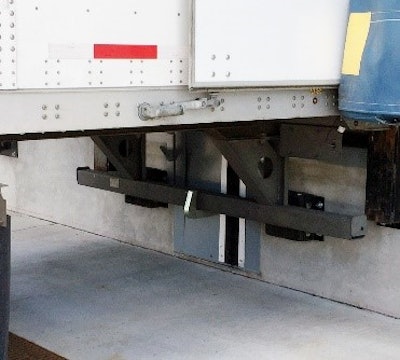
You’ve made the wise decision to install vehicle restraints at your loading docks, but it turns out, that was the easy part. How do you decide which restraint is right for your docks? You should discuss it with the distributor or contractor you’re working with, but it’s always good to educate yourself before you have that conversation. After all, two heads are better than one.
Most of the trucks and trailers warehouses and distribution centers receive at their loading docks have a rear impact guard (RIG), sometimes called an ICC bar or underride guard. RIG-based vehicle restraints keep a truck or trailer at the dock by capturing its RIG. RIG-based restraint types include trailer-positioned rotating hook, non-impact vertical barrier and non-impact active engagement. Here’s some examples:
Trailer-positioned rotating hook. These versatile restraints are typically mounted to the face of the dock and are automatically moved into the correct position when a trailer backs up against the dock bumpers. A steel hook then rotates up out of the housing and wraps around the RIG, preventing the trailer from leaving the dock. This type of restraint is often interlocked with other dock equipment to ensure a trailer is captured by the restraint before the leveler can be deployed.
Non-impact vertical barrier. Mounted to the dock wall or the drive approach, this type of restraint features a barrier device that rests on or close to the ground and raises up to engage a trailer’s RIG. Push-button versions can often be interlocked to other dock equipment to ensure a trailer is captured by the restraint before the leveler can be deployed. Some manually activated versions that feature automatic light communication systems can also be interlocked with other dock equipment.
Non-impact active engagement. This type of restraint holds a trailer against the dock, usually via hydraulic pressure on the RIG. This does not allow the truck or trailer to move away from the dock at all, whereas other types of restraints hold the RIG within a zone of about three to six inches depending on how close the RIG is to the dock wall. Sometimes active engagement is desired if there is an incline drive and trailers naturally want to roll away from the dock. Sometimes there may only be six inches of leveler lip purchase in the back of a trailer and if the trailer can move three to six inches away from the dock, the leveler lip could fall out of the trailer. Most non-impact active engagement restraints are under-leveler restraints, which means they are stored inside the building under the leveler until a truck or trailer backs up to the bumpers. A vertical barrier then emerges from the dock wall to capture the RIG. This means trucks and trailers without a RIG can also use a dock with this type of restraint, making it the most versatile of the three.
So, how do you choose which type of restraint is best for your docks? Here are three major factors to consider.
External dock environment
When choosing an RIG-based restraint, the conditions of the dock wall and drive approach should influence your decision.
Trailer-positioned rotating hook:
· These restraints are ideally mounted to the dock wall, but must be anchored in at least 8 inches of solid concrete to withstand the appropriate amount of pull-away force. A brick or hollow block wall is not strong enough to hold a truck trying to leave the dock early, so a steel bracket must be anchored to the pit floor and drive approach and then welded to the curb angle. A rotating hook restraint is then welded to the bracket. This is an acceptable method of installing a rotating hook restraint on a non-concrete dock wall but there are likely to be additional costs in time, labor, and materials.
· Rotating hooks have the benefit of storing higher off the ground than other types of restraints, which helps protect them from situations such as flooding, heavy snows and debris piling.
Non-impact vertical barrier:
· This type of restraint is mounted to the dock wall or the drive depending on the brand and model of restraint. Proper installation requires at least eight inches of solid concrete, so if the dock wall is not solid concrete but the drive is, a ground-mounted vertical barrier is a viable option.
· These restraints rest on or near the ground and are generally more susceptible to flooding, heavy snow or debris piling.
Non-impact active engagement:
· These restraints typically require significant concrete work when installed in existing docks, or they are installed with levelers in a new construction project.
· They are usually stored in the pit under the leveler, making it easy to remove snow and debris from the drive approach. External environmental factors are rarely as much of a concern for these restraints as they are for the other types.
Efficiency
Push-button restraints are always more efficient than manual ones.
· Trailer-positioned rotating hooks are usually push-button activated and easy to use and maintain.
· Non-impact vertical barriers include a variety of models with manual and push-button options.
· Non-impact active engagement restraints are always push-button activated.
Cost
Restraint costs run the gamut, but generally start with manually activated vertical barriers being the least expensive and non-impact active engagement being the most expensive.
Trailer-positioned rotating hook:
· These restraints generally make up the mid to high cost range, depending on added features specific to certain brands and models.
Non-impact vertical barrier:
· This type of restraint generally starts at the lowest cost range for manually activated versions and can enter the mid cost range for push-button versions with additional features specific to certain brands and models.
· These restraints include the largest percentage of manually activated models, which are most often selected for cost-saving purposes.
Non-impact active engagement:
· These restraints are usually in the mid to high cost range due to the extensive use of hydraulics.
· Installation of under-leveler versions of this type of restraint also tends to cost more than the others in retrofit applications because it requires extensive concrete work.
There are many things to consider when choosing the right vehicle restraint for your loading docks. You may even find that more than one type of restraint would be appropriate for your docks. Either way, any appropriate restraint will help make your loading docks safer.