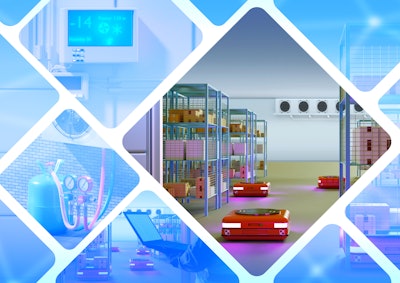
When it comes to warehouse automation, one thing is for certain: there is no one-size-fits-all. That’s because warehouse automation means something different to every company. To some, it can translate to the robotics placed throughout a manufacturing line, while others may liken it to a warehouse management system or other software full of track-and-trace alerts.
Some may even consider it to be the emerging technologies situated along the perimeter of a facility, like Internet of Things (IoT), artificial intelligence (AI) or even RFID. And of course, the automated controls tacked on to a forklift count.
Either way, 2024 is projected to be the year for major adoption and implementation of warehouse automation.
A report from Research and Markets predicts the warehouse automation market to boom over the next years, reaching $33.5 billion by 2027.
For the most part, warehouse automation has mostly been taken on by big organizations with deep pockets, but increased accessibility and mergers and acquisitions are allowing solutions to become more commonplace. In fact, the global install base of autonomous mobile robots (AMRs) in warehouses will surpass 500,000 by 2030, according to ABI Research.
Autonomous forklifts in particular are expected to see the most growth thanks to more vendors entering the market.
“There are now many options to automate a warehouse. Both stationary and mobile automation solutions have continued to expand to new form factors and are becoming more effective as artificial intelligence (AI) processing grows,” says Ryan Wiggin, supply chain management and logistics industry analyst at ABI Research.
Wearables are also seeing an extreme uptick in implementation. Over half (56%) of warehouse and logistics leaders are currently utilizing industry wearables to improve efficiency in the warehouse, according to research from ProGlove. And, 42% of respondents are certain they will invest in industrial wearables to improve warehouse operations in the next five years. Results also show that 34.5% of companies currently utilize semi or partially automated systems, and just 22% have implemented full automation.
“The potential is huge for human-machine collaboration,” says Stefan Lampa, robotics pioneer and CEO of ProGlove, “Undoubtedly, the number of organizations relying on automation will increase in the coming years. It’s an enormous undertaking that will bring with it a significant change in people’s work. However, there are many different boxes to be ticked in a warehouse’s total operations. As a result, the mental acuity, agility and problem-solving skills human workers provide will have a significant part to play for years to come. Over the next decade, connecting those human qualities with the power of automation technologies will be a key part of success.”
What warehouse automation is not though is just a trend that may soon fade away. That’s because in addition to these robotics, wearables and AI tools being providers of supply chain visibility and traceability; they’re now also considered true problem-solving solutions, prepping cold food chains for anything and everything.
Here’s why.
Filling the labor gap
The never-ending labor gap continues to pose challenges for many of today’s cold food supply chains. Whether it’s a driver shortage, office shortage or even a dockworker shortage, the labor gap is real and isn’t going away any time soon.
Fortunately, robotics, wearables and other automated tools have stepped in to somewhat “fill” the labor gap and “replace” the human worker where one currently doesn’t exist, at least for the time being.
“Robotics is about trying to fill a gap. Warehouse execution and creating more efficient flow is about trying to create, just trying to fulfill a gap. And that gap is the labor gap. The work one used to be able to do by plugging in a few extra people can't be done anymore,” says Jim Hoefflin, CEO, Softeon. “If you look at the last 10 years, automation and robotics were in more of in infancy stage, but now the sectors have accelerated because everything has shifted; people have to find solutions. The truth of the matter is, those solutions are still early, and they are improving rapidly. So, what our buyers need to be aware of is that they have to look at automation subsystems as much as possible as large operational components that fill a need in their whole ecosystem.” CLICK HERE to read our exclusive interview with Softeon.
“Done correctly and in the right environment, automation will reduce labor costs and alleviate much of the pain of employee turnover. However, we are seeing some misfires with the application of automation in warehouses where companies spend millions on machines, but it doesn’t turn out to resolve the issues,” adds Dan Waters, VP of sales for Made4net. “To do it right, you have to take a step back and determine what is driving the need or desire to automate. Automation is cool and exciting and new, but be careful that you don’t get distracted by a shiny new object. Start with your challenge and then look at potential automation solutions and vet them carefully.”
Labor gap aside, some companies are faced with hiring freezes, forcing them to implement automation in some areas where they simply just can’t hire a human body for.
“One of the key contributors to the continued rise of automation is the limited access to affordable and qualified labor. This leads to increased ramp-up times (time to competency) and places additional emphasis on retention of the staff that is performing tasks on the floor,” says Andre Luecht, global vertical practice lead for transport and logistics at Zebra Technologies. “Availability of automation has become a key motivating factor, as it reduces non-value-adding steps (walking long distances), reduces repetitive stress injuries and removes tedious and manual operations. In some environments, the deployment of automation has become mission critical as affordable labor is just not available.”
