuum cups, holes or other interruptions in the gripping surface are less prone to negatively affect handling reliability.
In addition to new innovations such as these, there is a growing industry standardization of mechanical products making it easier and faster for engineers to design custom EOATs using of-the-shelf components. Standard equipment for quick-change, tool compliance and gripping tasks, plus modular mounting components and solutions for routing pneumatic tubing and cabling are ready to go. Complete custom EOATs that previously required weeks to concept and construct can now be accomplished in days or even hours.
Sensing and vision technology integration into standard products
Sensors and cameras have long played a critical role in successful robotic handling of foods. Unlike with rigid workpieces, such as automotive engine and transmission parts, food products are even more commonly presented in chaotic unstructured ways to robots. Industry experts answer the challenges with their experience and knowledge using sensing to identify position and orientation of workpieces, bringing organization from chaos. But, just as with robots and mechanical systems, sensing advances are accelerating encouraging practical applications more quickly than ever. Further, advanced sensing and vision technologies are being directly integrated into robots and complementary mechanical components. For example, force/torque sensors are integrated into some robot arms enabling them to function safely close to human co-workers. They are also seen integrated into mechanical grippers allowing for handling of sensitive workpieces. A third example are standard EOAT packages with gripping and vision solutions pre-engineered to function as a single entity.
Software tying everything together
With many advances happening with motion systems and their supporting components, software is pushing progress even more. Robot EOAT components are developed with standard plug-in software making them easy to integrate with common robot control systems. Companies with specialized experience with certain types of EOATs like gripping, material removal, measuring etc. incorporate advanced features into their plug-in software helping programmers more quickly accomplish common tasks. There are even third-party software platforms that enable different brands of robots and supporting components to operate together seamlessly.
The overall progress means that machinery developers are empowered to bring improved results to their customers sooner. More obstacles to deploying new flexible automation are overcome using standard products and solutions that already exist. Mechanical and control engineers alike do not have to “reinvent the wheel” on every project, continually solving routine challenges. Instead robots and their peripherals, and software bring value and experience ahead of time, saving project time and costs.