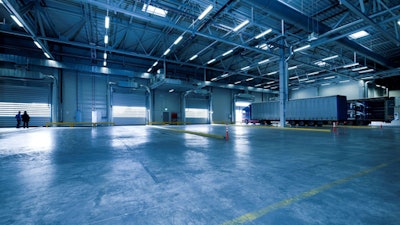
As a farmer-owned co-op since 1908, Bongards has unsurpassed cheesemaking expertise. Today, some of the biggest names in retail, foodservice and manufacturing turn to Bongards for wholesome, premium cheeses crafted to their unique specifications and sourced responsibly. Bongards has a long tradition of doing things the right way in terms of the way they service their customers and run their business. When they found its Minnesota facility, which picks, packs and ships cheese to customers nationwide, was bursting at the seams and slowing down service, they knew it was time to act.
The challenge
Growth meant it was time for a change, but Bongards was unsure whether this meant expanding to a new, larger facility or making more efficient use of its current one.
The company reached out to Conveyor Solutions Inc. (CSI), a turnkey system integrator, to begin exploring physical equipment that could help make better use of their space. CSI knew Bongards couldn’t afford to get things wrong, so they brought in Alpine Supply Chain Solutions to do a deep dive into the big picture -- an overall facility layout.
“Conveyors, picking devices and sortation systems can get expensive quickly,” says Kevin Thompson, West Coast relations builder for CSI. “We really wanted to make sure Bongards had a solid understanding of their volumes and order profiles which would drive their facility layout and physical equipment needs. This is an area where Alpine really shines, and we were glad to partner with them.”
The process
Alpine began facility design by analyzing data on Bongards' inbound and outbound shipments, inventory on hand, labor and material handling equipment to understand current business and future needs.
Alpine performed a Storage Type Analysis (STA). This exercise considers detailed SKU data, including size, shape and velocity, and assigns each SKU to its ideal storage location type based on its unique characteristics. Applying inventory rules based on individual SKU ABC categories assured the right products were assigned to the right type of pick location within the distribution center.
”Our focus was on getting product in and out of the facility with minimal touches and travel distance,” according to Michael Wohlwend, Alpine’s managing principal. “We also know that the Bongards business will continue to grow and wanted to be sure that the new layout was flexible and could handle changes, like the addition of new customers and products.”
The new layout included designated zones for bulk and broken case picking and the right sizing of the deep lane storage. Alpine also fitted Bongards with 2D, 3D and 4D push-back racking to meet Bongards storage demand.
Once the layout was complete, Alpine slotted both the broken case and full case picking areas to maximize picking efficiencies.
The outcome
The food world is moving fast. Bongards knows its customers need an uninterrupted supply of ingredients to capitalize on opportunities and win over consumers. While the team is still operating in the early phase of this initiative, productivity has been positive and efficiencies have been achieved, especially when dealing with complex orders involving multiple products. The “pick aisle” concept has proven to be a major variable enabling this improvement.
As Bongards continues to work toward streamlining processes in the mode of continuous improvement, it expects efficiency improvements to reach 20%. Pallet utilization has reached 90% with the new layout since installation of the multi-depth pushback storage solution.