Blue Yonder’s Orchestrator is a generative AI capability that allows companies to fuel more intelligent decision-making and faster supply chain orchestration.Blue Yonder
Furthermore, “with the integration of artificial intelligence (AI), companies can offset labor shortages by automating tasks that don’t need direct involvement from workers,” adds Ann Marie Jonkman, senior director, global industry strategies, Blue Yonder. “Solutions that use generative AI, in particular, allow businesses to quickly access recommendations and predictive insights that support intelligent decision making, which goes a long way in supporting sustainability and safety measures.” CLICK HERE to read our exclusive interview with Blue Yonder.
Safety mitigation
Automated forklifts and other material handling equipment equipped with some form of warehouse automation are also in position to help companies minimize safety accidents.
“Warehouse safety accidents are occurring at a high enough rate that OSHA has launched a national emphasis program to focus on improving safety in the warehouse. While automation technology in all its forms is not a catch-all solution to these challenges, it can certainly help warehouses mitigate the impact of these challenges,” says Darrell Hinnant, commercial director, emerging technologies, Yale Lift Truck Technologies. “Plus, by adopting robotic lift trucks and other automation technologies, warehouses can reduce the risk of accidents and focus employees on more engaging tasks, ultimately increasing employee satisfaction.” CLICK HERE to read our exclusive interview with Yale Lift Truck.
Warehouse automation also provides a means for companies to maintain productivity and efficiency levels while dealing with a reduced labor force, according to Sean Wallingford, president and CEO of Swisslog Americas.
“As the technology and ease-of-use continues to advance, many companies are seeing automation systems as a viable business option that lower operational costs,” adds Wallingford. “For instance, we recently introduced the next generation of our CarryPick mobile robotic goods-to-person storage and retrieval system, which offers high scalability with low operational costs. It features faster, more agile automated guided vehicles (AGVs) to increase performance levels and shorten the return on investment for customers. The system’s scalability enables companies to accommodate growth without adding additional labor.” CLICK HERE to read our exclusive interview with Swisslog.
New solutions
From providing predictive insights and real-time analytics to automating processes, plants and even some of the human interactions, these new solutions and technologies pave the way for more integrated warehouse automation.
Blue Yonder’s warehouse execution system (WES), for example, acts as the brain of the warehouse, synchronizing tasks and data and making AI- and machine learning (ML)-directed decisions, Jonkman says.
“It orchestrates warehouse processes, material handling equipment, and robotics in a centralized hub. Warehouse execution system allows our clients to trial multiple automation technologies and determine which work best for their particular business mix without losing sight of their own business processes that make them unique. They can also quickly ramp up and down capabilities within the solution as they need them and interleave robotics automation with labor for efficient task management,” she adds. “The speed of physical automation is picking up, but some studies indicate that about 80% of warehouses are not automated at all, making this an important competitive imperative.”
Blue Yonder’s yard management solution incorporates cameras, optical character recognition and machine learning to increase yard efficiencies and decrease detention and frustration, Jonkman adds.
Earlier this year, Blue Yonder launched its first set of interoperable solutions across the entire supply chain – from planning to warehouse, transportation, and commerce – to include always-on warehouse management and Blue Yonder Orchestrator, a generative AI capability that allows companies to fuel more intelligent decision-making and faster supply chain orchestration.
Within the last year, Softeon introduced upgrades to its WMS/WES solutions, “which includes robotic interfaces and other automation implementation options designed to address the growing customer investment and innovation in warehouse automation,” says Hoefflin.
For its part, Swisslog developed ACPaQ, a robotic and data-driven case picking and palletizing solution for store-ready order fulfillment, taking single-SKU inbound stock pallets, breaking them down to cases and building them back up into mixed SKU outbound order pallets.
Swisslog also introduced the latest evolution of its robot-based item picking system, ItemPiQ, designed for repeated, reliable picking of a wide range of items to fulfill fast delivery of orders at low operating costs, streamlining and improving the order picking process.
Every aspect of the system is handled within the Swisslog family of companies, from the vision camera to the robot and the software. For reliable and effective operation in a complete Swisslog system, the robot cell can be fully integrated into the SynQ warehouse management system.
“The business case for warehouse automation has never been stronger, and the return on investment has never been shorter. Nevertheless, organizations both large and small face a significant hurdle in securing the required capital, when advancing automation initiatives,” says Wallingford. “The good news is that financial options are available today for moving ahead with warehouse automation. Previous systems would sometimes become obsolete before realizing any ROI. But the promise of performance and the ROI of new-generation systems reduce the risk for financial services companies.”
Operator assistance technologies can include automation technologies that help improve safety in the warehouse while keeping a human operator in control of the lift truck.Yale Lift Truck Technologies
And, last year, Yale Lift Truck Technologies expanded its Yale Reliant advanced operator assist solution to now be available on 13 additional Yale lift truck models. The Yale Reliant solution uses multiple detection technologies to monitor the surrounding environment and the status of the lift truck and load. Yale Reliant automatically adjusts lift truck performance and constantly monitors truck and load status to prioritize stability as it implements hydraulic and traction controls.
