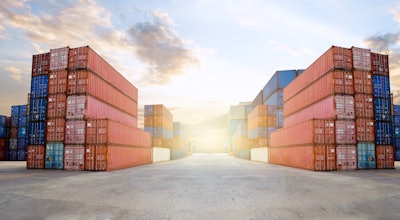
On March 23, a stranded Evergreen container ship blocked navigation in Egypt’s Suez Canal. Experts claimed a lack of visibility forced the 224,000-ton ship named EVER GIVEN, said to be the largest ship in the world, to run adrift and tip on its side while en-route to China, creating the largest supply chain disruption in 2021 to date.
Six days later, after hours of digging, tugging and pulling, the around-the-clock international effort eventually freed the massive vessel and re-opened the shipping lane.
While the re-opening of the Suez Canal sent cheers and celebrations around the world, it also set the stage for what became a domino effect of supply chain disruptions.
In Food Logistics’ May 2021 issue, editor-in-chief Marina Mayer talks with several industry experts about the Suez Canal crisis, the importance of supply chain visibility and what’s in store for the future in terms of mitigating supply chain disruptions.
Here’s an interview with Nikolaus Sievers, VP, global customer success for Slync, with excerpts publishing in Food Logistics’ May 2021 issue. [CLICK HERE to read the article in full].
Food Logistics: From your vantage point, what are some of the top challenges and/or opportunities pertaining to ports and ocean carriers? And, why?
Nikolaus Sievers: Ports and ocean carriers are a critical piece and oftentimes bottleneck. Up to 80% of industrial and consumption goods that keep our globalized economy going are moved in containers; this states the significance of this industry, but also underlines the dependency on it. The recent event with EVER GIVEN blocking the Suez Canal clearly showed the implications and risks from container capacity and ports or canals becoming a bottleneck.
Major topics that ports and carriers in the containerized ocean space have to deal with evolve around scale, standardization and partnerships.
The scale has increased significantly. A decade ago, peak season and related capacity shortage would have been a few months per anno on key trades. Today, it has turned into the opposite, where now only a few months of the year are considered slack season.
Ocean carriers have continually increased vessel sizes to increase economies of scale, which poses risks and challenges on ports in terms of throughput and hinterland capacity. The imbalance of equipment is another major issue this industry sees. Empty containers are never where they are needed, i.e. they are missing in inland depots and are short in key export markets. Empty positioning is a costly exercise.
Overall, carriers and ports struggle with a lack of standards. With the amount of involved parties in this business, common platforms and means to exchange information, like schedules, are key. There are some industry initiatives that are however taking a long time to come to life. In the meantime, ports, terminals, carriers and alliances often rely on manual ways of interacting. In some areas, a certain level of intransparency is to the benefit of these market players, hence no major need to change for the better of the industry and its customers, being shippers and their logistics service providers.
A critical piece for ports and carriers are strong partnerships. Ports are dependent on terminal operators, inland depots, overland transport providers, as well as other ports in the world that ship between one another. Carriers are dependent on the partners in their alliances. We have seen the ocean carrier market go down from 30 global carriers two decades ago to around eight global carriers today.
Some ports and carriers manage these challenges well, others do not. The ports of Rotterdam, Singapore, Duisburg, for instance, are at the forefront of digitalization and creation of string networks. Maersk is continuing to dominate the market in pioneering digital practices and new business models. Zim and OOCL, now COSCO, are considered to be more digitally advanced carriers.
A place where both parties, ports and carriers come together to jointly improve and connect their businesses are the consortia that have evolved on the basis of blockchain, like TradeLens and GSBN, but are not dependent on blockchain technology and rather create value from common processes being established.
Food Logistics: How is technology being used to solve some of these challenges?
Sievers: Ports and ocean carriers have naturally been more focused on physical processes and are only now beginning to exploit the potential of converging physical and digital flows.
[Digital Container Shipping Association] plays a major part in driving the definition of standards in the industry. One key component is the way how data is exchanged between parties. There are several initiatives that strive to evolve from reliance on EDI methods and standards to use of APIs allowing to connect more efficiently and seamlessly.
Most carriers are driving initiatives to install better portals to improve their customers' digital experience, but it is questionable how much the use of portals is really improving connectivity of parties.
The use of common platforms and community software has been and is continuing to play a key role for carriers and ports. But, there is a fine line for carriers and ports between benefits from being connected well and making oneself a commodity allowing customers to quickly switch based on capacity and pricing changes.
Food Logistics: Despite the impact of COVID-19 on our nation’s supply chains, ports and ocean carriers remained undeterred. Instead, they pivoted to become “smarter.” How and/or why did this happen?
