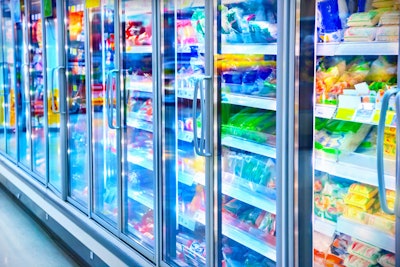
Grocery store managers must grapple with rising costs, supply chain disruptions, and complex regulatory demands. With profit margins in the grocery sector averaging just 1-2%, according to the Food Marketing Institute, managers must balance the need for affordability with the challenge of maintaining profitability—all while navigating a fiercely competitive market.
Against this backdrop, the financial impact of a refrigeration outage can result in a huge economic toll, extending beyond the immediately apparent costs of technician fees, replacement of broken parts, or the scramble to find emergency storage for perishable goods. These outages disrupt employee productivity, lead to lost sales, raise environmental and regulatory costs, and increase energy inefficiencies—all hidden expenses that can erase margins within just a few hours. To remain competitive, grocery retailers must shift from expensive and stressful reactive fixes to proactive strategies that minimize disruptions and manage the true costs of these failures.
For many, the most significant hidden cost comes from the disruption to employee productivity. When a refrigeration system goes down, it sends ripples throughout the store’s operations, diverting employees from their usual roles of engaging customers or restocking shelves to more urgent tasks, like transferring food to backup units or dealing with frustrated customers. According to the Bureau of Labor Statistics, the average hourly wage for grocery store workers in the United States is $14.96 (before considering payroll taxes, healthcare, paid time off, etc.). Each hour employees spend on these tasks is an hour lost from revenue-generating activities, pushing costs higher and chipping away at already thin margins. Over time, these disruptions wear down staff morale, increase turnover, and drive up recruitment and training costs—all expenses that could have been avoided.
Lost sales present another, often underestimated, consequence. Perishable goods account for 51% of all grocery sales (and growing), according to FMI. When refrigeration fails, the losses can be staggering. A 4-hour outage in just one display case can mean hundreds of dollars in lost sales; a full-store refrigeration outage can cause over $10,000 of lost sales. The hit to revenue is only part of the problem. Repeated outages can erode customer trust and loyalty, which are hard-earned and easily lost in an industry where shoppers have many options. McKinsey & Company has found that convenience is a top factor driving loyalty in the grocery sector, and reliable product availability is at the heart of convenience. If customers repeatedly find empty shelves or spoiled goods, they are likely to shop elsewhere—a decision that can have lasting repercussions for the store’s bottom line. An Ipsos survey revealed that nearly 1 in 4 shoppers will shop elsewhere on their next grocery trip if 1-3 items from their list are unavailable.
Meanwhile, the environmental and regulatory costs tied to refrigeration outages (especially, refrigerant leaks) are rising sharply. The average annual refrigerant leak rate in U.S. supermarkets stands around 25%, costing approximately $20,000 per store each year in replacement refrigerant alone. Leaks that go unnoticed and unresolved can result in catastrophic outages, which necessitate costly refrigerant refills and emergency repairs. The EPA’s GreenChill program has spotlighted that reducing the leak rate from the national average to their program average could save the industry over $108 million annually on replacement refrigerant alone. And with new government regulations under the AIM act poised to reduce hydrofluorocarbon (HFC) production and imports by 85% over the next 15 years, the cost of keeping refrigeration systems operational will only get higher.
Energy inefficiency represents another cost that is often overlooked but can add up quickly. Energy is the second-highest operating expense for most supermarkets, and refrigeration accounts for a significant portion of that bill. After a refrigeration outage, the quick fixes employed—like disabling energy-saving measures or cranking up the system to cool faster—can lead to months or even years of inflated utility costs if not promptly corrected. The National Renewable Energy Laboratory notes that improving refrigeration efficiency across the U.S. could significantly cut national energy consumption. At a time when sustainability is no longer just a buzzword but a priority for consumers and investors alike, grocery stores that fail to optimize their refrigeration systems are not only risking higher operational costs but also damaging their public image.
Food waste adds yet another dimension to the hidden costs of refrigeration failures. Around 30% of food in American grocery stores is discarded, and according to the USDA, the value of this wasted food is estimated to be twice the total annual profits of the sector. Every time a refrigeration outage occurs, it accelerates spoilage, leading to large-scale disposal of perishables. Beyond the direct financial hit, this waste complicates inventory management and disrupts supply chains, all while contributing to a retailer’s carbon footprint. In an era when major chains have pledged to reduce food waste as part of their corporate sustainability goals, unplanned outages create an obstacle that can derail these commitments.
What becomes clear when we consider all these hidden costs together is that the impact of a refrigeration outage extends far beyond the surface-level expenses of repair. Every incident chips away at a store’s profitability, from lost sales and increased labor costs to higher utility bills and compliance penalties. And as both customer expectations and regulatory standards continue to evolve, these hidden costs are poised to climb even higher.
The solution for grocery retailers is to shift from a reactive approach—fixing problems only when they arise—to a more proactive, preventive strategy that minimizes disruptions before they occur. Preventive maintenance, enhanced monitoring systems, and investments in newer, more efficient technologies could help stores stay ahead of these hidden costs. It’s not just about fixing what’s broken; it’s about understanding the broader implications of a seemingly small failure and planning strategically to mitigate these impacts.
As the grocery industry faces mounting pressure to reduce costs, improve sustainability, and maintain customer loyalty, understanding and addressing the true cost of refrigeration outages isn’t just a matter of sound financial management. It’s a critical strategy for staying competitive in an increasingly challenging marketplace.