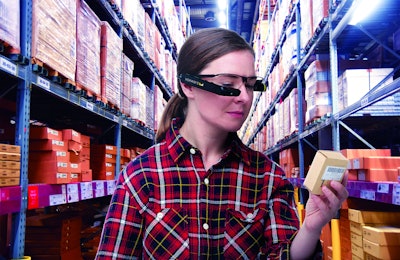
In 2020, warehouse managers will face continuing pressures to deliver goods at a rapid pace, which will require a greater agility to respond to constantly changing markets.
At the same time, warehouses are expected to process and deliver goods in bulk faster, and e-commerce continues to drive customer personalization. This is forcing warehouse managers to re-think processes in order to expeditiously address the rapid processing of “one of” orders.
The conflict between personalized “one of” orders and the ability to ship vast quantities of merchandise quickly presents a dichotomy to managers. On one hand, warehouse managers are expected to introduce new technologies and work methods to keep pace with the speed of business. On the other hand, managers must retain the ability to customize orders and stay within workable budget parameters as they strive toward operational optimization.
“Based on what we hear from customers, it’s all about throughput in the distribution center and optimizing the workforce,” says Keith Phillips, president and CEO of Voxware, Hamilton Township, N.J.
So, how can warehouse managers maximize throughput, optimize operations and yet stay within budget?
Here are several leading warehouse technologies and trends likely to shape warehouse strategies in 2020:
The power of voice
Over the past few years, voice-based technology has embedded itself into numerous warehouse process. Voice is no longer an end in itself, but instead has become an integral communication component that can operate alongside a myriad of human and automation-based work practices in the warehouse. Voice-based communications, which enable hands-free operation and greater accuracy in order and item identification, integrates with most of today’s warehouse management systems (WMS), mobile devices and appliances. Voice can operate in almost every operational phase of the warehouse—from goods intake to stocking, moving, picking, scanning, loading and querying WMS systems.
Voxware customers who rely on VoxPilot are said to see an additional 10-15% more productivity from their workforce.Voxware
“Many companies we work with tell us that they understand voice picking and the benefits that come with it, so they are looking for other ways to increase productivity throughout their warehouse,” says Phillips. “Anywhere companies have human capital deployed, they need automation to increase productivity, and voice-based technologies embellish this. We’ve almost seen voice technology come full circle. Years ago, using voice was about gaining productivity. Then, it became accuracy, and now we’re back to productivity. Companies just can’t keep up with rising consumer demands and will need to deploy technologies like voice in order to remain competitive.”
Companies will see a 20-30% increase in productivity by just deploying voice for picking alone, adds Phillips.
“We have many customers who also deploy our supply chain analytics software, and realize an additional 10-15% in performance gains,” he adds. “It’s about the multimodality of the solution.”
More flexible AS/RS
Automated storage and retrieval systems (AS/RS) that place and retrieve products from different storage locations within warehouse and distribution centers will also see their use expanded as more high-volume loads need to be processed quickly.
AS/AR’s automation capabilities reduce the need for human intervention. Reducing human involvement in storage and retrieval processes promotes warehouse safety and enables warehouse vertical and horizontal space that humans can’t access to be better taken advantage of.
A new twist to AS/RS is the ability to differentiate products, so that mixed pallets or loads of products can be produced. The need to variegate products at the pallet level is rising in the food and beverage industry, as retailers respond to the individual needs of customers and move to more “one of” orders. This change will likely generate a new wave of AS/RS technologies that will be more agile and better equipped to work with a diversity of warehouse fulfillment scenarios.
Meanwhile, at the macro level of AS/RS, the benefit to warehouses is the ability to rapidly process products and save on real estate and facility costs.
For example, Martignetti Cos. used AS/RS to consolidate two warehouses into a single 50-foot-high facility at its Taunton, Mass., headquarters. It achieved the facility savings by implementing AS/RS that could overcome the physical limitations of humans working with high stacks. The AS/RS stores and retrieves thousands of pallets per day out of its new 600,000-square-foot warehouse. Without the benefit of AS/RS technology, the company would have required an additional 150,000 square feet of floor space. Throughput is now 8,000 cases per day, compared to a former throughput of 4,000 cases per day.
Autonomous vehicles
Autonomous vehicles are also saving miles of walking on warehouse concrete floors. This is a safety and a health objective for warehouse workers, and a way to expedite warehouse operations with the power of artificial intelligence (AI), autonomous vehicles and automated forklifts.
As e-commerce and rising consumer demands force warehouse operators to process work around the clock, machines are part of the solution because they don’t wear out. Autonomous machines can also offset human labor costs.
Key areas of warehouse operations where autonomous vehicles play a role include picking and placing items and boxes, cycle inventory, load handling and moving, scanning and tracking.