Sievers: Ports and carriers have been striving to become “smarter” for a while now, ever since the digitalization wave came knocking on everyone’s door. All that COVID-19 has added is a focus on supply chain and pressure to react to volatility.
Before COVID-19 and the recent EVER GIVEN incident, many people were not quite aware of or interested in the significance of transport, logistics and supply chains. For different reasons, being vaccines, missing toilet paper, massive vessel backlog in Suez, etc. the public eye has been on supply chain topics more than before.
I would disagree that ports and carriers have been entirely undeterred. Ports definitely struggled with the impacts of massively decreased volumes during COVID-19. Carriers had to deal with vessel orders and overcapacity during 2020, larger vessels were not needed as much as medium-sized ones, etc.
Ports that had already been “smart” prior to COVID-19 have been able to weather the storm and work more efficiently than those ports that already struggled prior to COVID-19.
What has definitely benefited carriers is the consolidations of the last years, and the fact that for the first time, they have not engaged in an unsustainable pricing war once demand picked back up, but rather kept rates stable at a higher more sustainable level, resulting in greater profitability. This is an unusual situation and fewer carriers are executing their market powers over shippers up to a point that China and other regulators have started questioning and reviewing the system of alliances in place.
Food Logistics: What is the potential impact of the Suez Canal blockage on the global supply chain?
Sievers: The main impact we see on global supply chains is that of lost sales and added costs. Lost sales from not having the product at the point of sale when required and added costs from unplanned events such as dead freight of trucks ordered to pick up containers that have not arrived or been cleared.
COVID-19 has already put a major strain on supply chains as it is, transit times across the Pacific for instance have tripled in duration. This has a massive impact on planning cycles and bound capital. The Suez Canal blockage amplifies some of the challenges already imposed by COVID-19.
Food Logistics: How has it been / will it impact ports and carriers?
Sievers: Ocean freight depends on a steady circular flow of goods. Vessels move on so-called service loops. Containers move from one region to another and back. Ports are designed to handle a certain capacity.
Empty moving vessels or containers and idle space in ports and warehouses are as bad as overbooked ships and congested terminals.
Volatility and imbalance disrupts the system. And, this is exactly what the Suez Canal blockage caused. The trade lane that is most affected by this is the one between Asia and Europe; less so other large trade lanes such as transpacific and transatlantic.
There is a ripple effect from this event. Downstream, there is a massive congestion at European ports, berthing slots are blocked, vessel waiting areas in front the of the ports are overly busy, terminals will struggle to have enough space for full and empty containers, hinterland infrastructure will be completely overloaded. Upstream, in Asian ports, vessels and equipment that should have come back from Europe will be in shortage, i.e. a major shortage in capacity, and thus delays in being able to move freight.
Ocean schedules will be disrupted for months to come. A main impact will be the need for constant replanning by all involved parties, and with systems not being in sync, this causes bullwhip effects.
Food Logistics: How could carriers better plan for incidents like the Suez Canal blockage to avoid these problems in the future?
Sievers: Problems like the Suez Canal blockage can hardly be avoided. In the logistics world, there are certain instances that are called force majeure, which refers to unavoidable occurrences. Also, there are bottlenecks in physical supply chains that always bear a risk of causing disruptions when affected.
The focus should be on mitigation of supply chain risks. A general approach would be to diversify. For carriers, this could involve relying more on mid-sized vessels and higher number of services instead of consolidating their offering into fewer larger loops.
Where the physical nature of supply chains cannot be changed or avoided, the key is how parties such as carriers manage their information. Connected information and close collaboration with partners and customers is key. This is an area in which carriers have much room for improvement. Schedule data for instance is oftentimes managed in disparate legacy systems. Carrier’s fleet management teams are not well connected with the booking management systems. This causes time lags and inaccuracies, which is fatal in situations such as the one caused by EVER GIVEN.
Food Logistics: When these problems do arise, how can carriers leverage technology to their advantage?
Sievers: Carriers and ports lack a dedicated set of standards for scenario/contingency planning and communications. It’s up to [logistics service providers] and shippers to treat these entities like any other node in the supply chain. While a shipper or LSP can’t enforce standards with a port, carrier or many other third parties, they can work to digitize their own processes and data to bring critical communications, documentation and exception management tools into a single place. It calls attention to the need for systems that bring all data, especially unstructured data like emails, PDFs and any other incoming external data, together so these companies can quickly identify exceptions, escalate them and take appropriate action to deliver the swift response shippers demand in these situations.