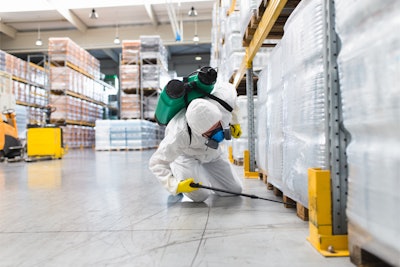
As a food manufacturer or distributor in the age of the Coronavirus disease (COVID-19), you have likely made dramatic changes to processes in order to protect staff and safeguard products.
The food industry had already made many changes over the last few years in an effort to comply with the Food Safety Modernization Act (FSMA), and these updates have provided a strong foundation in facing new challenges brought on by COVID-19.
Food safety and quality control staff are likely already taking proactive steps to maintain compliance. They have been trained to challenge the process, identify vulnerable areas of risk and work with internal teams to address concerns before they become a hazard.
It is this proactive focus that has allowed the food industry to quickly adjust to the COVID-19 pandemic. FSMA already required a deep dive into operations, focusing on prevention, surveillance and rapid response and recovery. The lessons learned in these processes can help now, as we develop frameworks and processes to mitigate the risks associated with an airborne illness that could be introduced by anyone at any time.
That’s why your pest control provider plays a valuable role in a company’s food safety system. In fact, it has never been more critical that they align their service protocols to your evolving processes than right now.
As your team adjusts in response to COVID-19 and implements policies to prepare for any future pandemics, here are some things to keep in mind regarding pest control services.
Service automation in the post-COVID-19 world is no longer just an “added bonus” offered by your pest control provider. It must be a requirement. If your long-time local provider says that they simply cannot afford these more robust, modern systems, this may force some difficult decisions. In the past, you may have conceded in this area in order to retain a trusted local partner, but in a world where the goal is to limit opportunities to transfer viruses, it is time to revisit this issue.
The good news is that competition has entered the software space for this industry, lowering automation costs for pest control providers. Several of these software platforms allow technicians to complete work orders on their phones and email the finished reports directly to a member of your staff without any physical contact. By shifting to a 100% paperless system, you can limit unnecessary contact and potential exposure.
Now is also a good time to revisit the necessity of all the devices placed in and around your facility, especially those devices located near your staff. Standards have evolved to allow for placement flexibility based on trends and previous captures. If devices are being checked in areas that would require a technician to come near your staff, you should challenge whether that device is actually necessary. If a device is not needed, remove it. If it is, be sure to require the pest control provider to check it at a time when minimal staff is present.
Even before COVID-19, remote monitoring devices with state-of-the-art sensors were starting to catch on. These devices provide real-time data and don’t have to be manually checked. While your current equipment may require some modification (and there are, of course, upfront costs to integrate the technology), the offsets in reductions in labor rates and opportunities for exposure in your facilities can’t be overlooked.
Require your vendor to provide a service process flow, so you can attempt to reduce close contact with staff. This would also provide useful information to sanitation teams, as they attempt to focus their efforts on keeping contact surfaces cleaned and disinfected. If you have a large facility, your provider may be inspecting and/or treating different areas of the facility at different times. Require them to create zone maps to keep them in controlled areas on specific days. If problems arise in other areas, they should notify your team, so those surface areas can be addressed as needed.
Communication was important before COVID-19, but it is absolutely critical now. The provider needs to report through all of the same control points as other members of your staff. It is also important that you know which other accounts your provider services. Did your technician just come from a processing facility with known positive cases of COVID-19? How are they sanitizing their equipment? Do they change uniforms and shoes between facilities? Your team should pose these questions to other vendors that enter the facility.
COVID-19 has made an impact on every industry in one form or another, perhaps none as profound as the food industry. The changes implemented in response to this pandemic are likely to remain in place for years to come. That’s why it’s vital to ensure updated processes are optimal from both a safety and efficiency standpoint. The good news is that it is possible to accomplish all of this and actually reduce pest control costs at the same time.