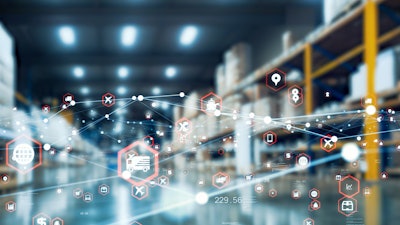
In today's logistics landscape, warehousing sorting systems are transforming how goods move through supply chains. These systems enhance efficiency, reduce costs, and elevate operational accuracy, all of which contribute to faster delivery times and better customer satisfaction.
In the era of rapid globalization and e-commerce growth, warehousing plays a pivotal role in ensuring timely and accurate delivery of products. To meet the increasing demands, businesses are integrating advanced warehousing sorting systems that utilize automation and technology to optimize inventory management, improve order fulfillment, and streamline overall warehouse operations.
The evolution of sorting systems in warehousing
Traditionally, sorting in warehouses was performed manually, requiring a significant workforce to handle products and sort them based on destination, type, or size. This process was time-consuming, labor-intensive, and prone to human error. As the demand for faster, more accurate order processing grew, sorting systems evolved to incorporate automation and data-driven technology.
Modern warehousing sorting systems employ cutting-edge technologies such as barcode scanning, artificial intelligence (AI), and robotics to automate the sorting process. These systems not only enhance speed but also reduce labor costs and eliminate human errors, driving greater operational efficiency across warehouses of all sizes.
Benefits of automated sorting systems
- Improved efficiency. Automated sorting systems handle high volumes of products with precision and speed, ensuring faster processing times and smoother workflows. This results in the ability to meet tight deadlines and manage increased demand, especially during peak seasons.
- Reduced labor costs. By automating the sorting process, companies can significantly reduce their reliance on manual labor for repetitive tasks. Workers can focus on higher-value tasks like quality control and system management, leading to improved productivity and reduced labor expenses.
- Enhanced accuracy. Sorting systems minimize the risk of errors that commonly occur in manual sorting. Using sensors, AI, and machine learning, these systems sort products based on predefined criteria, ensuring orders are accurate and inventory is properly managed.
- Scalability. As companies grow and their warehousing needs expand, sorting systems can be easily scaled to handle larger volumes and more complex sorting requirements. Systems can be customized to fit the specific needs of a business, from handling delicate items to managing heavy products.
- Real-time data integration. Advanced sorting systems are equipped with real-time data tracking and reporting capabilities, providing warehouse managers with insights into stock levels, order statuses, and workflow efficiency. This data can be used to optimize operations and make informed decisions to improve overall performance.
Types of warehousing sorting systems
- Conveyor belt sorters. Conveyor belts equipped with sensors and diverters are widely used to move and sort products. These systems are efficient for handling large quantities of goods in warehouses with fast-moving inventories.
- Automated guided vehicles (AGVs). AGVs transport items from one location to another within the warehouse. These mobile robots are equipped with advanced sensors and AI to navigate warehouse environments autonomously.
- Tilt tray sorters. Ideal for high-speed sorting, tilt tray sorters use trays to carry items and tilt them at appropriate destinations, quickly directing products to their intended location.
- Cross-belt sorters. Designed for accuracy and efficiency, cross-belt sorters are suitable for handling items of varying sizes and weights. These systems transport items on individual belt segments, directing them to designated areas for further processing or shipping.
Challenges and considerations
While the advantages of automated sorting systems are evident, their implementation comes with certain challenges:
- High initial investment. Deploying an automated sorting system requires a substantial upfront investment in hardware, software, and training. However, many businesses experience a significant return on investment over time through increased efficiency and reduced operational costs.
- System integration. Incorporating new sorting systems into existing warehouse management systems (WMS) or enterprise resource planning (ERP) systems can be complex. Seamless integration is essential for real-time data sharing and optimizing the entire supply chain process.
- Maintenance and downtime. Like all machinery, sorting systems require regular maintenance to prevent downtime and ensure smooth operation. Companies must be prepared to manage any technical issues that may arise and have contingency plans in place to avoid disruptions in workflow.
The future of warehousing sorting systems
As technology continues to advance, the future of warehousing sorting systems promises to bring even more innovation to the logistics sector. Trends to watch include:
- AI and machine learning. AI-powered sorting systems will become more intuitive, capable of learning from past data to make real-time decisions and optimize sorting routes and workflows.
- Collaborative robots (Cobots). These robots work alongside human workers to assist with sorting tasks. Cobots can handle heavy lifting or precise sorting tasks, increasing productivity without completely replacing human labor.
- Sustainability. As sustainability becomes a growing concern, future sorting systems will focus on energy efficiency, reducing waste, and incorporating eco-friendly materials in their construction.
Conclusion
The warehousing sorting system is revolutionizing supply chain management, offering businesses an effective way to enhance speed, accuracy, and cost-effectiveness. By embracing automation and integrating advanced technologies, warehouses can meet the growing demands of the global market while improving the customer experience.