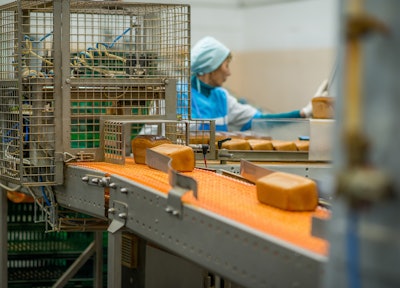
Automation in the food processing industry promises improvements in efficiency, throughput, quality and consistency as well as lower costs. But fulfilling those promises depends on two important steps that must be taken even before automation begins.
Strengthen your data
The first step is to ensure that the data used to make decisions about what to automate is reliable and interconnected to the other functions in the supply chain to understand the impacts upstream and downstream. Many organizations are dealing with antiquated systems, disparate systems, manual data manipulation or inability to transform data into insights.
Data is only as good as the strategic thinking of the people behind it, their commitment to collaboration, and the metrics used to gather and measure it. There are multiple applications for automation, including equipment automation, back-office process automation, tracking of raw materials, inventory monitoring, quality control and safety. But having a solid understanding of the reliability of your data will allow you to see the value leakage in your supply chain to determine where automation may have the most valued impact and return on investment.
Moreover, any change made in one function—research and development, procurement, operations, finance, sales or logistics—affects all the others. Automation will impact every function throughout the supply chain. For example, installing more automated equipment within processing, could free up resources that could either be eliminated to reduce overall costs or re-deployed to other functions to drive additional productivity or innovation in other areas of the supply chain. This could drive efficiencies to higher levels than predicted but could also create constraints on other parts of the organization, like warehousing and transportation. Understanding the scenarios and implications will help you prepare for the change and maximize the investment.
Optimize your processes
The second step before automation is to optimize processes across the end-to-end supply chain, from planning through operations to logistics. Automating a flawed process won’t fix the flaws. Bad processes that are automated simply create bad results faster. It is crucial to challenge and optimize your processes to ensure the right flow is occurring, the right people are involved and the right controls are in place.
A simulation of the supply chain through a digital twin or even process mapping may reveal existing bottlenecks, inefficiencies and inconsistencies that need to be cleared up first. Many organizations struggle with silos within departments and the lack of connectivity across those silos and processes. Understanding each department’s process flow and where there is a lack of process is important. Many times, this effort can identify areas where there are no formal processes and where there are multiple processes for the same tasks.
Creating uniformity and identifying the “best practice” is essential before automating. Many times, companies look at current process structure and ask, “why do we do things this way?” If you find yourself saying “because this is the way it has always been done,” then it is most likely time to review if there is a better way to do it. Taking the time to step back and analyze those existing opportunities can remove some of the low hanging fruit and enhance the impact of automation once implemented.
The simulation may also help to evaluate the ability of automation to capture the expected EBITDA, cash flow, and growth. Many automation initiatives fail because they work on paper but not for the company’s unique supply chain and unique culture. Closing the gap between theoretical improvements and actual improvements is key to making sure your investments are successful.
A particular company had spent millions of dollars by investing in automation throughout one of their manufacturing plants and distribution centers. About a year after the implementation, they were disappointed because they were not seeing the benefits that were promised to them by the automation manufacturer. After an analysis it was discovered that the proper processes for training and onboarding on the equipment were not put into place for operators and maintenance. Operators were inconsistent from shift to shift on how they managed the equipment, and proper maintenance protocols were not being followed, resulting in more downtime and wear and tear on the new equipment. The biggest lesson to learn is that processes need to be looked at and assessed before automating, during automating, and afterwards to truly optimize the value creation that you will get.
There is no doubt that automation can greatly enhance your overall company performance. For safety, quality, efficiencies and insights, automating the right areas of your business will take you to the next performance level. However, making sure you are targeting the right areas of the business and have the best foundational processes in place before driving change through automation will make the difference between fulfilling the committed savings and improvements, and having lackluster performance after implementation. The combination of reliable data, process optimization and visibility of the supply chain across planning, buying, making and moving functions ensures that automation delivers the best possible return on investment.