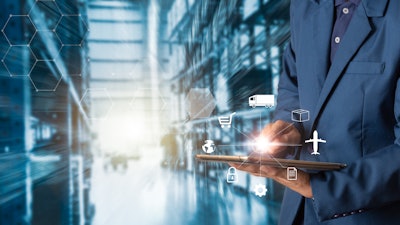
While maintaining the same operating standards year-over-year is important to ensuring boxes are continually checked across the board – from informative touring, onboarding and training to daily safety procedures and more – refreshing a plant’s approach with new, innovative solutions can take efficiency to the next level.
Prioritize communication
Here’s the scenario. The demands of your manufacturing operations don’t quite look the same as they did a year ago, or a month for that matter. Your team has followed an age-old approach to best practices that no longer meets its needs. The truth is, when the industry outpaces operations, it’s time to adapt and evolve. Keeping best practices current helps ensure that the tactics and tools utilized on a day-to-day basis remain efficient and successful on a number of levels. One of the key best practices from an operations standpoint is clear, ongoing communication. Over time, technology and tools advance, and better solutions arise that should be explored as potential additions or replacements for existing staples.
For example, communicating with individuals on the facility floor often presents a less-than-seamless experience for those attempting to convey important messages when surrounded by loud equipment, potential interruptions and more. In these circumstances, teammates may need to communicate with each other from far away or communicate with large groups on a facility tour.
For both scenarios, one solution that is often overlooked or discovered as an asset in hindsight is headsets. Whether used for special occasions or for daily function, this tool provides the benefit of clear communication, with the capability of providing both one-way and two-way interaction. Effectively tackling this key element can not only improve understanding amongst teammates, but also boost the employee experience and existing safety measures.
Encourage employee feedback
In addition to enhancing communication tools, incorporating a mobile app with feedback capability into employee offerings can pay dividends in job satisfaction and trust in the company.
From a management perspective, it’s important to know how teams are performing and keep a pulse on employee satisfaction and engagement.
Mobile apps designed specifically to encourage employee feedback and communication with their manager will organically increase engagement between parties. This in turn improves productivity, as employees are provided the opportunity to relay questions, express concerns and provide input in real-time.
Many platforms go beyond one-on-one conversations. For companies with multiple facilities or a large number of employees, mass announcement capabilities allow leaders to communicate with full teams, either on-site or across the globe, to share important information that may not warrant an in-person meeting. Ultimately, emphasizing employee feedback opens the doors for a more collaborative and transparent work environment.
Enhance safety measures
Knowledge and understanding of current policies, expectations and available equipment should always be incorporated into the onboarding process. But, what about months down the road when better procedures are discovered, or years down the road when team members have forgotten about key measures? It’s imperative that conversations around safety are an ongoing focus, as opposed to a one-time training session.
Enhancing safety measures is not limited to a well-written handbook that’s only opened when an incident occurs. Facility managers should be prepared to accommodate regular inspections to check elements such as equipment functionality, employee knowledge, safety equipment availability, PPE stock and clear hazard markings. Recurrent safety training should also be added to the calendar to ensure expectations are continually met and OSHA-compliant procedures stay top-of-mind.
However, downfalls in plant safety are not solely due to the lack of safety equipment or a proper handbook. Communication mishaps can hold great operational risk in an environment like a food processing plant. If a threat or mistake is caught by one team member, quick communication can allow for a potentially dangerous issue to be fixed before it’s too late.
Increase training opportunities
Just as best practices in any industry are bound to receive an eventual facelift, the same goes for the skillsets of employees. One of the most critical missteps a company can take is neglecting to offer ways of expanding their knowledge. Those training opportunities, whether they resemble an industry conference or a lunch-and-learn session, are key to investing in team members and their professional development. In turn, the company will grow in knowledge and credibility.
In addition to furthering employee engagement with both leadership and across teams, creating immersive opportunities promotes motivation, happiness and empowerment. While budget or capacity may limit the level of training available, providing less time-consuming options or even providing recommendations for out-of-house alternatives can show employees that the company is supportive and sees the value in their individual growth.
From a reputation standpoint, employee retention should always be a priority. The loyalty of employees is often seen as a reflection of the company’s values and mission, among other qualities that make them a suitable partner or vendor. Customers and prospective employees will almost always take a company’s perceived reputation into account before moving forward with a relationship. Above all, authenticity and sincerity are key, so those who truly put in the work to enhance company operations and culture will reap the benefits in more ways than one.
For new and existing food manufacturing plants, it's not uncommon for game-changing tools to be overlooked or underutilized. There are many moving parts and countless team members that make a plant successfully function each day. Clear communication, employee feedback, up-to-date safety protocol and training opportunities are all imperative for not only smooth operations, but also employee peace of mind.