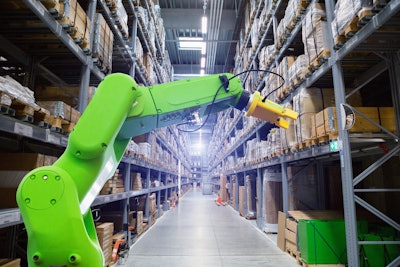
Warehouse automation has mostly been taken on by big organizations with deep pockets, but growing accessibility and maturing vendors are allowing solutions to trickle down and grow through the market. In fact, the global installed base of autonomous mobile robots (AMRs) in warehouses will surpass 500,000 by 2030, according to ABI Research.
“There are now many options to automate a warehouse. Both stationary and mobile automation solutions have continued to expand to new form factors and are becoming more effective as artificial intelligence (AI) processing grows,” says Ryan Wiggin, supply chain management and logistics industry analyst at ABI Research.
Key takeaways:
- AMRs will seep further into the industry and be adopted by more small-medium enterprises (SMEs).
- Autonomous forklifts are expected to see growing investment with more vendors entering the market.
- Europe could see much weaker growth in new warehouse construction as political pressure hinders new buildings. As a result, investment in automation and space-maximizing infrastructure will be crucial to handle increasing product demand.
“New warehouse building dropped by as much as 35% in 2023 compared to 2022 because of economic headwinds and demand shifts, with the reduction expected to continue into the first half of 2024. As construction picks up later this year, incorporating automation into new builds will be top of mind for organizations,” Wiggin states. “While automation is of key interest, companies should continue to invest heavily in augmenting their manual workers with digital devices and wearables to boost worker experience while introducing automation for basic movement tasks. The most efficient warehouses are those that focus on both areas.”