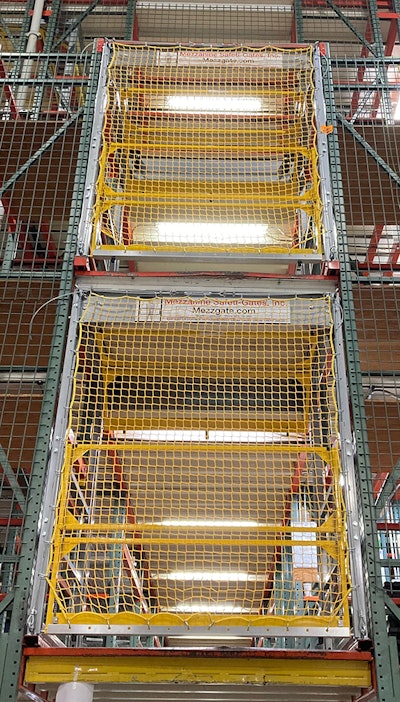
Cold storage continues to be a fast-growing sector in material handling. Demand for space in this sector has outpaced traditional warehousing real estate, and the facilities often include large rack supported pick modules to store goods, primarily food products.
In most cold storage facilities, rack supported pick modules feature pallet drop areas in the upper levels of the system. For increased efficiency and inventory tracking, automated storage retrieval systems (AS/RS) often utilize automated vehicles to load and move material to and from the pallet drop area. Employees work around these elevated drop zones, often alongside the automated vehicles, moving products to different areas within the pick modules.
Fall protection for employees working around the pallet drop areas in the pick module is mandated by OSHA’s Walking Working Surfaces regulations and ANSI standards. Pallet drop safety gates that provide a dual-gate system to ensure there is a barrier from the ledge at all times are the ideal solution for these areas.
Any mezzanine safety gate selected for fall protection in cold storage facilities must fit within the environment. From the construction to operation, these safety gates must differ from those used in traditional warehouses and storage systems. There are four things to remember when looking to secure elevated pallet drop areas in cold storage systems.
1. Save space by using rack uprights
Space is a huge issue in any storage system, and often there is minimal space to move material, let alone operate a safety gate. Because rack supported pick modules are widely used in cold storage systems, safety gate models should utilize existing rack support structures to maximize usable workspace. The ledge-side gate opens and closes flush with rear upright columns and does not extend into the lift-truck aisle, and the rear-side gate opens and closes flush with the rear upright column and does not extend into the picking aisle. These gates can be designed to secure both picking positions or empty pallet/tote return bays.
2. Ensure proper construction material
In most warehouse environments, pallet drop safety gates are constructed from powder-coated steel. However, the hostile environment of a cold storage facility often requires construction from stainless steel, which can handle freezer environments as well as temperature fluctuations or frequent rinsing.
3. Choose climate-optimized power
Increasingly, mezzanine safety gates for pick modules are being equipped with power operation. Motors should be optimized for the climate; in cold or other hostile climates, waterproof, explosion-proof and heated motors should be evaluated.
Power allows for the automated guided vehicle (AGV) or forklift truck operator to open and close the safety gate when loading or unloading material. This provides for a very ergonomic and sanitary “no touch” fall protection solution for employees working around pallets in the pick module.
4. Add additional measures for automation
Mezzanine safety gates can go beyond providing fall protection for employees in a couple of ways. First, it can provide product containment by adding safety netting or mesh panels to the safety gate system. Safety netting is often applied to the ledge gate for product containment and can also be applied to the rear gate and sides for a fully contained pallet drop area. Metal mesh panels can be installed on the sides of the gates for product containment. Both options provide fall protection for employees and products, and keep the pallet drop area a hands-free zone while being loaded and unloaded by an automated vehicle.
In addition, the pallet drop gates can be a part of the overall warehouse automation system. Facility managers can add sensors equipped with warehouse management software (WMS) to track products as they move through the safety gate in the loading and unloading process. Other technologies such as lighting systems can alert vehicles to full or empty pallet drop areas.