Companies will continue to invest in packaging automation in 2020.Lucas Systems
Another important area of focus for warehouse operators in 2020 will be cobotics, the collaboration of humans and robotics such as autonomous vehicles working together for mutual advantage.
In the warehouse, an autonomous forklift moves heavier loads than a human, and can operate with greater safety than a forklift operated by a human operator, but the “know how” of experienced warehouse personnel who can recognize and resolve an exception situation in a workflow or innovate a better way of performing a task is still needed. Skilled employees working alongside autonomous vehicles facilitate this combniation. It will be up to warehouse managers and technology vendors to focus on
this human-machine interface and work with employees to develop best practices.
Packaging automation and process optimization
In packaging operations, warehouses can also automate by creating packages, cartons and sealing products without human assistance for repetitive processes. Line operators can quickly change the dimensions of a case or a pallet with the click of a button when working with automation. Automated robotic packaging operations can also work around-the-clock picking, placing and removing items, as well as moving empty boxes.
Given the efficiencies of packaging automation, companies will continue to invest in it in 2020. Equally important will be packaging sustainability initiatives.
“Sustainability is a major concern within the packaging industry and amongst consumers,” says John Ashby, president of Crawford Packaging, Canada. “Our expectation is, with this continued emphasis on sustainable packaging, that future packaging technologies will focus on waste reduction and recyclability. Whether that’s through replacing certain materials with more sustainable ones or by implementing simplified packaging that is both durable and lightweight, there is a significant effort to re-think packaging best practices.”
That’s why companies are encouraged to perform a packaging audit for best results.
“Unless you have a packaging expert overseeing the creation of your packaging workflows specific to your application, then there’s a good chance that time and money is being wasted in one or more areas,” says Ashby. “A packaging audit is a complete assessment of a business’s packaging practices. When a business requests a packaging audit, we send a packaging specialist on-site to identify areas for packaging optimization and improvement and work directly with the business to develop customized packaging workflows that save time, money and reduce packaging. This improves packaging efficiency.”
Workflow optimization, budget conservation and future proofing
Warehouse technology offerings and customer demands continue to expand and drive warehouse improvements, but one thing hasn’t changed much for warehouse management—the need to keep budgets under control and maximize assets already under management.
For warehouse managers, this means making careful technology “picks” to improve the warehouse, while continuing to work with legacy and other systems that have proven their value over time.
“We find many companies are dealing with legacy systems, or even have their own homegrown WMS systems,” says Justin Rotter, director of project operations for Lucas Systems, Wexford, Pa.
Companies like Lucas work with clients to integrate up-and-coming technology that can improve warehouse operations and build upon the existing technology bases that companies already have. This eliminates the need for companies to develop massive capital budgets for “rip and replace” technology projects.
Companies like Lucas Systems work with clients to integrate up-and-coming technology that can improve warehouse operations and build upon the existing technology bases that companies already have.Lucas Systems
“We can use an approach like this to migrate paper-based and older system operations to newer technologies that can optimize replenishment, picking and other processes. These newer technologies, including voice and wearable technology, can improve hands-on processes, and also give warehouse managers better visibility into warehouse workflows and into exception situations that may arise on the floor and require resolutions,” says Ritter. “Many of these solutions also use GS1 barcodes to support barcode scan and capture and product track-and-trace capabilities.”
The mixed environment of legacy systems and new technology has the potential to return investment at a faster rate, as it costs less to add new capabilities to support changing business needs and enables companies to continue running the systems already in place. It also helps warehouses gain a footing in new technologies and applications while they continue to run their older systems.
In the future, workflow optimization tools will incorporate machine learning, so that software-based analytics can provide answers to questions such as how long individual tasks should take, how to allocate workers, when to move product from one location to another and more.
Artificial intelligence tools are already in use to determine how best to combine orders for the most efficient pick sequence and then execute the appropriate sortation, so items are placed in individualized orders before being shipped.
All of these tools are needed to better orchestrate warehouse workflows to meet the growing customer fulfillment trend of “one each” picking for individualized orders.
Mindful of operating expenses and budgetary constraints, warehouse managers can be expected to choose wisely when it comes to technology investments in 2020.
At the same time, they understand that the rate at which products are now expected to be delivered and the growing demands of customers will not abate.
The personal success of managers—and of the warehouses they operate—will depend upon meeting the dual and sometimes conflicting goals of agility and speed.
In this environment, technology offers the best answers for both.
“There are a lot of companies that have been slow to adopt technology in the distribution center,” says Phillips. “With the current economy and the labor shortage still very prevalent, we believe that companies that do not automate will struggle to remain competitive.”