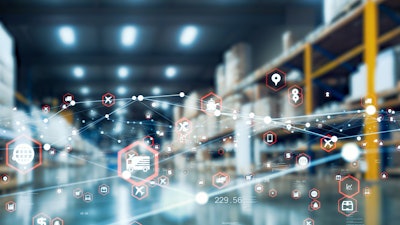
Balancing health goals with a busy schedule can be tough, and as a result, more people are turning to frozen foods as a quick and practical solution. But frozen meals have come a long way—they’re no longer just the simple TV dinners of the past. Nowadays, you can find a wide range of high-quality options, including plant-based choices, that cater to all sorts of dietary needs. In fact, between 2019-2023, U.S. frozen food sales jumped by 33%, reaching $74 billion.
So, why the surge? Changing consumer habits and the demand for convenience are key drivers. Busy families and professionals find frozen meals are a practical solution when time is tight. Innovations in cold chain technology have also improved quality and shelf life, reducing waste and making it easier to stock up without worrying about spoilage.
The increased demand has placed pressure on food manufacturers, particularly with cold chain infrastructure. Without proper cold storage, food waste and delays can cause major issues. However, here’s the good news: cold chain tech innovations are presenting new opportunities to cut costs, reduce waste, and help create a more sustainable future for frozen food.
Overcoming frozen challenges
The "cold chain" is a vital system that keeps perishable products—like seafood, dairy, frozen meals, and even pharmaceuticals—fresh and safe from farm to table. But the cold chain is facing new challenges and increased pressure to keep up.
Setting up and maintaining a cold chain network requires specialized infrastructure, and it’s not a small investment. Imagine a temperature-controlled truck hauling frozen meals across the country. Except it’s not just a refrigerated truck: it’s a high-tech, climate-controlled mobile environment that needs to be monitored around the clock. Similarly, warehouses need to be equipped with sophisticated refrigeration systems to store frozen products without risking spoilage.
Energy is another major factor driving costs. Cold storage facilities consume a lot of energy to keep products at precise temperatures, especially when dealing with frozen goods. For example, a large warehouse storing frozen pizzas might need to maintain a temperature of -10°F, which requires consistent energy usage. When energy prices fluctuate, it can create a financial headache. A spike in energy costs could mean a warehouse operator might suddenly face significantly higher utility bills, which ultimately get passed on to consumers in the form of higher prices for frozen products.
As demand for frozen foods increases, so does the need for specialized packaging to keep everything cold and intact. Think about the plastic film wrapped around frozen vegetables or the insulating foam in a frozen dinner box. These materials aren’t easy to come by, and with supply chain disruptions, manufacturers can find themselves facing shortages or price hikes. That can lead to tighter margins for businesses that are already struggling with rising infrastructure costs.
Unlike canned goods, frozen products are perishable, so any disruption in the cold chain—whether it's a faulty refrigeration unit in a warehouse or a delay in delivery—can cause spoilage. This isn’t just a financial loss for the manufacturer—it’s an environmental one, too. Food waste contributes to greenhouse gas emissions as it decomposes, and with the cold chain system being so time-sensitive, minimizing spoilage is key to cutting down on waste.
Then there’s the challenge of meeting on-time, in-full (OTIF) delivery standards, which ensure products arrive when and where they’re supposed to. If a manufacturer doesn’t meet OTIF standards, customers might not get their frozen meals on time, leading to dissatisfaction and potential loss of business.
There are also external factors beyond a manufacturer’s control that can disrupt the cold chain, such as extreme weather, labor shortages, global conflicts, and shifting trade regulations. For example, the war in Ukraine has caused material shortages and higher transportation costs, while hurricanes or labor strikes can delay shipments, forcing companies to absorb costs or risk stock shortages. Additionally, changing regulations demand flexibility—such as new certification requirements for cold storage—and often require costly adjustments to operations that add layers of complexity and cost to an already challenging system.
These many challenges show that the cold chain is more than just keeping things cold; it’s a complex, resource-intensive network that manufacturers must continuously adapt in order to meet demand while keeping costs manageable and ensuring sustainability.
Advancements shaping the frozen future
From improving visibility to leveraging artificial intelligence (AI), manufacturers are increasingly turning to advanced technology and smarter processes to overcome the unique challenges of cold chain logistics.
Technologies are now helping businesses monitor temperature, humidity and movement in real time. Imagine a truck transporting frozen fish from the coast to a grocery store. The company can track whether the temperature stays within the safe range and get alerts if it doesn’t, preventing spoilage and ensuring the product arrives fresh. This real-time visibility not only reduces waste but also allows companies to address any issues—like a delayed delivery—before they become bigger problems, improving efficiency and cutting costs across the board.
Enhanced visibility also supports better on-time performance. Frozen food deliveries need to happen within tight time frames to maintain quality. With improved tracking, companies can adjust routes or schedules on the fly. If a truck carrying ice cream is delayed due to traffic, the driver can reroute in real time to ensure the product gets to the retailer within the critical window. Cold food companies are also using eco-friendly packaging and introducing electric vehicles to lower emissions and minimize food waste. For example, grocery services use electric vans with built-in refrigeration to ensure frozen products stay at the right temperature while keeping emissions low.
Another breakthrough is the use of data tools that help manufacturers understand trends and demand patterns. With accurate data, frozen food companies can adjust their strategies based on real-time information. For instance, if a popular frozen meal brand notices a sudden uptick in demand in a particular region, it can adjust its supply chain accordingly. By having access to more precise data, companies can avoid overstocking (which leads to waste) or understocking (which leads to missed sales), helping them run a leaner and more responsive operation.
AI and automation—the buzzwords of the moment—are also revolutionizing cold chain logistics by handling repetitive tasks with speed and precision, reducing human error and speeding up operations. Supply and demand sensing are additional key innovations gaining traction. While traditional forecasting relies on historical data, demand sensing uses real-time signals to predict demand more accurately, allowing companies to adjust inventory levels in advance and avoid both stockouts and overstocking. Similarly, supply sensing tracks the availability of essential resources like packaging materials, raw ingredients, and refrigeration equipment, helping manufacturers spot shortages early and address potential production delays before they occur. Together, these tools enable more balanced inventories and minimize waste.
These innovations are helping manufacturers navigate the complexities of the cold chain more effectively than ever before. With advancements in technology and a growing focus on sustainability, the cold chain is poised to meet the rising demand for frozen foods while reducing costs and minimizing environmental impact. These changes are helping the cold chain evolve into a more efficient, agile and sustainable system, one that can adapt to the challenges of tomorrow’s market while still meeting the needs of today’s consumers.