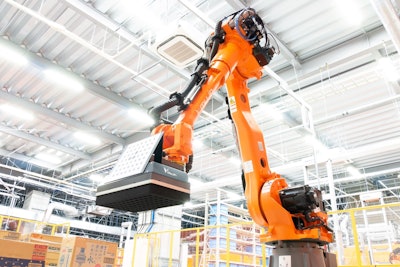
Digitalizing the supply chain is the future. But, getting there takes automation and emerging technology. It requires investing in solutions designed to track and trace, produce data analytics and deliver real-time alerts when parts of the supply chain fall off track. It requires buy-in from all decision-makers to help build the supply chain of tomorrow.
And, it’s this automation and emerging technology that helps the cold food chain build the supply chain of tomorrow.
In Food Logistics’ March/April 2022 issue, editor-in-chief Marina Mayer talks with several industry experts about warehouse automation and how automation and emerging technology future-proof supply chains.
Here’s an interview with Josh Cloer, director of sales, Mujin Corp., who says there are a number of new solutions in the market that make automating tasks previously performed by low-skill labor more feasible, with excerpts publishing in Food Logistics’ March/April 2022 issue. [CLICK HERE to read the article in full].
Food Logistics: From your perspective, what are some of the top challenges today’s cold food chains face?
Josh Cloer: Much like any distribution or fulfillment operation today, cold chains face an uphill battle with workforce turnover and lack of available resources to manage operations. With record low labor force participation rates, low skill labor is increasingly difficult to find and retain. This problem is in part due to short-term issues like the pandemic but is also a long-term trend that will extend into the future in North America. People want better jobs and higher pay, and the younger generations are finding more attractive alternative options to low-skill jobs. Continuing to rely on human labor for low skill tasks will lower competitiveness and resilience of our supply chain.
Food Logistics: And, how can warehouse automation help overcome these challenges?
Cloer: There are a number of new solutions in the market that make automating tasks previously performed by low-skill labor more feasible. Today, you can automate picking tasks for induct or fulfillment with intelligent robotics solutions. You can manage material movements within your operations with autonomous vehicles. You can store raw materials and finished goods with automated storage and retrieval systems (ASRS). The solutions are there to solve any challenge with automation, and the warehouse control and execution software is available to seamlessly connect the different solutions to fully automate your operations from door to door.
Food Logistics: The warehouse automation market is expected to grow to $27 billion by 2025; twice the size it was roughly five years ago, according to Research and Markets. To what do you attribute this growth to?
Cloer: Warehouse automation along with automation generally are at record high volumes and continued growth is expected for several reasons. First, the solutions have advanced to critical point where difficult problems can now be solved with robotics and automation. Vision systems have become more advanced and reliable, processing chips are enabling next generation software solutions, and there are now more options for the basic hardware creating more flexibility for overall solutions. Additionally, the cost of automation has lowered through standardization and economy of scale. There are new buying models allowing you to pay for automation the same way you pay your employees. When you take the labor crisis into account with the flexibility and capability of new automation solutions, starting a new automation initiative becomes a no-brainer.
Food Logistics: There are many different types of automated warehousing solutions. What kinds of emerging warehouse automation technologies do you see continuing to make an impact on the industry?
Cloer: If you have people building or breaking down pallets, there are now intelligent robotics solutions that can be deployed in a matter of days, have very low maintenance costs, high reliability and will have payback within a 2-year period. This is even true for mixed case scenarios, which were previously extremely difficult to automate. By combining 3D vision with advanced robotics solutions, you can solve nearly any picking or packing challenge that you are currently using low skill labor to manage.
Food Logistics: What advice do you have for those companies still struggling to adopt warehouse automation? Where do you envision the hang-ups being and why?
Cloer: Find a place to start. There is likely an operation within your warehouse that is perfect for automation with a reasonable payback and quick deployment. Stay away from highly custom, larger systems for now and just find the low hanging fruit. You will see benefits beyond the labor savings with things like safety and reliability improvements. Make sure you understand the full cost of each option and find a solution that gives you guaranteed performance and reliability.
[CLICK HERE to read the article in full].