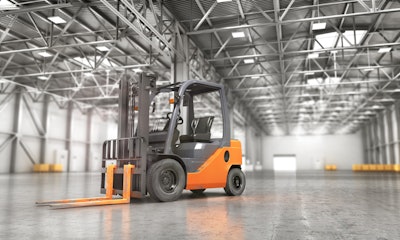
Forklift batteries are a significant investment for warehouse and factory operators, keeping goods and materials within the facility moving. Decisions such as whether to stick with lead batteries or switch to lithium batteries are among the most important motive power professionals will make in the new year.
To better understand the opportunities and challenges influencing motive power decision-makers in 2024, here are the Top 4 forklift battery trends in 2024.
1. Lead is the most prevalent chemistry in forklifts today, but lithium is quickly growing.
Lead batteries are the workhorses of the industrial supply chain, so their dominance in the forklift space is unsurprising. Today, more than nine in 10 motive power managers rely mainly on this proven technology. Survey respondents are splitting their fleet 70% lead and 30% lithium, and only 2% said their fleet runs more on lithium than lead batteries.
However, as lithium becomes more accessible over the next few years, this battery chemistry is expected to steadily gain fleet share. While no motive power managers said their fleet is split evenly between lead and lithium batteries today, 40% said they’ll reach 50/50 within the next five years.
2. In the battle of cost vs. uptime, cost still wins.
Motive power managers associate each of the two leading forklift battery chemistries with a major benefit. When asked which word(s) best summarize their perceptions of lead and lithium, 53% said “low cost” was their top term for lead, while 81% said “longevity” was their top term for lithium.
Those opinions influence the buying decision: 83% of those planning to buy a lead battery in the near term said the chemistry’s cost is a significant plus, while 49% planning to buy a lithium battery in the near term said the chemistry’s improved uptime is a significant plus.
But even though 52% said performance is an important factor when deciding between lead and lithium, cost is still king. Cost will be a major consideration for 63% of motive power managers, and it’s the reason nearly two-thirds said they’ll hold off purchasing a lithium battery.
3. Lead battery life is still good, though occasional maintenance is still a consideration.
If well-maintained, lead batteries can last more than five years for most forklift fleets. Almost 50% of motive power managers said they’re meeting that benchmark, while another 46% said their batteries last 3-5 years. Still, the amount of money respondents spend on forklift battery maintenance varies greatly. Just more than a third said they invest $251-$500 each year per battery, while 29% said they invest more than $1,000 per battery.
Perhaps not surprisingly, respondents most frequently cited maintenance as a top concern when purchasing a lead battery, with 33% mentioning it. Battery life was cited to a lesser extent at 24%.
4. Lithium steals the sustainability headlines, but lead has been a longtime success story.
Because of their role in the electric car boom, lithium batteries are often associated with clean energy efforts. But the United States has a robust supply chain for recycling and reusing lead batteries, and motive power managers are aware of its impacts. Nearly 90% said lead has a more reliable domestic supply chain than lithium, highlighting the known current sustainability tradeoff between the two chemistries.
And when recycling practices to recapture raw materials are put to the test, lead has an advantage over lithium. More than half graded lead manufacturers’ efforts as an A in recognition of the industry’s nearly 100% recycling rate. Lithium recycling is still a nascent industry with a recycling rate under 5%.
Need help determining the right battery solution for your operation?
A power study can help organizations determine the right motive power battery and charger solutions for their forklift fleet.
The first step is measure. Real fleet data, including peak and average energy usage, charge time optimization, and other data for system design, is used to create an in-depth energy profile of your fleet.
The second step is model. Performance modeling simulates the impact on operational and financial performance and determines the best solution for your environment.