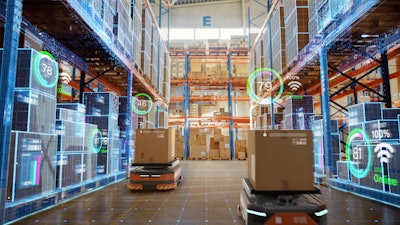
If you were to scan all the headlines about the proliferation of artificial intelligence (AI) and robotics, you’d see that most people are afraid of being replaced by emerging technologies. Writers, programmers, artists, lawyers, and even doctors are all feeling the pinch of fear that intelligent machines may take their jobs.
Perhaps unique among today’s workforce, employees in the warehousing industry report the opposite. Around 80% of warehouse workers surveyed said they were satisfied with their jobs and that recent changes in technology have been positive. In an industry experiencing challenges with employee retention, that means warehouse managers should continue the trend of investing in technology.
A lot of the challenges managers face keeping their warehouses staffed comes down to the manual nature of a warehouse job. That explains why technology is seen as a boon, not a curse to warehouse workers. U.S. manufacturing executives report that finding the right talent to staff warehouses is 36% harder than it was in 2018. With the addition of robotics and AI, a lot of that burden is lifted.
Improved safety
In a warehouse, you have a mix of humans doing boring, monotonous work with complex, heavy machinery and often tight deadlines that encourage rushing. No wonder the Bureau of Labor Statistics reports that of all industries, the transportation and warehousing industry had the highest rate of non-fatal injuries in 2021, at 4.6 per 100 full-time workers.
Many of those injuries come from employees using equipment improperly or machinery malfunctioning. It’s easy to assume that adding more machinery in the form of robots would just add more fuel to the fire. However, robots can make warehouses a safer place to work.
For example, many warehouses are beginning to implement automated storage and retrieval systems that can move products in and out of high-density storage areas. As a result, human employees avoid the physical strain of manually retrieving or storing items in tall racks or shelves. These automated systems also decrease the likelihood of injury from heavy falling loads from precariously balanced pallets.
It’s also worth noting that a lot of injuries happen because an employee is rushing to meet a tight deadline. When under pressure, people tend to be clumsier and more accident-prone – a bad combination in a warehouse full of complicated machinery and heavy boxes. By using robots, which don’t have a sense of haste, manufacturing companies can reduce the risk of accidents caused by human error.
Ultimately, robots can take over much of the heavy lifting that occurs in warehouses. That keeps human employees safer because they are relieved of physically demanding tasks that can lead to strain, muscle injuries, or accidents.
Less fear of replacement
Now that all the dangerous and boring work is managed by robots, what do we even need human warehouse employees for? That doesn’t mean robots will replace them, but it does mean automation will make their jobs better. Many finicky warehouse tasks still need human hands to select and move things, and human eyes to pick out things robot vision just can’t see.
For example, warehouse owners may find it makes sense to elevate warehouse employees to supervise and manage the robotic underlings. Human employees can ensure that the robots are functioning correctly and intervene if any issues arise. They can conduct routine maintenance tasks, such as cleaning or calibrating robotic equipment, and perform troubleshooting to identify and resolve technical problems.
And of course, while robots can handle many picking and packing tasks, there are times when only a human can make a judgment call. For instance, with items that are fragile, irregularly shaped, or have specific handling requirements, warehouse employees can use their expertise to pack these items securely, ensuring they are properly protected. Employees could also handle outlier cases like inventory discrepancies, missing items, or customer-specific packing requests.
Warehouse automation may lead to fewer manual jobs for humans, but increased efficiency and better work conditions mean more job opportunities for the kinds of tasks only humans can do.
What owners can do
That said, it can be a bit daunting to think about how to bring robots into the warehouse. Here are some ways to do so.
First, assess your specific needs and identify areas in the warehouse that can benefit from automation. If you don’t know, ask your employees. What is especially physically demanding or repetitive? Where are you seeing the most accidents happening? Those are contenders for robotic replacement. Once you’ve figured out the gaps where robots could fit, it’s time to go robot shopping. Look for technology that fits your needs, budget, and existing infrastructure.
Finally, be sure to take the time to train employees on how their roles will be changing, and how they can collaborate with their new, robotic coworkers. Ultimately, create a harmonious work environment where humans and robots work together seamlessly. You also want employees to feel comfortable telling you about areas where robots aren’t a great fit, or where there are issues or confusion. Setting up channels of open communication for discussions like this will help create a streamlined work environment in the long run.
Final thoughts
In short, robots can make warehouses safer and more interesting places for humans to work. That results in net gains for everyone. Human employees feel more fulfilled, they’re less likely to leave, and warehouse owners don’t need to spend money or time rehiring and retraining for those positions. Warehouse owners who like the sound of those benefits should look into integrating robots into their operations as soon as possible.