For its part, in 2023, Zebra introduced ET6x Series tablets, featuring generative artificial intelligence (GenAI) large language model (LLM) running on-board without needing connectivity to the cloud. Powered by Qualcomm Technologies, this tablet enables frontline workers to utilize a smaller on-device AI model.
“Automation provides most benefits in environment with repeatable, well-documented and predictable process flows,” says Luecht. “Availability of automation has become a key motivating factor, as it reduces non-value-adding steps (walking long distances), reduces repetitive stress injuries and removes tedious and manual operations. In some environments, the deployment of automation has become mission-critical as affordable labor is just not available.”
And, Tompkins Solutions partnered with Soft Robotics to deliver cutting-edge AI-powered robotics to logistics operations worldwide.
"Tompkins Solutions has been an early adopter of feeding one robotics system with another. By combining different technologies we’re offering unique solutions to our clients’ needs," says David Latona, president and CEO, Tompkins Solutions. CLICK HERE to read our exclusive interview with Tompkins Solutions.
Companies can now utilize automation and robotics to convert the more complex tasks to solve for the increasing labor shortage.Tompkins Solutions
Next steps
Whether your company is just beginning the journey toward implementing automation or if you’re still deciding on which solutions are best for your warehouse, one thing is certain, because there is no one-size-fits-all solution, the warehouse automation boom is prepping cold food chains for anything and everything.
Case in point: If you’re not thinking about automation, you’re behind already, according to Waters.
“That being said, it’s important to take your time. Reverse engineer your challenge. Identify the problem you want to address and then vet solutions that are proven to solve it. When you’re talking to vendors, ask to speak to users who look like you so you can follow the path of someone who has successfully addressed your same challenges,” Waters adds. “Expect to do a lot of research. There are many options out there, such as goods-to-person, picking robots, shuttle systems, VLM, AMRs and much more. You need a research team doing the math on all the possibilities. And be sure to find someone who has ‘gone before you,’ a company who had a very similar challenge as you and can speak directly to the results. Look at cost and production numbers before and after. What is the impact?”
Likewise, when a supply chain leader says they don't have the people in place to do a lot of the necessary work, “they understand they have to cover that need with automation sub-systems, machine learning, large language models, and artificial intelligence that will learn and identify things,” says Hoefflin. “For leaders who are considering the implementation of automation, I tell them they must figure out their needs. Are they adding autonomous mobile robots and other hardware to do the work? If so, they need to integrate and orchestrate all of the work being completed by utilizing automated technology, like a WMS and WES. They need a platform for handling warehouse data and processes that enables orchestration across various devices and systems on the warehouse floor. For best success, they need a composable platform that provides a comprehensive, bird’s-eye view of warehouse operations and enables data-driven decisions, so we know when we need to pivot if work becomes unbalanced or if we need to manage order fulfillment peaks, for example.”
Before you even start to consider specific solutions for your warehouse, perform a detailed evaluation of the entire operation to see which tasks would benefit most from automation, advises Hinnant.
“If you see certain processes that need to be sped up or are leading to particularly high operating costs, those processes would be good candidates for automation. From there, it’s all about finding an automated solution that can help your operation improve that particular task,” adds Hinnant.
Companies should also always start with the data first.
“Getting a clear and exact identification of their critical paths internally, and then extrapolating those with volume and growth to a realistic future-state environment should be completely mapped out prior to even considering automation/robotics of any sort,” says Latona. “Once they have a future-state destination to arrive at, they can explore a portion of their facility to automate. Jumping into a multi-million-dollar system from a baseline type system can be disastrous and should only include those concepts that have been properly evaluated.”
Additionally, companies need to ensure that they’re complying with food safety and regulations.
“To do this, they need active quality control and the ability to provide visibility, inventory management and temperature monitoring,” says Jonkman. “Companies should also focus on implementing automation in ways that have the most impact on improving safety of employees and food, as well as quality efficiency. It's also important to look for solutions that support sustainability efforts. In the cold food chain, many warehouses are using ammonia-based freezer and refrigeration systems to reduce energy usage. There are also automated temperature tracking and control solutions that ensure cold food products remain at a safe temperature to prevent spoilage and waste. There are opportunities to incorporate automation into the facility that can benefit overall operations. Each warehouse will also have its own physical aspects – like lights, cameras, conveyors, lifts, and HVAC equipment – that an automated solution can monitor to ensure the whole facility is running as efficiently as possible.”
All in all, because of a warehouse automation boom, the business case for warehouse automation has never been stronger and the return on investment has never been shorter, says Wallingford.
“The good news is that financial options are available today for moving ahead with warehouse automation,” he adds. “Previous systems would sometimes become obsolete before realizing any ROI. But the promise of performance and the ROI of new-generation systems reduce the risk for financial services companies. There are a number of warehouse automation technologies available today—and more coming in the future—and this can be overwhelming for organizations considering automation. But it also allows the technology to be precisely matched to the application.”
While 2024 is projected to be the year for major adoption and implementation of warehouse automation, these true problem-solving solutions are already in position to prep cold food chains for anything and everything.